Cast-in-situ bored pile foundation may be used by proper choice of installation methods covering the method of soil stabilization that is the use of casing and drilling mud; method of concreting that is tremie and choice of boring tools that is hydraulic rig or DMC setups in order to permit a satisfactory installation of a foundation pile at a given project. Detailed knowledge about the subsoil conditions is vital to deciding the details of the pile installation technique. In this section, we learn more about the construction of a Pile foundation by the Direct Mud Circulation(DMC) method.
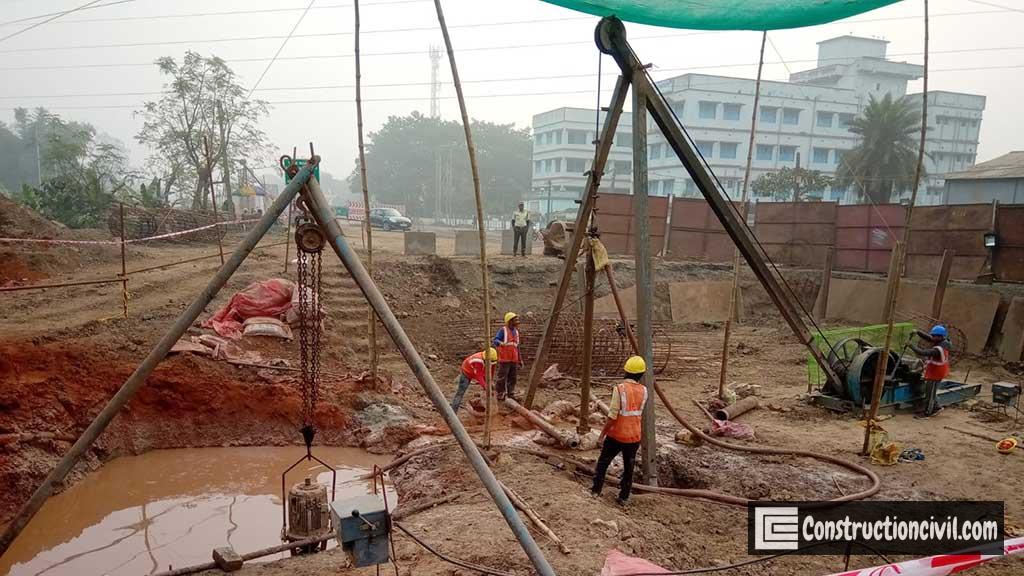
Also, Read: Types of Deep Foundation in Civil Engineering
DMC Pile Foundation Construction Method:
Pile Foundation Survey:
Coordinates of individual piles of a group shall be worked out for longitudinal and transverse centerlines. Pile centre points shall be marked at exact DMC pile locations as per the approved drawings with the help of a Total Station. After that, reference points shall be marked/fixed at a suitable distance from pile points to cross-check the pile’s centre during pile boring operations.
Guide Casing Placing for DMC Pile:
- The boring is of DMC pile(direct mud circulation) type carried out by using Bentonite drilling fluid, Mendola type pile rigs consisting of two freestanding front legs attached to a centre leg with a pulley at one end, and fixed to a mechanical winch at the other end.
- For example, when the average height of overburden from the pile cut-off level is about 2.50 m, excavate up to the pile cut-off level, known as the working platform level.
- First, the front legs of the rig are placed on both sides of the pile centre point, and then the legs are adjusted until the pile point is approximately in the centre of the legs by eye judgment.
- Then about 50mm sand cushion around the pile point more than the required foundation pile diameter is formed, and a bailer of outer diameter equal to the required pile/guide casing diameter hanging from the pulley is slowly dropped.
- The bailer leaves a circular impression on the sand cushion around the pile point, from which the exact centre of the bailer coinciding with the pile centre can be judged and, if not, can be adjusted by the leg movement. Once the process is completed, three more points are to be marked radially around the pile point at a distance of about 2.0m to verify the true centre of the guide casing at the time of boring.
- Initial boring is done by dropping the bailer about 1.0m-2.0m falls into the borehole. After initial boring, a guide casing of the inner diameter equal to the pile diameter is inserted into the borehole by tamping on the top of the casing with the bailer. Guide casing is rigidly fixed in the borehole up to 4m depth below the ground level to resist the loose soil of the surface falling into the borehole.
- While driving the casing, measurements w.r.t reference points shall be continuously taken, and the casing alignment will be corrected if necessary by hammering the casing laterally.
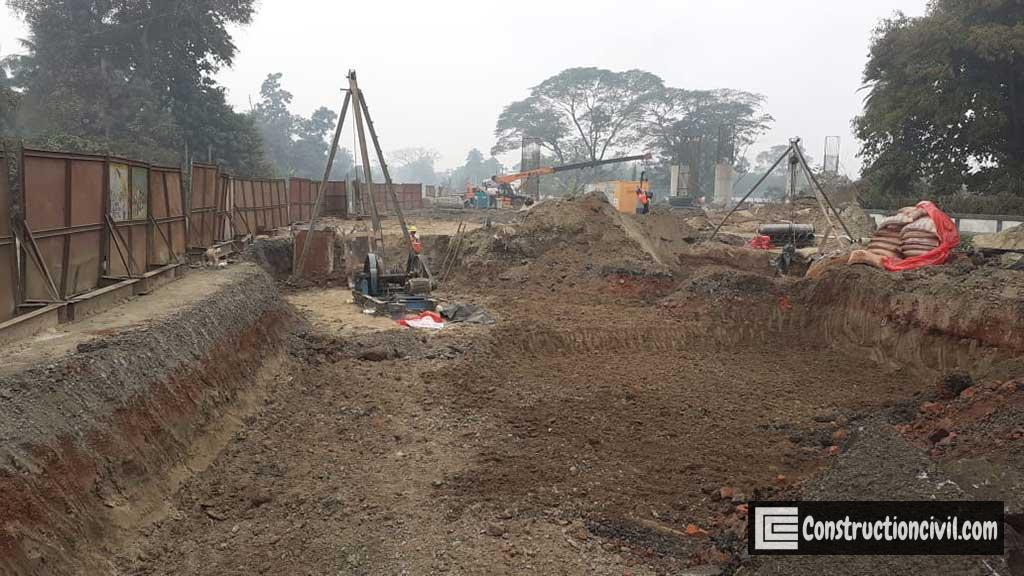
Also, Read: Integrity Test of Pile – Purposes, Procedure & Limitations
DMC Pile Boring Method:
- Excavate the soil from the inner of the already placed casing up to 2 to 3 m depth below the casing bottom.
- Cut a square hole of 150 mm width in the casing from the working platform top level to allow bentonite overflow to get out from the pile borehole.
- After guide casing driving, the bailer is taken out from the borehole, and boring is continued by percussion hammering with the help of a chisel by pumping Bentonite slurry having a specific gravity of 1.03 to 1.08 through the DMC rods connected.
- Simultaneously, the bentonite slurry that dislodged from the borehole flows out from the casing hole into the settling tank through the trenches made before operation.
- This process is continued until the boring is completed.
- Then the DMC pipes and chisel are removed. After completion of boring, bore depth should be measured by the sounding chain.
Pile Reinforcement Cage Lowering:
- A prefabricated and approved reinforcement cage is cleaned out of loose material and maintains the proper cover providing cover blocks throughout the length of the cage.
- The cage may be made in two more parts considering proper lap length as per the specification.
- Cage lowering is done from pile bottom to top (one after another) by main vertical reinforcement lap welding.
- The reinforcement cage should be welded in between the main vertical rod and stiffeners to maintain rigidity.
- Spiral rings shall be tightened properly with binding wire to the main bars of the pile after lap welding to ensure rigidity/stability during cage lowering.
- Required numbers of cover blocks shall be provided for the lap length portion. Lapping and staggering length should be maintained as per drawing/specifications.
- Maintain cage top level carefully at design level only.
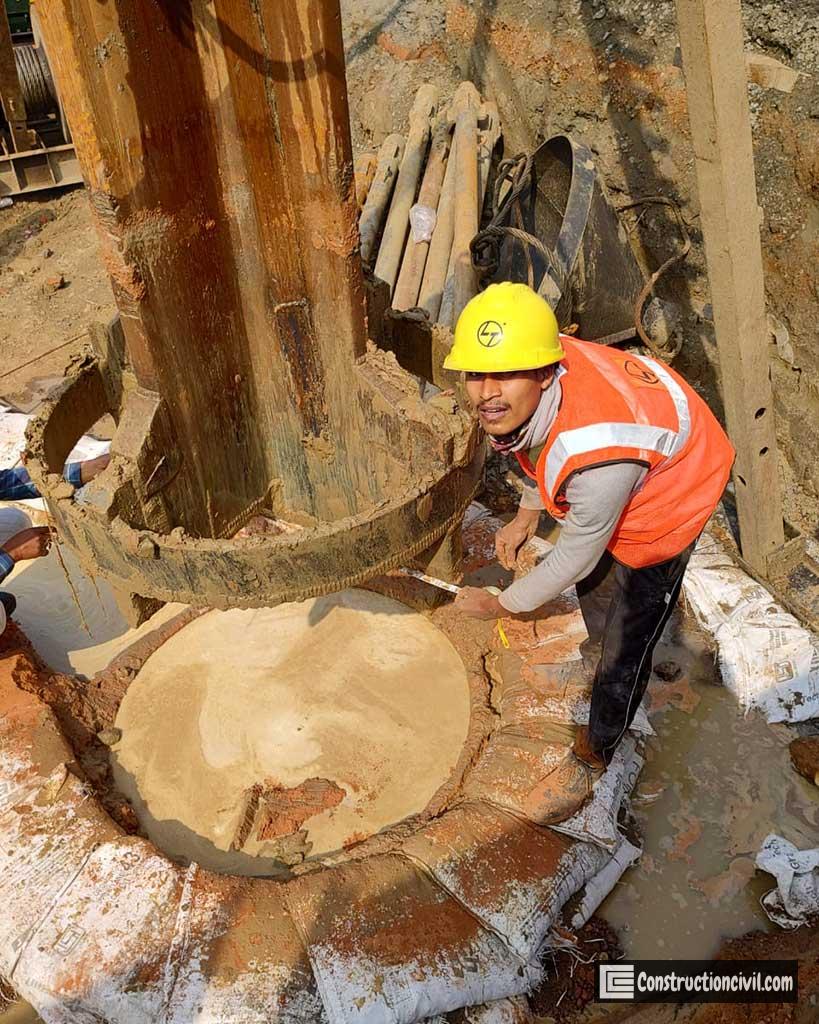
Also, Read: Construction of Footings – Important Guidelines
Tremie Pipe Lowering for Pile Foundation:
After completion of cage lowering, Tremie pipe of about 260.00mm diameter is to be provided throughout the pile shaft. Tremie pipe to be fixed one after another by threaded and socket joint. Tremie pipe length to be provided up to the required depth of pile with minimum clearance at the bottom to flow the concrete through the tremie pipe smoothly.
Flushing of DMC Pile Borehole:
- As piles are in sandy/silty strata (friction piles), it is always necessary to carry out flushing of piles at the end of completion of the pile borehole with fresh bentonite through the DMC rod connected.
- For flushing, bentonite slurry will be directly pumped from the swelling tank, where the slurry is ready for use after swelling.
- Air flushing will attract side collapses, hence not to be used for flushing and even flushing with immature fresh bentonite slurry.
- After cage lowering, tremie pipe lowering will be completed.
- Flushing will be done through already placed tremie before concreting.
- The bentonite coming out from the borehole will join the regular “vertical pump tank”. Frequently checking the specific gravity of bentonite slurry being fed v/s coming out of the borehole is necessary. When both the specific gravities match, the flushing is declared over.
- Return bentonite slurry, which is contaminated and contains much silt stored in a vertical pump tank, can be reused by recycling with the help of a vertical pump and desander unit.
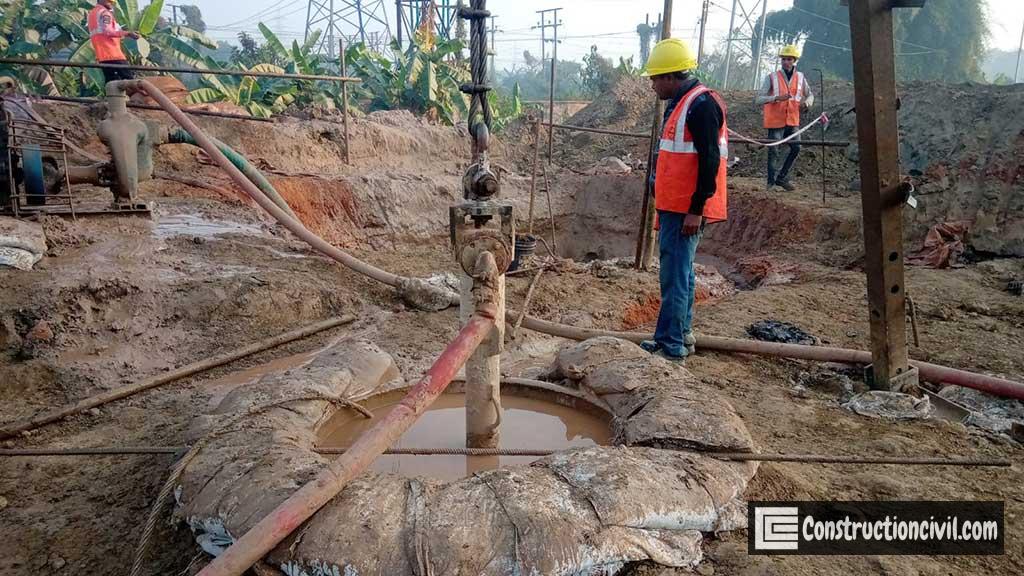
Also, Read: Bentonite Uses in Piling – Bentonite Slurry Preparation and Recycling
DMC Pile Foundation Concreting Method:
- After flushing through the tremie, a funnel known as a hopper shall be attached to the tremie, and the hopper should always be hanging and supported with the fork by taking support of rods/guide casing as disturbed pile bore base will harm the quality of the pile so constructed.
- After flushing through the tremie, remove the bentonite flushing arrangement from the tremie.
- Place a concrete funnel known as a hopper and snap-out plug (MS circular plate) in the funnel opening with one end of the wire rope connected with a plate and another with the funnel top edge.
- The quantity of the first charge of concrete shall be such that the weight of the column of green concrete formed is more than the hydrostatic head of bentonite standing inside the borehole.
- In the case of the first charge, the capacity of the funnel should be calculated accordingly; in this case, it shall be at least 1.0 cum.
- After placing the first charge, continue concreting and withdrawal of tremie pieces in between so that at no point of time the tremie embedment is less than 1.2 m inside concrete to avoid mixing fresh concrete with bentonite slurry.
- Concrete will be mixed either in mini batching or regular central batching plants. The concrete will be transported through transit mixers if it is from a regular central batching plant.
- Concrete will be poured into the hopper directly from the mini batching plant or the transit mixer, and concreting must be completed in a single continuous operation. Concreting of the pile should be uninterrupted. In the unusual case of interruption of concreting, but which can be resumed within one or two hours, the tremie shall not be taken out of the concrete. Concreting should be resumed by adding a little richer concrete with a slump of about 150mm-200 mm for the smooth displacement of the partly set concrete.
- To ensure compaction by the hydraulic static head, the rate of placing concrete in the pile shaft shall not be less than six meters (length of the pile) per Hour.
- The concrete slump shall be checked for each batch and recorded in the Concrete Pour card. In the case of batching plant, the concrete slump shall be checked at Batching Plant and at the pouring location.
- Tremie shall be raised and lowered gradually, from time to time to prevent the concrete throughout the tremie from setting.
- The theoretical and actual Concrete built-up depth shall be checked with sounding chains between the pile concreting operation and recorded in a prescribed format.
- Concrete in a pile is to be filled approximately 0.6 m (as per site conditions) above the cut-off level to permit removal of all laitance and weak concrete before capping and to ensure good concrete at the cut-off level for proper embedment into the pile cap.
- Concrete pile up to cut-off level, allow concrete to overflow equivalent to overflow height as per specification. In this case, the working platform shall be at the cut-off level. The overflow concrete will flow through the guide casing square hole.
- Pile concreting data shall be entered in the relevant formats for future reference.
- On completion of the Piling, all tremie pieces, funnel and fork be cleaned and stored correctly.
Also, Read: Construction of pile foundation by Rotary Method

Also, Read: Vertical Pile Load Test Procedure – Kentledge Method
Guide Casing Withdrawal after Piling:
After completion of the concreting operation, the guide casing, installed initially before pile driving, shall be extracted using DMC piling arrangement or with the help of a service crane.
After Piling Shifting Rig, Next location:
As soon as the pile guide casing is withdrawn rig will be shifted to the next pile location as per the predecided sequence by towing the assembly with the help of crowbars and by taking reaction from the piling winch. If the rig is shifted to the next foundation/bridge location, the rig will be dissembled and shifted & reerected/recommissioned.
Also, Read: Construction of Well Foundation – Step by Step Procedure

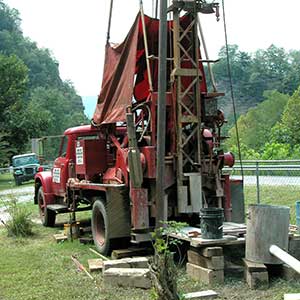
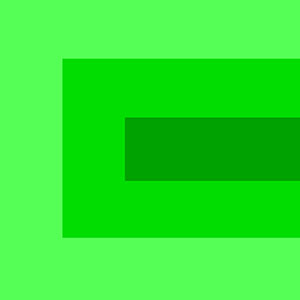
HI.. you are really giving good infoโs.. which everybody can understand easily and that too without doing 4 years civil enggโฆ
keep it up ADMIN
All the best..
Thank you
It is really east to understand. I’m also taking training in pile foundation as trainee.
GOOD EVENING SIR,
MY SELF MAHESH WORKANG AS A CIVILENGINEERING ,I NEED WORK STATEMENT IN PDF FOLLOWING CIVIL WORKS,
*TRIPOD PILING
*POURING OF CONCRETE
*EXACAVATION OF PILE CAP
*BACK FILLING OF PILING CAP
*SHUTTERING FOR PILE CAP
*BAR BENDING FOR PILE CAP
*PLINTH BEAM CONCRETE POURING
*SHUTTERING FOR PLINTH BEAM
*BAR BENDING FOR PLINTH BEAM
*BACK FILLING UP TO PLINTH BEAM TOP
This is a very informative article. Cast in situ piles provide more strength comparatively.