Piles are usually transferred axial loads from a structure to subsurface soil strata having sufficient bearing capacity. The load transfer mechanism from the structure to surrounding soil strata through the pile is complicated. However, the application of pile foundations has been used for many decades. Mainly, piles are designed considering friction along its shaft and/or the end bearing capacity of foundation soil. Selection of pile foundations requires the subsoil conditions, the load characteristics of a structure, settlement criteria and any other specific requirement of a particular project. Construction of pile foundation demands careful control of position, alignment and depth and requires specialized skill and experience. In this section, we learn more about the construction of pile foundation by Rotary Method.
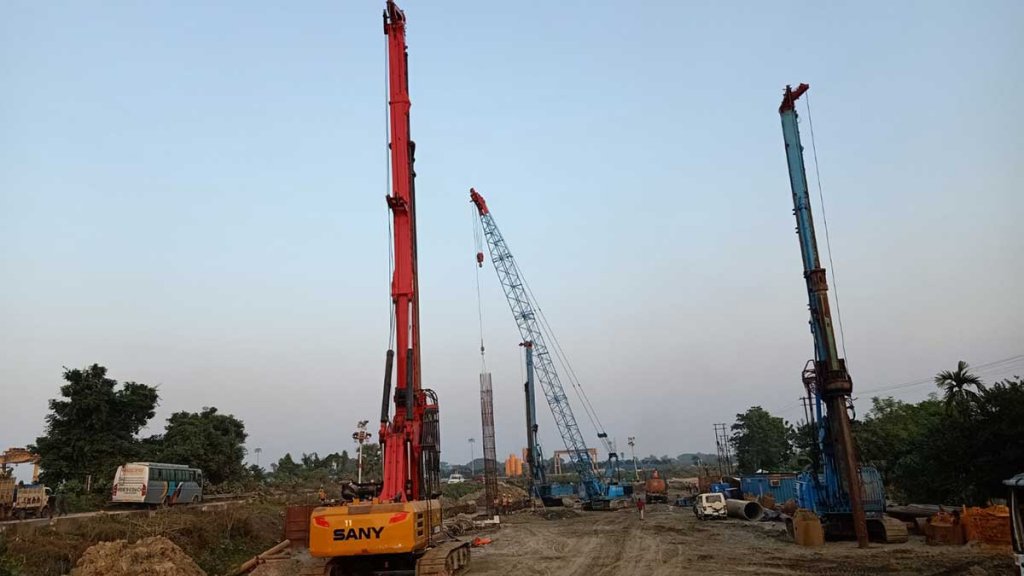
Also, Read: Bentonite Uses in Piling – Bentonite Slurry Preparation and Recycling
Construction of Pile Foundation by Hydraulic Rig Procedure:
Pile Point Survey Before Start of Piling :
- Coordinates for individual piles shall be worked out for longitudinal and transverse centerlines. Pile points shall be marked at exact pile locations as per the relevant structural drawings with the Total Station, and reference grid pillars shall be established. Reference points shall be marked/fixed at a suitable distance from pile points to cross-check the pile’s centre during the drilling operation.
- The setting out of pile positions shall be carried out by a qualified surveyor for every pile location as per construction of pile foundation methodology.
- The piling Engineer shall be informed of the setting out and requested to check the pile locations before any piling work is carried out.
- The setting out pegs will consist of steel reinforcing bars, or the nails, as required, shall be driven slightly below the working platform level of the piling rig so that they will not be disturbed by the pile boring activities.
Guide Casing Driving Before Start of Pile Boring:
After completion of the pile point survey, the piling rig moves to the position of the pile to be installed, and the pile point shall be made visible by hand excavation. Two reference pegs are set perpendicular to each other at one meter from the outside of the temporary casing.
- The temporary steel casing of outer diameter is equivalent to the nominal pile diameter and a minimum of 6-millimetre thickness with the necessary guide collar.
- Temporary steel casing shall be provided 4.0m below Ground Level or as specified in the approved drawing, depending on the soil and other conditions.
- The casing is punched and centralized over the centre point of the pile using a vibro-hammer. The verticality shall be controlled by a long base level alternatively positioned in two mutually perpendicular directions on the casing or with two plumb lines on the perpendicular axis.
- The casing will extend about 250 to 300 mm above the working platform and serves as a guide for the auger.
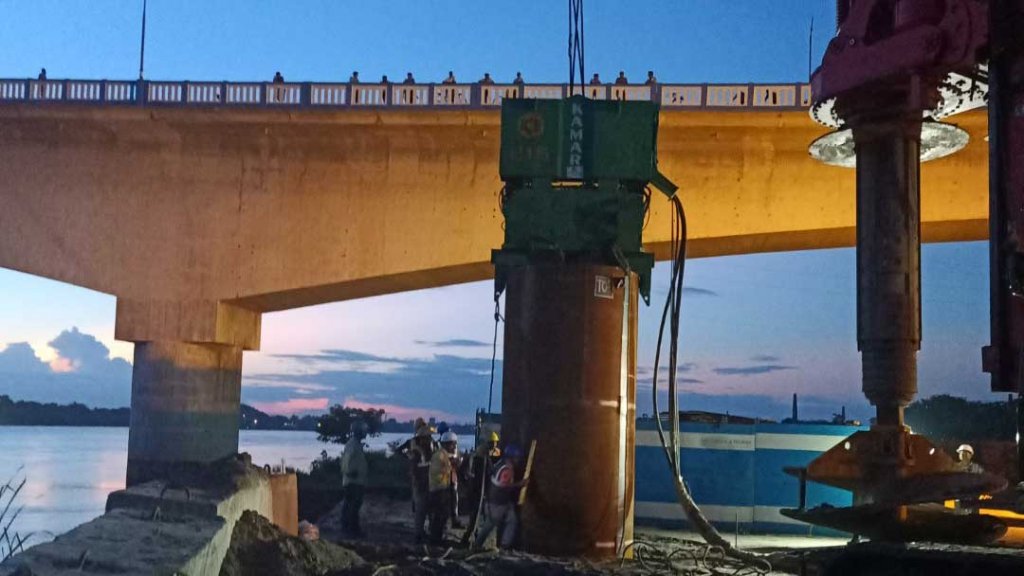
Also, Read: 4 Important Bentonite Test for Piling – Equipment & Procedure
Pile Boring Operation:
- Once the temporary casing has been installed, excavation for the foundation pile shall be carried out using Hydraulic rigs. The Boring bucket with the cutting tool will have an external diameter equal to the diameter of the pile, less 25-30mm or specified by the bucket manufacturer. For example, for a pile diameter of 1200 mm, the tool diameter shall be 1125 mm.
- During boring operation, pile borehole is filled with Bentonite slurry, fed from Bentonite storage tank. A proper bentonite pipeline shall be installed between the storage tank and the pile bore for the continuous supply of fresh bentonite to the borehole.
- Bentonite powder shall be mixed with fresh water at least 24 hours before, and it will ensure that bentonite is completely dispersed in the water and attain the required density to stabilize the sides of the borehole during drilling.
- It will be crucial to maintain the quality of bentonite shall be carefully controlled at stages of mixing, supply to the borehole and immediately before concrete is placed. The following limits shall be remembered during the construction of pile to maintain the borehole stability.
- The density of Bentonite suspension from 1.05 gm/cc to 1.10 gm/cc
- The marsh cone viscosity for the construction of pile is between 30 to 40sec
- The pH value is between 9.5 to 12
- The silt content for the construction of pile is less than 1% for fresh bentonite slurry
- The liquid limit for the construction of pile is not less than 400%
- Bentonite slurry is pumped by a high-pressure 15 to 20 HP reciprocating pump/vertical pump into the borehole through the pipeline. Bentonite slurry level under the borehole to be maintained throughout the boring operation.
- Each time the drilling tool is filled with boring muck, it is taken out and unloaded on the ground at a specified location. Then the tool is again lowered into the borehole, and boring is continued.
- The telescopic arrangement of the piling rig lowers the bucket further deep. Though the verticality of the pile being bored mainly depends upon the operator’s skill. Verticality shall be checked periodically by checking the verticality of the rig mast.
- The verticality of the pile can also be ensured by incorporating the changes in the design of Kelly, like increasing the overlap of the Kelly assembly pieces, hence reducing the play in joints, thereby reducing the possibility of deviation in verticality.
- Some advanced tests like Ultrasonic Echo Sounding Test may ensure the verticality of the pile borehole. Specialized equipment such as ‘High Precision Bore-hole Inclinometer’ or ‘Sonicaliper’, a device which gives 3D images of bore area profile, may also be used in the construction of pile foundation to control and ensure the verticality of the pile borehole but shall be an expensive option.
- On reaching the foundation level, the depth of the borehole shall be measured by taking sounding, and the exact depth shall be measured and recorded. Measurements for pile length shall be certified by the Engineer and secured clearance for cage lowering and concreting.

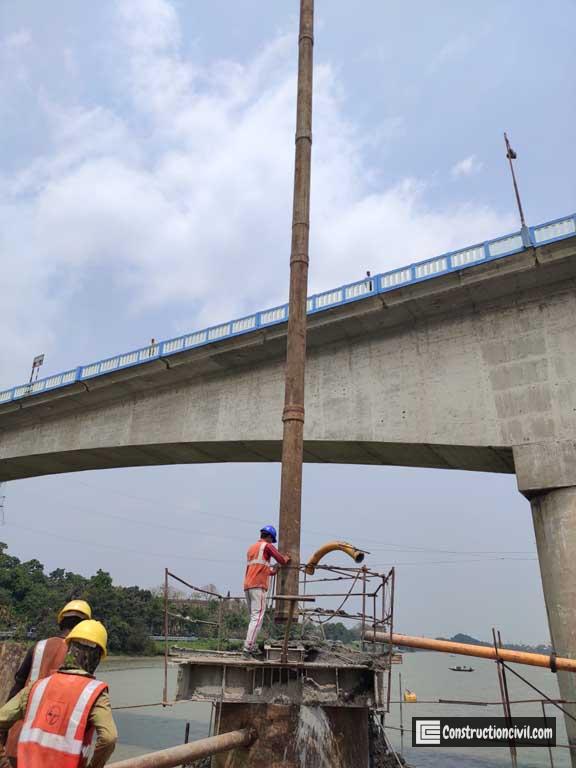
Also, Read: Tolerances for Foundation Piles – Important Guidelines
Flushing of the Pile Borehole:
- On approval of the funding level, the bore is flushed by freshly mixed bentonite slurry with direct mud circulation. The pumping for the flushing operation is done by use of a mud circulation pump.
- The boring bucket is removed during flushing to remove all the loose mud/soil that might have accumulated on the founding level. Further, the flushing operation shall be continued until the consistency of inflowing and out-flowing slurry is similar.
- After flushing is over, the piling rig shall be removed, and the borehole is ready for lowering of the reinforcement cage.
- In the event of pile boring being completed and the time lag between completion of boring and the start of concrete is more than 12 hours, the bore shall be re-cleaned by Air flushing before the start of pile concreting.
Pile Reinforcement Cage Lowering:
- Pre-fabricated, pre-certified and pre-recorded reinforcement cage shall be lowered into the borehole by the rig/service crane in one piece.
- If two or more cages are lapped with the lap length as per relevant drawings and specifications, spirals shall be placed around the lapped length and tack-welded to the main bars.
- Also, cover blocks of required numbers shall be provided for the lap length portion. Lapping /Staggering etc., as per drawing/specifications, shall be provided.
- Spiral rings shall be tightened with binding wire to the main bars of the pile to ensure rigidity/stability during cage lowering.
- Whenever the reinforcement cage top is below the operating floor level of piling equipment, provide temporary suspenders in the form of 4 Nos of 16 mm dia rods or as required at the top of the reinforcement cage by welding.
- Maintain cage top at design level only. Measurements shall be as per the approved bar bending schedule and certified by the Engineer.
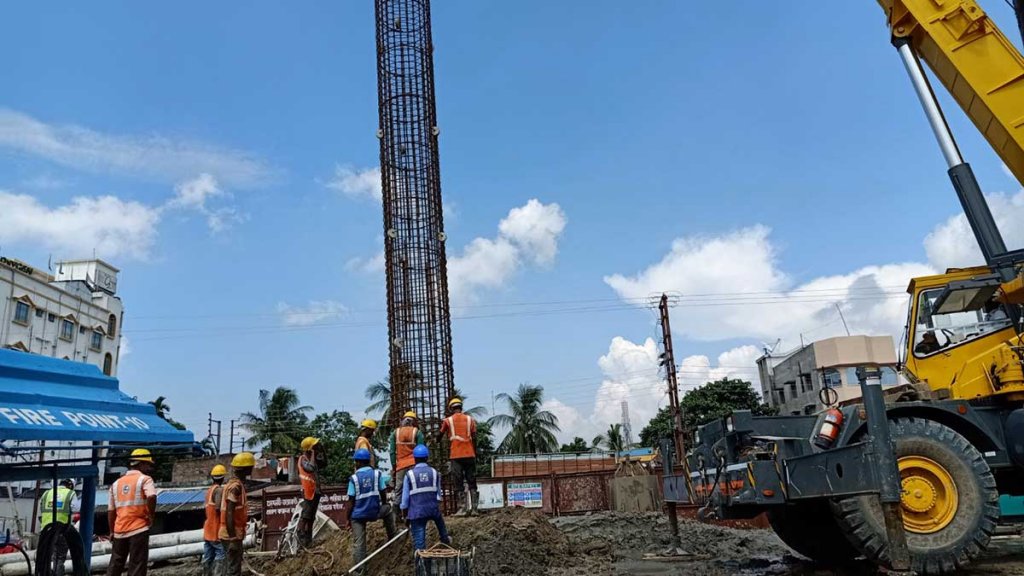
Also, Read: Construction of Footings – Important Guidelines
Tremie Pipe Lowering:
- Before lowering, all the tremie pipes shall be thoroughly checked, and form oil shall be applied inside the pipes for the free flow of concrete inside the tremie.
- Pre-calculated, pre-assembled and pre-recorded in sequential order, tremie shall be lowered through reinforcement cage with the help of rig/service crane, keeping 300 mm clearance from bottom of pile borehole.
- If required, adjustable tremie pieces shall have to be replaced in place of standard length pipe pieces.
- The tremie pipes shall be clean, watertight, and of adequate diameter (usually 200mm-300mm diameter) to allow the free flow of concrete during construction of pile.
- The length of the tremie pipe (total of individual joined pipes) shall be more than the length of the pile, and the base of the tremie pipe shall be lowered to the bottom of the borehole allowing drilling mud to rise inside it before pouring of concrete.
- Before the start of concreting operation, the borehole shall be flushed with fresh Bentonite slurry to wash the borehole and flush out all loose particles and deleterious materials, if any, present in the bore.
- The top of the tremie pipe shall be fitted with a large diameter Funnel to receive the concrete with a steel sealing plate arrangement at the bottom of the funnel. The funnel should always be hanging and supported by a fork only.
- After the funnel is filled with concrete, the steel plate is removed, and concrete is discharged. After that, concrete is done in a continuous manner, up to the required level.
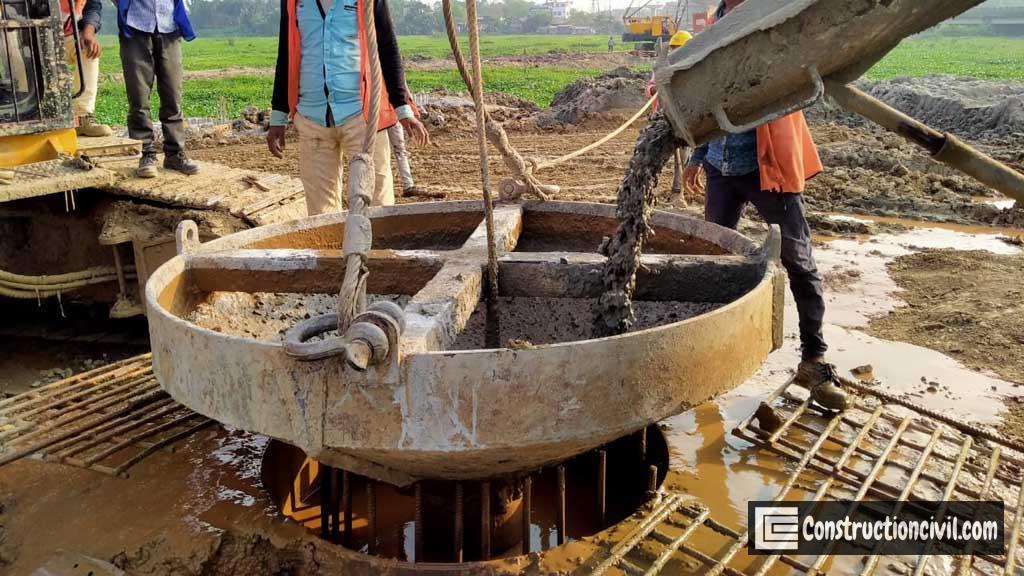
Also, Read: Types of Deep Foundation in Civil Engineering
Pile Concreting:
Concreting operation is similar to pile foundation construction by the “Direct Mud Circulation(DMC) method.“
Guide Casing Extraction after Construction of Pile Foundation:
After construction of pile, the guide casing, installed initially before pile driving, shall be extracted using the Vibro hammer and service crane.
Tolerances for Construction of Pile Foundation:
Permissible tolerances for Bored Piles shall be as follows (Ref Cl.1116.1 (iii) of MORT &H).
a) Variation in cross-sectional dimensions of pile: +50 mm, – 10mm
b) Variation from verticality: 1 in 50
c) Variation in the final position of the pile head in plan: 50 mm
d) Variation of the top level of piles: +/-25 mm
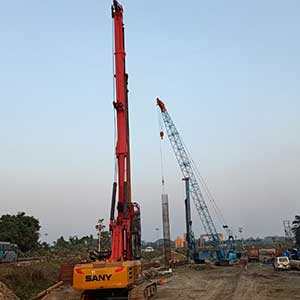
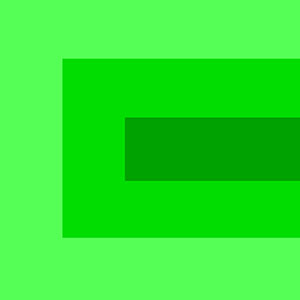