PQC stands for Pavement Quality Concrete made with larger size aggregates following IRC specifications and laid over a Dry Lean Concrete(DLC), concrete subbase course. PQC construction is explicitly used for highway concrete pavements and runway pavements to take heavy loads.ย
Also, Read: Concrete Subbase Course – DLC Construction
PQC Construction Method:
Plant and Machinery:
Excavator, Paver, Motor Grader, End dumpers, Vibro rollers(tyre mounted), Vibro rollers(smooth wheeled double drums), Concrete Batching Plant, Needle and screed vibrator etc. are required for PQC construction.
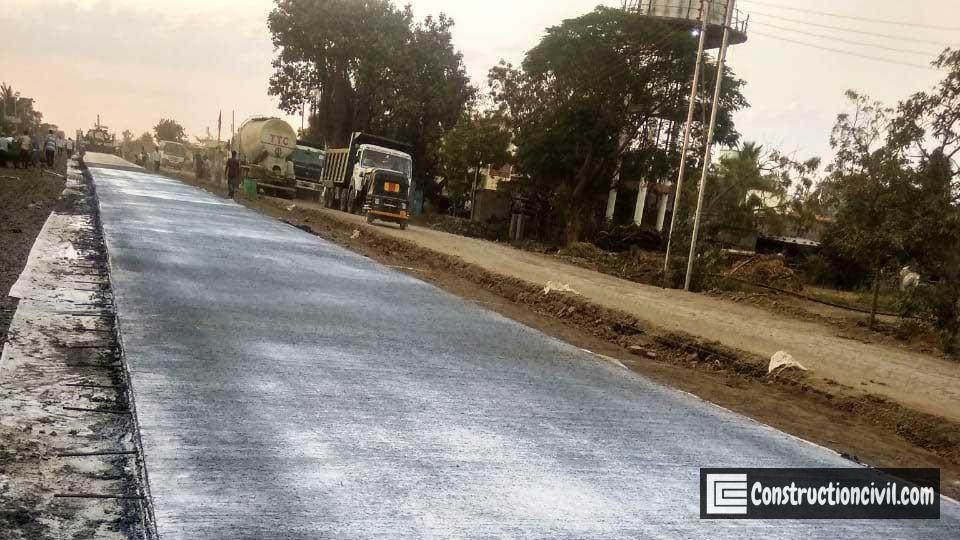
Also, Read: Properties of Concrete – Introduction to Good Concrete Practice
PQC Construction Materials:
The following list of materials is essential for PQC construction.
- 20mm size aggregate
- 10m size aggregate
- Crushed Stone dust and sand
- OPC 43 grade
- Admixture
- Water
- Dowel bar of 32mm dia from an approved source
- Tie bar of 12mm dia from an approved source
- Poly Sulphide sealant of approved brand
- Epoxy of approved brand
- Anchorage grouting compound of approved brand
- Curing compound of approved brand
- Separation membrane of specified thickness
PQC Construction Materials – Important Notes:
Cement:
- Up to 20% of fly ash can be blended for PQC construction as a partial replacement of ordinary portland cement of grade 53 only.
- GGBFS(Ground Granulated Blast Furnace Slag) conforming to IS:12089 shall not be used in any other grade of cement except 53 grade.
- As per MoRTH, the minimum OPC content for PQC construction shall be 310 kg/cum in case of blending at the site, and Mix design will be done as per IRC:44.
- In the case of the Portland Pozzolana Cement, fly ash content should be 25% or less for pavement concrete.
- The cement used having sulphate resistant property and shall conform to IS:12330.
Chemical Admixtures:
- Admixtures used for PQC construction work shall conform to IS:9103 and IS:6925.
- The admixture’s solitary function is to improve the workability of the concrete or extension of setting time without affecting concrete properties concerning strength, volume change, durability, and no harmful effect on steel bars.
Fibres:
- Steel(IRC SP:46) or polymeric synthetic fibres can be used to reduce the shrinkage cracking and post-cracking subjected to Designer approval.
- The properties of fibres shall be as per MoRTH Section 600, clause 602.2.3.1.
Also, Read: Causes, Prevention and Repair of Concrete Surface Defects
Aggregate:
- Aggregates used for PQC construction work shall conform to IS:383 and with a Los Angeles Abrasion value, not more than 35%.
- Permissible deleterious materials content should be as per MoRTH table 600-2.
- Chloride ion and the Sulphuric anhydride (SO3) content should not exceed 0.06% and 0.25% by weight, respectively.
- For pavement concrete, The maximum size of coarse aggregate shall not exceed 31.5mm.
- We shall not accept the water absorption of more than 2% in pavement concrete mix.
- The soundness of aggregate shall be tested as per IS:2386 (Part-5), and the loss shall not be more than 12% if sodium sulphate solution is used or 18% if magnesium sulphate solution is used.
- The combined Flakiness Elongation index of aggregate should be 35% or less for PQC construction.
Fine aggregates:
The fine aggregates for PQC construction work may be clean natural sand or crushed stone dust or a combination of the above conforming to IS:383. It should be free from soft particles, clay, shale, loam, cemented particles, mica and organic and other foreign matter. It is essential to investigate the mica content of fine aggregate before mix design and make suitable allowances for the possible reduction in concrete strength.
Water :
As per IS:456, it should be clean and free from harmful oil, salt, acid, vegetable matter or other substances.
Mild steel bars for dowels and tie bars :
- Dowel Bar having a yield stress of Fe-240 shall be of plain mild steel conforming to IS:432.
- Tiebar having yield stress of Fe-500 shall be of TMT steel and shall conform to IS:1786.
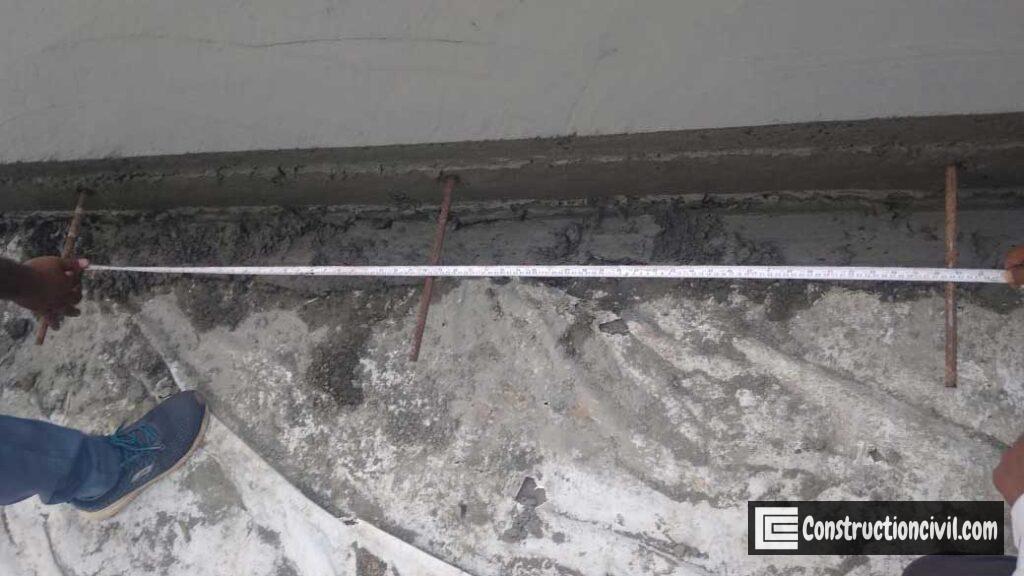
Also, Read: Concrete Ingredients – Important Properties and Tests
Pre moulded joint filler :
- As per IS:1838, or BS:2630, a firm compressible Joint filler board for expansion joints is used only at adjoining structures like bridges with a thickness of 20-25mmยฑ 1.5mm.
- It shall be 25mmยฑ 3mm down from the deck slab top level and provided in full width between the side formwork.
- It should be in suitable lengths which shall not be less than one lane width.
- To give a sliding fit of dowels recess to be provided on the compressible Joint filler board.
Joint sealing compound :
- As per IRC:57, the joint sealing compound for PQC construction shall have the following properties: flexibility, resistance to age hardening and durability.
- It would be of the hot poured type, elastomeric type or cold poured type (polysulphide/polyurethane/silicon)
- More than six months old Joint sealing compound is not suitable for construction work. The samples shall meet the specifications, as specified in IRC:57. Hot applied sealant shall be as per IS:1834.
Construction of PQC:
- We shall leave the PCC sub-base course which is known as DLC for seven days before overlaying OF PQC.
- Dowel bars of 32 mm dia, 500 mm long shall be placed as per clause 602.6.5 of MoRTH, and maintain the spacing of dowel bars, which is 220 mm centre to centre or as per approved pavement design.
- A tie bar of 12mm dia of length 640mm shall be placed at the centre to centre spacing of 550mm as per clause 602.6.6/Approved pavement design.
- Before placing PQC, side formwork shall be erected true to the line and level.
- Separation membrane (impermeable PVC sheet of 125 microns thick transparent or white) laid flat with minimum creases over DLC as per clause 602.5 of MoRTH before laying PQC.
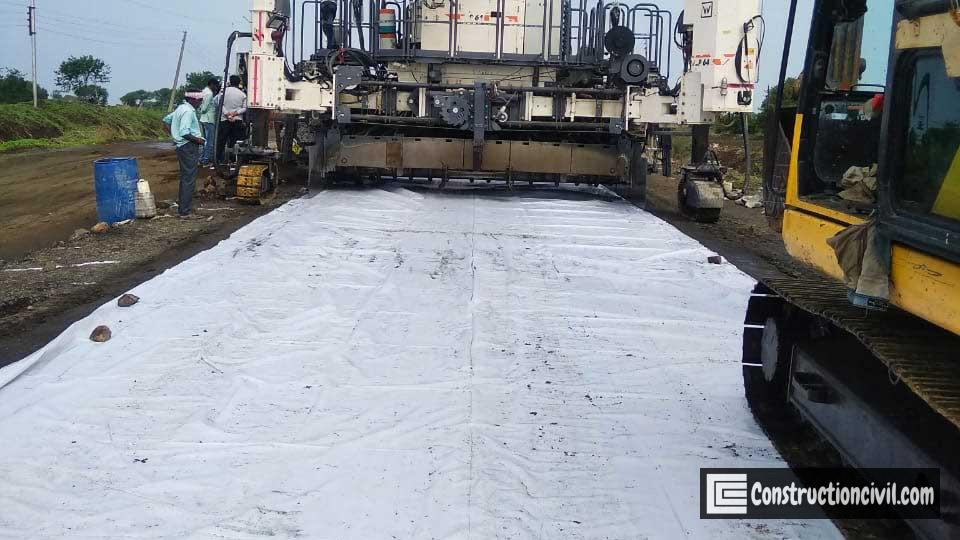
Also, Read: Design Mix of Concrete – Detailed Procedure With Calculation
- PQC mix shall be prepared in the fixed automated batching plant and hauled to the site. It shall be placed manually or with the help of an automatic paver.
- Compaction of the mix shall be done with needle vibrator and screed vibrator to have fully compacted thickness in case of manual laying.
- Quality control for each day laying of PQC shall be done as per clause 903.5.2.1 of MoRTH. Beams for flexural strength and cubes for compressive strength shall be moulded at the plant and tested at a specified time at the site lab.
- The compacted surface of PQC shall be textured as per clause 602.9.8 of MoRTH.
- Approved curing compound on the textured surface shall be sprayed as per clause 602.9.9 of MoRTH after three hours of PQC laying. It should be appropriately covered with moist hessian cloth and remain kept moist for 14 days.

Also, Read: Rusting of Iron Rebar in Concrete – Special Repairing
Contraction joints:
- Transverse contraction joints with dowel bars need to be provided at pre-specified locations mentioned in the construction drawing.
- After the initial hardening of PQC mix, joints cutting work started with the help of a joint sawing machine without damaging the newly constructed slab.
- Contraction joints should be 3 to 5 mm wide and 1/3rd-1/4th depth of the slab ยฑ 5 mm deep or specified in the drawings.
- The contraction joint shall be widened and accommodate the sealant as per Clause 602.11 or as per IRC:57.
Expansion joints:
- It is essential to provide expansion joints at predefined intervals of PQC slab to avoid any kinds of expansion cracks.
- All expansion joints shall consist of a joint filler board.
Longitudinal joint:
- As per the approved drawing, longitudinal joints shall be prepared after saw cutting as per details or as per dimensions given in IRC:57.
- The groove can be prepared with the help of a cutting machine after the final set of PQC.
- As per clause 602.6.6, tie bars shall be provided at every longitudinal joint, maintaining dimensions and spacing shown in the construction drawing.
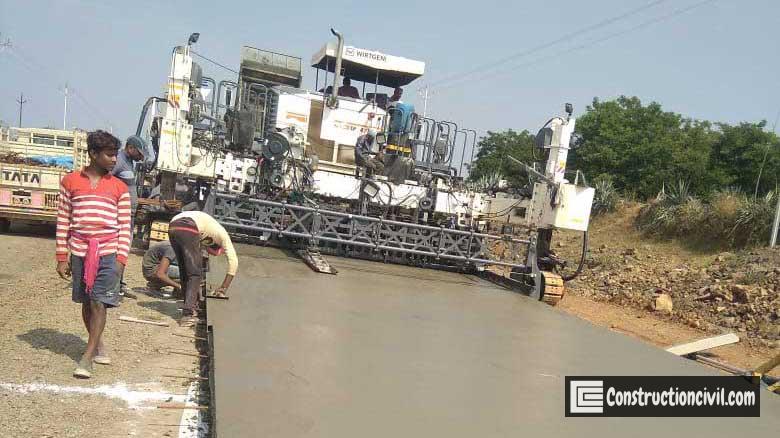
Also, Read: Blowholes/Surface voids/Bugholes in Concrete Surface
Concrete Mix Design Requirements:
- Target mean flexural strength of PQC mix shall not be less than (4.5 MPa + 1.65s), where “s” is called the standard deviation derived by conducting the test on a minimum of thirty beams.
- The maximum free water-cement ratio should be 0.45 if Ordinary Portland Cement(OPC) is used and 0.50 when Portland Pozzolana Cement or Portland Slag Cement or OPC mixed with fly ash or GGBFS is used.
- Depending upon the paving equipment available at the site, workability shall be established, constructing a trail patch. PQC mix slump value in the range of 30 ยฑ 15 mm is acceptable for PQC works, but this may be adjusted depending upon the site conditions and need approval.
Reference:
- MoRTH 5th revision
- IRC 58
- IRC 44
- IRC 15

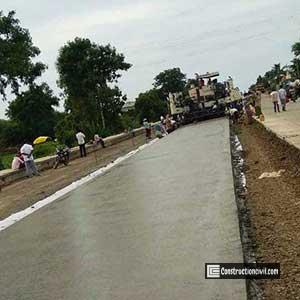
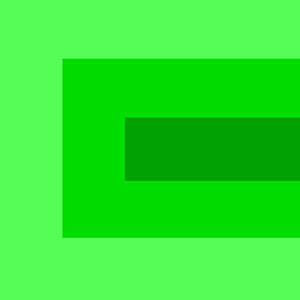