Asphalt Concrete(Bituminous Concrete) is an entirely controlled, hot-mixed, hot-laid, plant mixture of well-graded dried aggregates, filler and paving bitumen in best proportion as per requirements when compacted, forming a dense material Layer of thickness 25-100mm on a previously prepared granular, modified granular or Dense Bituminous Macadam (DBM) as per the specification.ย ย
Also, Read: Dense Bituminous Macadam (DBM) Construction Requirements
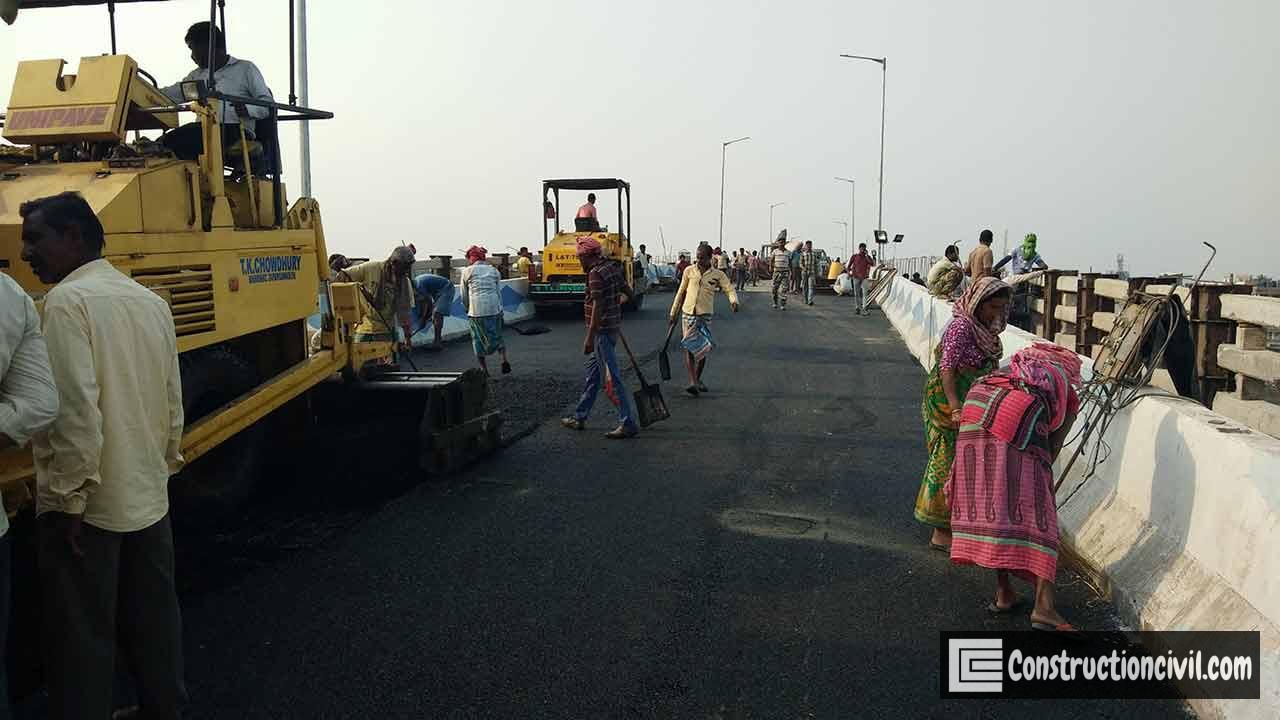
Construction Materials for Asphalt Concrete:
Binder:
An appropriate type of bituminous material is commonly used for Asphalt Concrete mix as a binder complying with the relevant standard specifications or otherwise specified. Bitumen shall be viscosity graded bitumen or Polymer modified bitumen complying with IRC & MORTH specification, obtained from an approved source.
Coarse Aggregates:
Coarse Aggregates consist of crushed rock retained on the 2.36 mm sieve. They shall be clean, hard, durable of the cubical shape, free from dust and soft or friable matter, organic or other deleterious substances. Aggregate meeting all the physical requirements specified in table 500-18 of MORTH for Bituminous Concrete construction.
Fine Aggregates:
Fine Aggregates consist of crushed stone passing on a 2.36 mm sieve and retained on a 75-micron sieve. They shall be clean, hard, durable, dry and free from dust and soft or friable matter, organic and other deleterious matter. Fine Aggregates shall have a sand equivalent value of not less than 50 when tested according to IS 2720 part โ 37, and the Plasticity Index of the fraction passing the 0.425 mm sieve shall not exceeding 4 when tested in accordance with IS 2720 part โ 5.
Filler:
Filler shall be finely divided hydrated lime or cement as approved by the Engineer. The filler shall satisfy the grading requirements, as indicated in table 500 – 8 of MORTH.
Aggregate Grading and Binder Content:
The combined grading of coarse aggregates, fine aggregates and added filler when tested following IS 2386 part I (Wet Grading Method) shall satisfy the limit specified in table 500 -20 of MORTH.
Prime Coat / Tack Coat:
It shall be Bitumen Emulsion of grade CSS 1h as per ASTM D โ 2397 or ASSTHO M 280 โ 96.
Also, Read: Prime Coat and Tack Coat using Cationic Bitumen Emulsion for Road Work
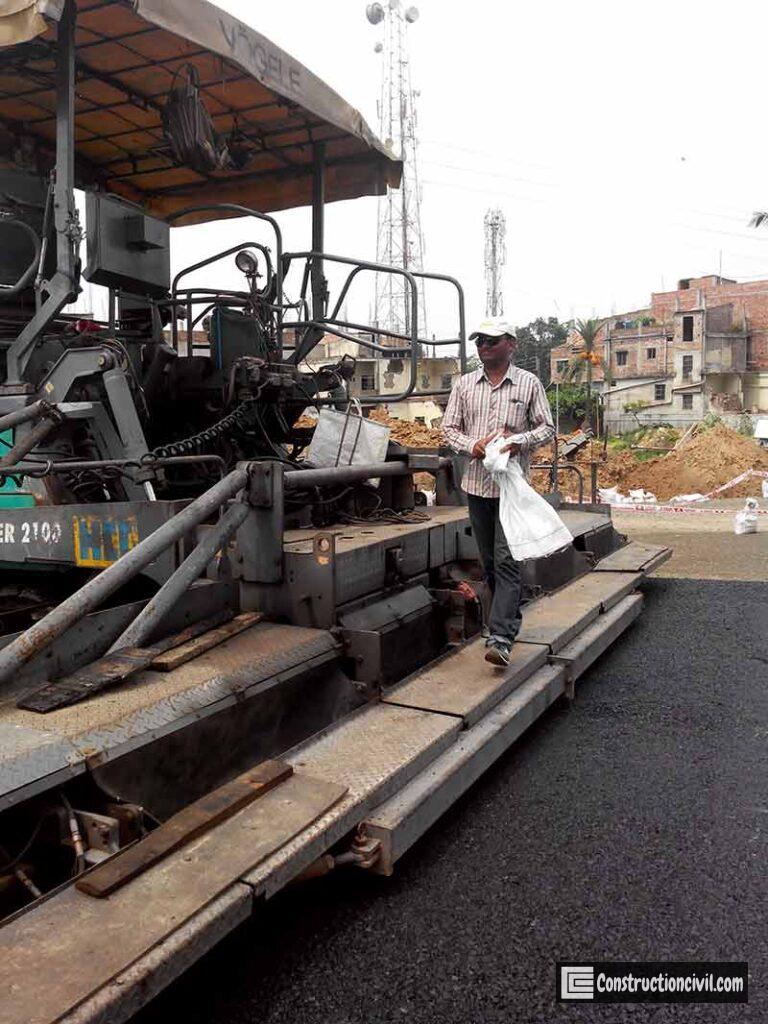
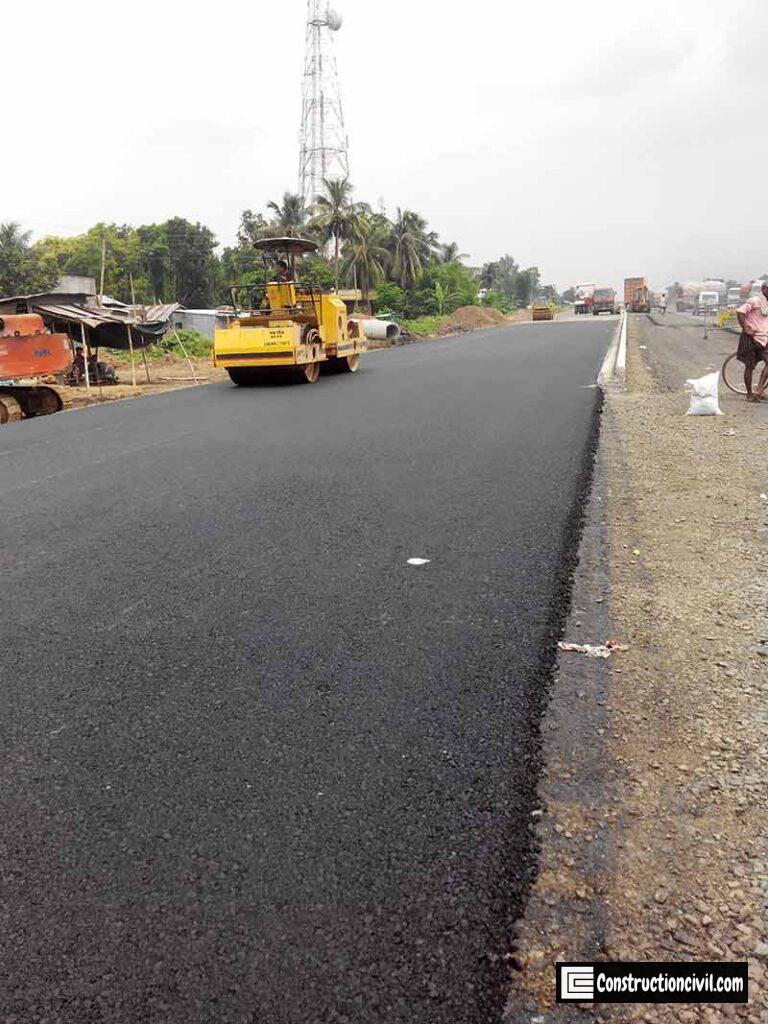
Plants, Equipment and Machinery for BC Construction :
The following equipment and machinery required for the execution of BC works:
- Hot Mix Plant
- Vibratory Tandem Roller
- Pneumatic tyre Roller – 12 to 15 mt. dead weight
- Sensor Paver
- Pneumatic Blower
- Water tanker
- Tippers and Dumpers
- Broomer
- Air compressor
Asphalt Concrete Trial Patch:
The full-scale laying and compaction trials shall be carried out with the approved mix design for asphalt concrete proposed for the permanent works using the Plants, Equipment, Machinery and the methods proposed.
- The trial patch shall be at least 100 sq.m and the full construction width and depth for the material.
- The Pavement layer trial shall be undertaken ahead of the proposed work to commence full-scale work of that layer.
- We shall record the following data during trial patch construction: The composition and grading of the material, including the binder content, type and grade of bitumen, temperature of the mix (after discharge from the mixer, before dispatch from the plant, on commencement of laying, on the start of compaction and completion of compaction), the density of mix, number of passes of rollers to achieve the specified degree of compaction, air voids, and Marshall properties of the mix.
- The trial patch shall be deemed successful if all specified sets of results over the range of compactive effort meet the material’s specified requirements.
Survey and Setting Out Works for Bituminous Concrete:
After completion of the DBM Layers as per construction drawings, we have to mark the limits of asphalt concrete as per the established grid lines and Bench Marks etc. and as per approved construction drawings.
Preparation of Base for BC:
The base on which asphalt concrete or bituminous concrete is to be laid shall be prepared to the specified lines, grade and cross-sections in accordance with clause 501 and 902 of MORTH or as specified. Loose materials and foreign matters shall be removed by thorough brushing with mechanical brooms and/or blown off by compressed air or other acceptable means.
Tack coat:
The tack coat shall be applied over the bituminous bound surface before laying the asphalt concrete mix according to provisions of clause 503 of MORTH and approved methodology.
Asphalt Concrete Construction Procedure:
Preparation of Mix and Transportation:
- We shall prepare the asphalt concrete mix in the Hot Mix Plant as per the approved mix design complying with MORTH specifications.
- The plant shall have automatic controls that coordinate the proportioning, timing, and discharge of the mixer.
- The bitumen tank with an agitator which is continuously agitating the bitumen shall be capable of maintaining its contents at the specified temperature. Bitumen delivered to the mixing plant via insulated pipes such that heat losses are minimized.
- The dryer shall be of the rotating drum type capable of heating the aggregates to the temperatures outlined in this specification.
- The PMB shall be heated at the specified temperature so that it can be distributed uniformly.
- The aggregates shall be heated to a specified temperature to be mixed within the temperature range of 165ยฐC to 185ยฐC.
- The temperature difference between the binder and the aggregate shall not exceed 14ยฐC.
- Proper mixing is required as all particles of the aggregates are coated uniformly, and the discharge temperature of the mix shall be 185ยฐC, maximum.
- Bituminous mixes shall be transported to the laying site by dumpers covered with tarpaulins and shall be kept free of contamination and segregation during transportation.
- Dumpers used for hauling the mix shall be adequately free of petroleum oils, solvents or other materials that adversely affect the mix.
Laying of Asphalt Concrete:
- The asphalt concrete mix shall be laid by a self-propelled sensor Paver equipped with a hopper, delivery augers and capable of spreading, tamping and finishing the mix to specified grade, lines and cross-section, flush with the road kerb. It shall be capable of laying the mix with no segregation, dragging, burning or other defects and within the specified level. Surface regularity tolerances shall meet the specified as per clause 509.6 of MORTH.
- Immediately after receiving the transported materials from the hot mix plant at site, the Paver shall spread on the prepared and approved DBM surface.
- We shall place the asphalt concrete mix in the full width of the flexible Pavement. The compacted thickness of the asphalt concrete layer shall be as per specification requirements.
- We have to ensure continuous laying to avoid continual stop and start fashion and coordinate the Paver’s speed with the feeding limiting to no drag condition.
- Paver shall have an accurate screed unit for maintaining the screed. The automatic screed unit shall keep the screed at the specified longitudinal and transverse slope within the plus or minus tolerance.
- In areas with restricted space where Paver can not be used, the material shall be spread, raked and levelled with suitable hand tools and compacted to the Engineer’s satisfaction.

Also, Read: Dense Bituminous Macadam (DBM) Preparation and Laying Methodology
Compaction of the Laid Mix:
- We shall use a sufficient number of rollers of appropriate types, size and weights to achieve the specified compaction.
- Compaction asphalt concrete layer shall be completed before the temperature of the asphalt mix falls below 115ยฐC.
- Rolling shall be continued until the layer under compaction has attained the specified degree of compaction.
- Initial or breakdown rolling shall be completed with the help of 8-10T dead weight smooth wheeled rollers.
- The Rollers shall be operated with a uniform speed not exceeding 5 km/hr.
- Intermediate rolling shall follow immediately after a deadweight(8-10T) vibratory roller. It shall be followed by intermediate rolling with a Pneumatic tyre roller of 12-15T weight having a minimum tyre pressure of 5.6 kg/sqm.
- The finishing shall be done to eliminate marks from previous rolling with 8-10 tonnes smooth wheeled tandem Roller.
- The Roller wheels shall be kept lightly moistened with a water sprinkler fitted with the roller to prevent adhesion of the asphalt mix to the Rollers.
- Rolling shall commence at the edges and progress towards the centre longitudinally except that on super elevated and unidirectional cambered portions, it shall progress from the lower to the upper edge parallel to the Pavement centre line.
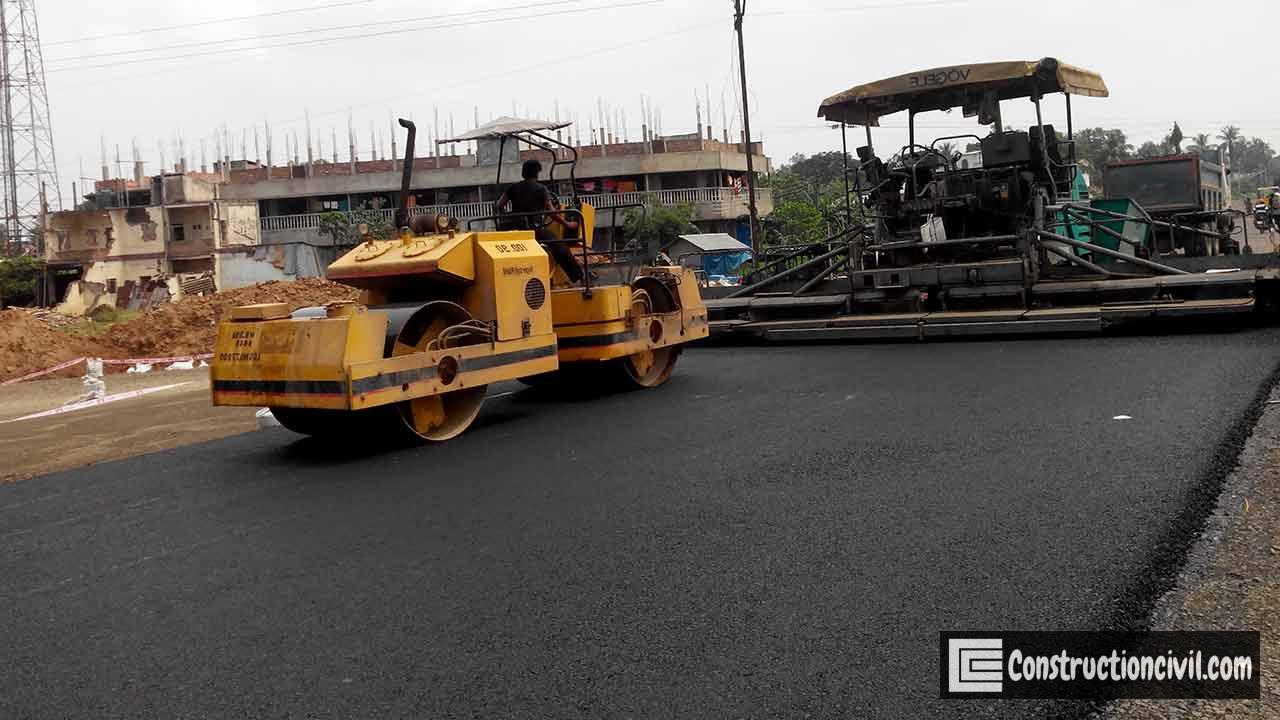
Finishing of Edges:
- The roller shall roll the edges of the asphalt concrete layer concurrently with or immediately after the finishing.
- In case of rolling the edges, roller wheels shall extend 50 mm to 100 mm beyond the bituminous concrete layer’s edge.
- Any mix that becomes loose or broken, mixed with dirt or foreign matter, or defective shall be removed and replaced with fresh hot mix manually and compacted.
- Any fresh mix on the existing work shall be removed carefully, sweeping it back to the uncompacted work to avoid the formation of irregularities on the previous face.
Surface Finish:
The surface finish of construction shall be conforming to the requirements of clause noโ902 of MORTH.
Limitations To Construction:
Laying of asphalt concrete not permitted while free-standing water is present on the surface over which BC to be laid or during rain, fog and dust storms. After the rain, the water present over the Bituminous surface shall be blown off with a high-pressure air compressor, or the surface left to dry before Bituminous Concrete(BC). Laying of asphalt concrete mix shall not be carried out when the ambient temperature is below 100ยฐC or when the wind speed at any temperature exceeds 40 km/hr at 2.0m height unless specifically approved by the Engineer.
Reference:
- MORTH โ Specifications for Road and Bridge Works (Fifth Revision) Technical Specifications
- Relevant BIS/ASTM/ BS standards/codes cross-referred elsewhere in this methodology.

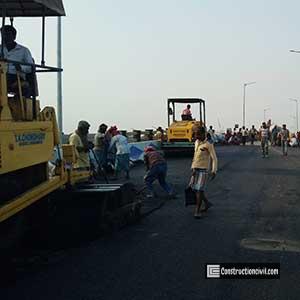
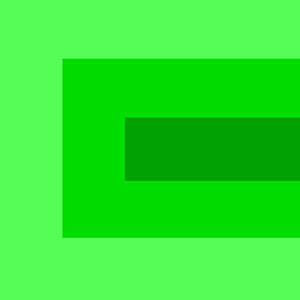