What is Concrete?
Concrete is the largest consumed human-made heterogeneous material. Ordinary concrete made by mixing cement(inorganic material), water, natural sand or stone dust, natural stone and admixture. The aim is to combine these Concrete Ingredients as per designed ratio to make concrete easy to transport, place, compact and finish and which will set, and harden, to give a durable and robust product.
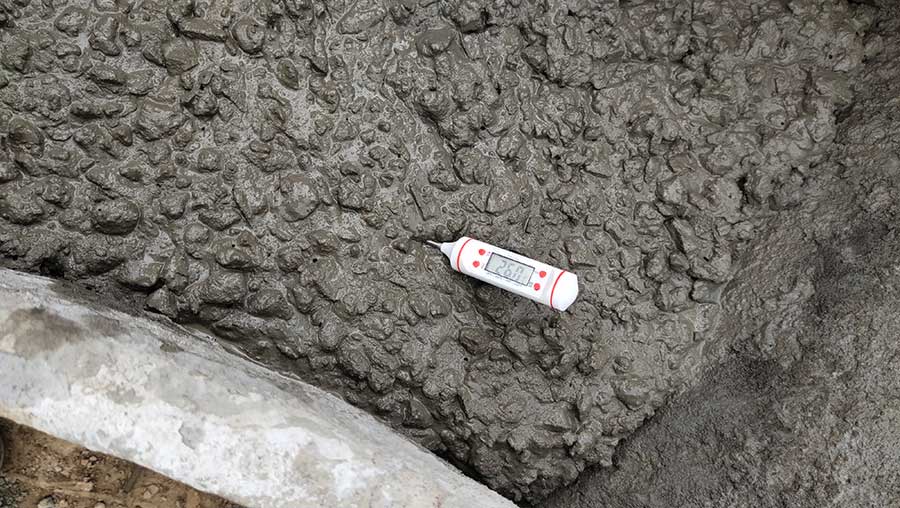
Also, Read: Properties of Concrete – Introduction to Good Concrete Practice
Advantages and Disadvantages of Concrete Mix:
Advantages of Concrete Mix:
- Ingredients are readily available.
- Low life-cycle cost
- Can easily be handled and moulded to any desired shape
- Robustness
- Can be designed for selected properties
- Due to the monolithic character of concrete, it gives a better appearance and much rigidity to the structure
Also, Read: Design Mix of Concrete – Detailed Procedure With Calculation
Disadvantages of Concrete Mix:
- Low tensile strength
- Low ductility
- Demands strict quality control
Concrete Ingredients:
Cement:
It is necessary to use cement as concrete ingredients of appropriate grade and type for specific applications and environmental conditions. The following varieties of cement for concrete are used for Bridge/Structure construction work.
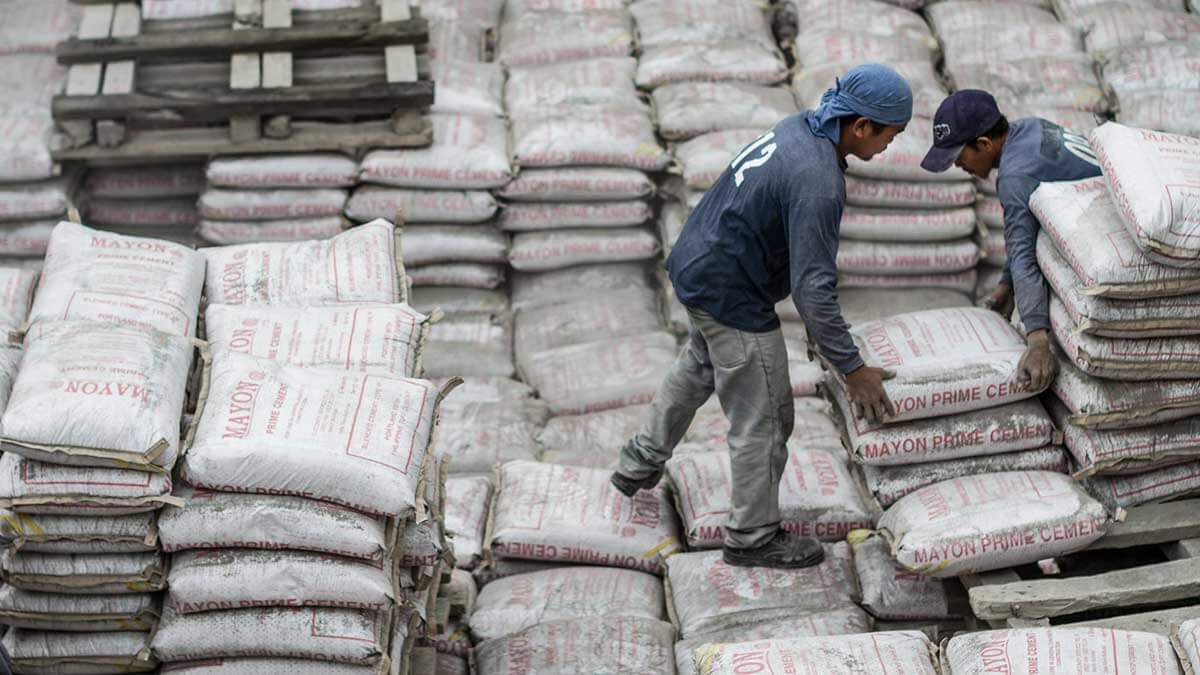
Also, Read: Rusting of Iron Rebar in Concrete – Special Repairing
varieties of cement | Grade | Suitability for usage |
Ordinary Portland Cement (OPC) for concrete IS: 269-2015 | โ Grade-33 โ Grade-43 โ Grade-53 | โ Up to M20, grouting of cable ducts in PSC works โ Up to M30, precast elements, marine structures, etc. โ A grade higher than M-30, PSC works |
Portland Slag Cement (PSC) for concrete IS:455-1989 | Manufactured by either inter-grinding in the OPC clinker, Gypsum and Granulated Slag or blending the Ground Granulated Blast Furnace Slag (GGBS) with OPC by mechanical blenders. | โ Marine and offshore structures โ Locations expected to be attacked by chlorides and sulphate ions โ Sewage and water treatment plant |
Portland Pozzolana Cement for concrete: IS: 1489 (part-I) IS: 1991 (fly ash based) | A kind of Blended Cement produced by either inter-grinding of OPC clinker, gypsum and pozzolanic materials in certain ratio or grinding the OPC clinker, gypsum and Pozzolanic materials separately and thoroughly blending them in a certain ratio. | โ Hydraulic structures- dams, retaining walls โ Marine structures โ Mass concrete works โ Aggressive conditions |
Rapid Hardening Cement for concrete IS: 8041-1990 | Similar to OPC, but gains more strength rapidly. Gives much greater heat of hydration | โ Prefabricated construction โ Cold weather condition |
Also, Read: Blowholes/Surface voids/Bugholes in Concrete Surface
Physical Characteristics of Various Types of Cement as per IS:
Types of Cement | Fineness (m2/kg) min. | Soundness by Le-Chatlier (mm) max | Initial Setting time (minutes) | Final Setting time (minutes) | Compressive strength (Mpa) |
OPC 33 Grade cement for concrete IS: 269-2015 | 225 | 10 | 30 | 600 | 33 |
OPC 43 Grade cement for concrete IS: 269-2015 | 225 | 10 | 30 | 600 | 43 |
OPC 53 Grade cement for concrete IS: 269-2015 | 225 | 10 | 30 | 600 | 53 |
Portland Pozolana (PSC) Cement for concrete IS:1489-1991 | 300 | 10 | 30 | 600 | 33 |
Portland Blast Furnace Slag Cement for concrete IS: 455-1989 | 225 | 10 | 30 | 600 | 33 |
Rapid Hardening Cement for concrete IS: 8041-1990 | 325 | 10 | 30 | 600 | NS |
Also, Read: Causes, Prevention and Repair of Concrete Surface Defects
Deliberations needed by BIS:
- Considering the hot weather conditions in India, it is necessary to insist on a higher initial setting time for cement, e.g. about 60 minutes.
- Chloride content: It is an essential requirement from durability consideration.
- Manufacturers produce major Concrete Ingredients cement with increased fineness to improve compressive strength. Not desirable in hot weather concreting. The upper limit of around 280 should be specified.
- The heat of Hydration: No limit specified in IS. for hot weather concreting it should be (i) 7 days < 270 Kj/Kg and (ii) 28 days < 320Kj/Kg. For cold weather, it should be more.
Storing of Cement at Site:
- Cement store godown should be dry, leak-proof and as moisture-proof as possible
- cement bags should be stack on wooden platform 150-200mm above the floor top of cement storage godown.
- The floor may include lean cement concrete or two layers of bricks laid over well-compacted earth.
- Storing of cement shall be done in such a way that The height of each cement bag stacked should not be more than ten bags of cement.
- Cement bags should be stack close to each other.
- The height of each cement bag stacked should not be more than ten bags of cement.
- The width of the stack should not be more than four cement bags
- Bags should be placed alternately length-wise and cross-wise
- Stack to facilitate use in the order in which they arrived.
- Put label showing date of receipt of on each bag
- Enclose the stack by a waterproofing membrane/tarpaulin
- Stack different types of cement separately in the godown.
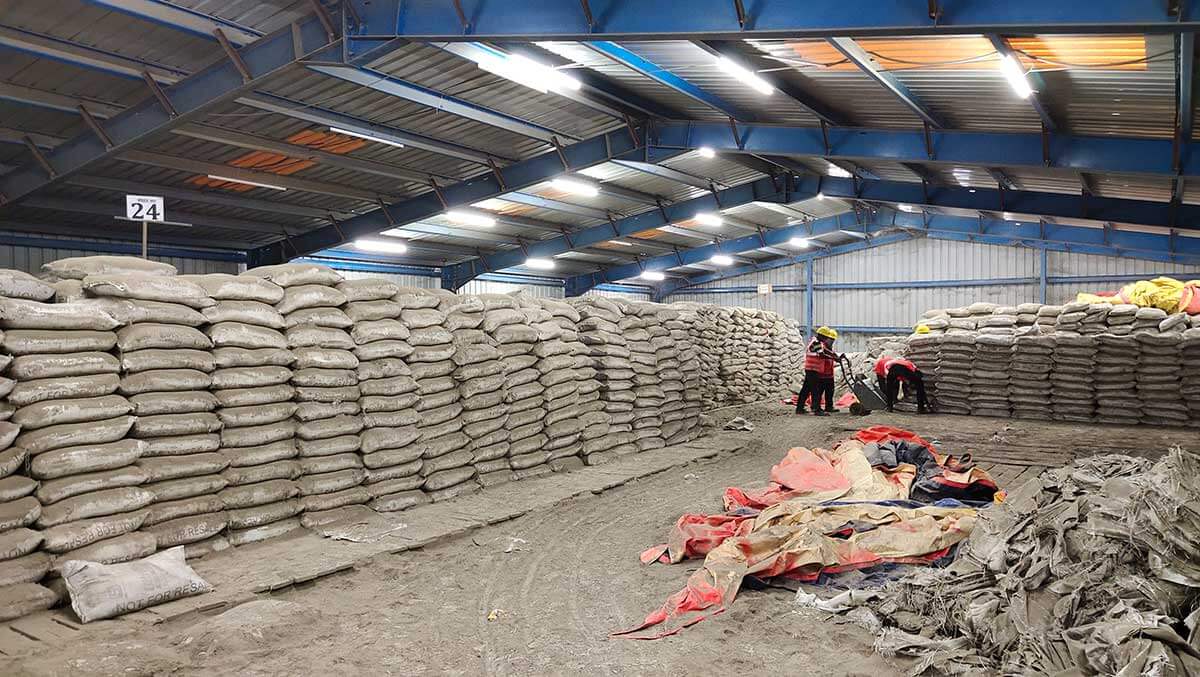
Also, Read: Nondestructive Testing of Concrete – Methods & Guidelines
Coarse and Fine Aggregate:
Most important concrete ingredients aggregates play an essential role to establish the properties of concrete such as water-cement ratio, cohesiveness and workability of concrete in plastic stage, while they affect compressive strength, density, durability, permeability in the hardened stage. The following tests are conducted to determine the quality of aggregate for concrete:
Also, Read: Determination of Sieve Analysis For Fine Aggregate
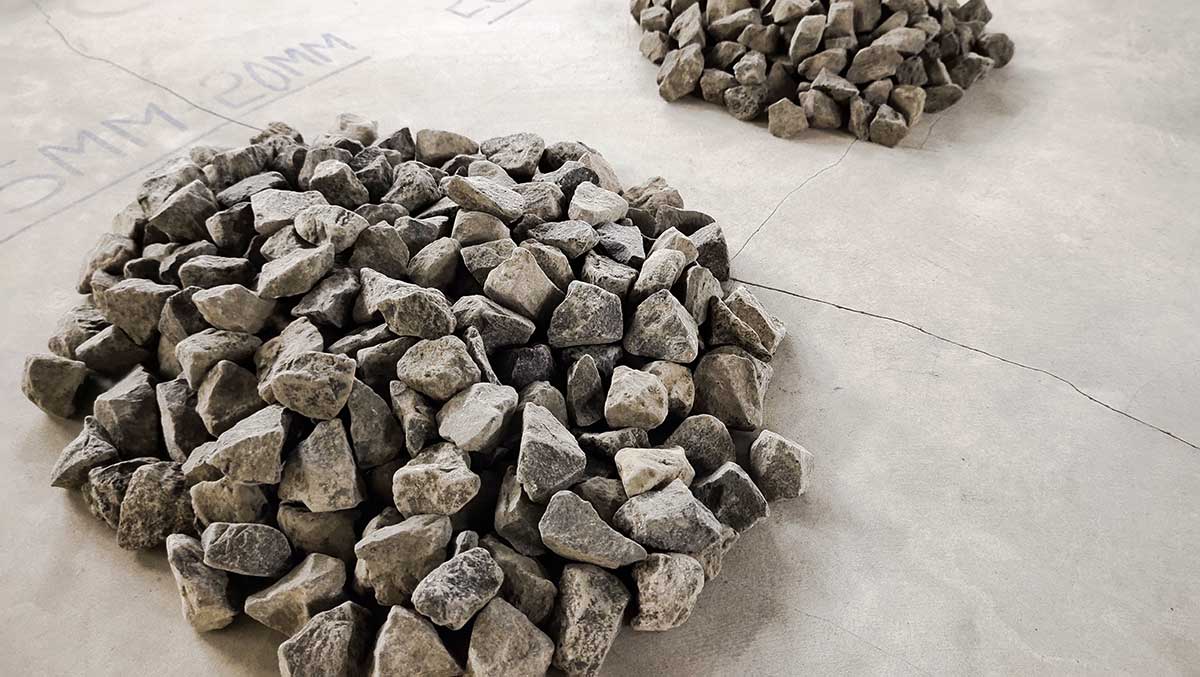
Also, Read: Sieve Analysis of Coarse Aggregate Test – Construction Civil
- Gradation
- Estimation of deleterious materials and organic impurities
- Combined Flakiness and Elongation Index
- Aggregate Crushing Value
- Aggregate Abrasion Value
- Soundness of Aggregate
- Alkali Aggregate Reactivity
Water:
The following tests are conducted to determine the quality of water for concrete mix:
- pH value
- Limits of acidity
- Limits of alkalinity
- %age of solids
- Chlorides
- Suspended matters
- Sulphates
- Inorganic solid
Also, Read: Factors Affecting Strength of Concrete – Construction Civil
Admixtures:
Chemical Admixture for Concrete:
Used as specific property/performance enhancer. Chemical admixture can be classified by function as under:
- Water reducing admixture
- Plasticizer for high slump or flowing concrete
- Accelerating admixture
- Retarding admixture
- Shrinkage reducer
- Corrosion inhibitor
- Air-entraining admixture
- Foaming agent
Mineral Admixture for Concrete:
Mineral admixtures are used as concrete ingredients for the improvement of long term strength and durability performance. Mineral admixture include
- Fly ash
- Silica fumes
- Ground granulated blast furnace slag
- Rice husk ash
By using the above two types of admixtures together, high strength and high-performance concrete may be designed.
Also, Read: Formula for Development Length, Anchorage and Lapping Length

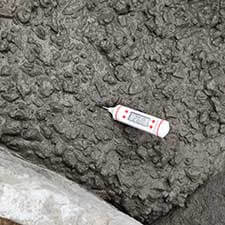
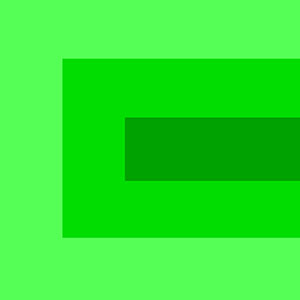