What is a Culvert?
The culvert is a small cross drainage structure spanning six meters or less between the inner face of the wall. It may be like a bridge designed to allow carrier or pedestrian traffic to cross the stream providing adequate clearance from high flood levels. Depending upon the project’s requirements like traffic volume, embankment height and high flood level, it may be a single cell or multicell box culvert with round, elliptical, flat-bottomed shapes, open-bottomed, pear-shaped, and box-like structure.
Culvert types:
Following are the different types of culverts:
- RCC Box type culvert
- Hume pipe culvert
- RCC slab type culvert
- Stone slab type culvert
- RCC arch culvert
- Masonry arch culvert
In this section, we learn more about the construction methodology of the RCC box culvert, which has a significant role in providing cross drainage.
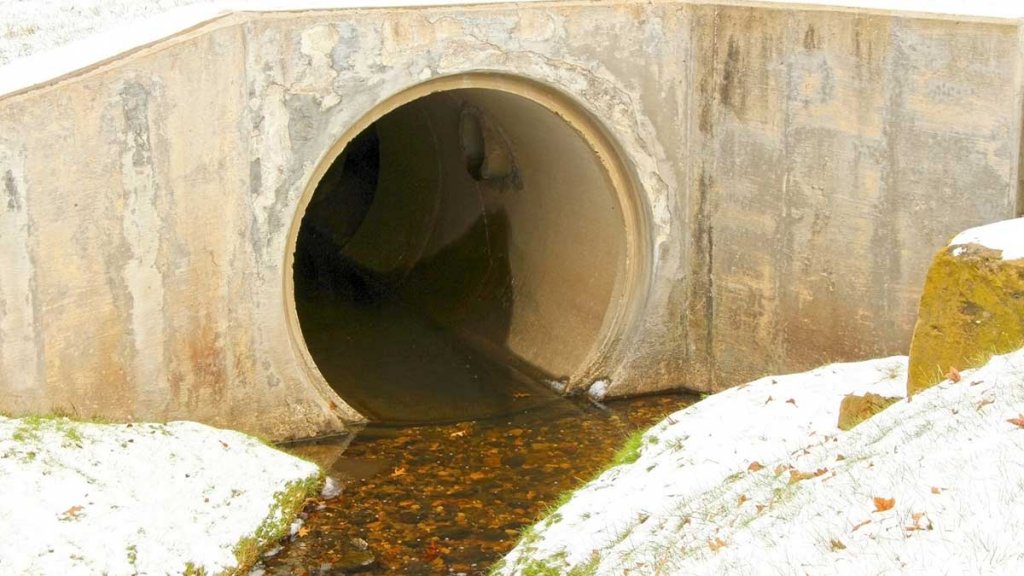
Also, Read: Construction of Footings – Important Guidelines
Complete Method Statement for Box Culvert Construction:
The construction sequence of the box culvert mainly consists of the following activities-
- Raft Construction (Foundation)
- Wall Construction (Substructure)
- Deck Construction (Superstructure)

Construction of Box culvert Raft: (STAGE -1):
Survey & Setting Out:
- Survey points shall be marked in either direction of the alignment by the total station from control points.
- A benchmark shall also be established nearby where no disturbance will occur throughout the execution phase.
- The benchmark shall be checked at the frequent interval as and when required.
- The foundation shall be marked on the ground with the clearance of formwork space required.
All the Survey Instruments used shall be calibrated periodically per the Calibration Plan. Survey check reports/other relevant data shall be maintained in relevant inspection formats.
Dewatering:
- The open foundations are provided mainly for the cross drainage structures, which require preplanning for dewatering before excavation commences per site conditions.
- If required, water shall be diverted through other channels; otherwise, dewatering shall be done if required. Depending upon the flow of water, a pump of about 5 to 10 HP capacity may be sufficient to keep the foundation dewatered.
- Pumped-out water shall be released at the farthest point to the maximum possible. The surface water source shall be checked and, if possible, stopped from joining this stream or diverted to another stream.
Earthwork and Excavation for Box Culvert Raft:
- The excavation shall be done with safe side slopes per ground conditions, and sufficient margin for the minimum working area should be left (minimum 300mm).
- JCB or excavator shall carry out excavation, and excavated material shall be disposed of using tractor trolleys or dumpers as directed.
- The pit level reached up to the PCC bottom shall be properly levelled and compacted before laying Plain Cement Concrete.
- The SBC at the founding level shall be checked for the design SBC as given in the construction drawing with the help of the Plate Load Test for the individual culvert.
- If the actual SBC is less than the design SBC, then granular filling up to thickness as specified in the drawing shall be done in layers and compacted to 95% of modified proctor density.
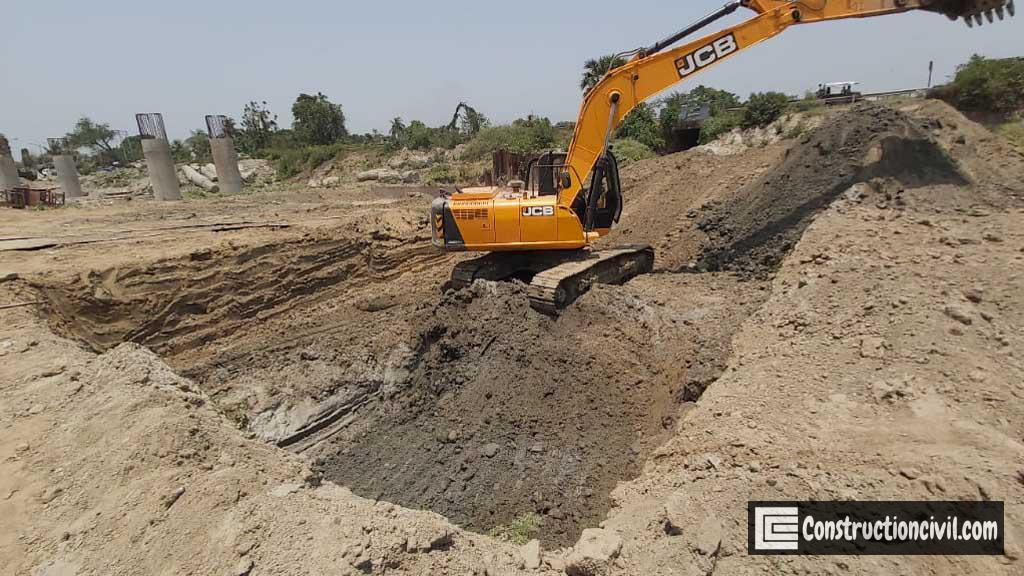
Also, Read: Top 7 Ground Improvement Techniques in Civil Engineering
Levelling Course (PCC) for Cross Drainage Structure:
- The excavated pit shall be manually dressed with sufficient working space around the raft to be constructed.
- Fix forms like ISMC 150 or wooden planks at the edge as formwork.
- PCC shall be supplied from the batching plant through transit mixers.
- It shall be unloaded through chute/s, then manually spread and compacted in a uniform layer of levelling course thickness.
- After the initial setting, the concrete surface shall be sprinkled with water to prevent cracking. Curing shall be done by keeping it moist with Hessian cloth or by continuous water spray.
- After allowing it to gain strength over 24 hours, it can be released for raft activities.
Reinforcement Binding for Box Culvert Raft:
- As per the approved construction drawings and bar bending schedule, reinforcement of the raft is pre-straightened /cut/bent in the rebar yard.
- Reinforcement bars shall be shifted to the location in advance.
- Marking for the raft shall be done on the levelling course.
- Rebar shall be tied as per approved drawings and bar bending schedule. Chairs shall be provided at appropriate places to avoid the sagging of the top reinforcement mesh.
- After completion of top reinforcement, erect the vertical wall bars with binders/spacers.
- Necessary pipe support with an inclined member shall be provided to the vertical bars temporarily from sides to avoid tilting of rods.
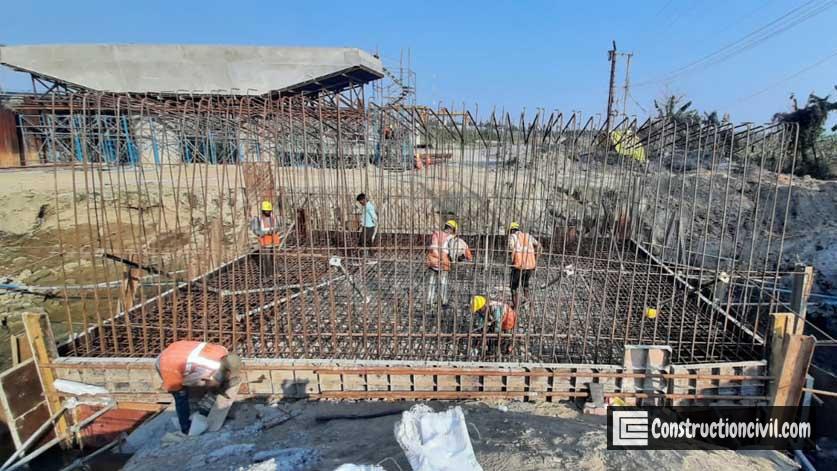
Also, Read: Ground Improvement Techniques – Vertical Drain & Stone Column
Formwork Fixing for Box Culvert Raft:
- Concrete cover blocks of the same grade of foundation concrete shall be tied to the reinforcement before fixing formwork.
- Steel formwork plates applied with shuttering oil are fixed in position with the help of props and ties/spacers against each other to line and level as per formwork and staging drawing.
- The formwork shall be properly jointed with bolts and a washer. Foams or masking tape shall be used in joints to keep the formwork joints leak-proof. During concreting, the formwork shall not lose its alignment.
- Foundation dimensions and reinforcement details should be as per the good for construction drawing. Final inspection shall be carried out before pouring concrete as per guidelines, and if deviations are found shall be corrected before pouring concrete.
Box Culvert Raft Concreting:
- Concrete shall be supplied from batching plant through transit mixers.
- Concrete shall be poured into the foundation using a direct chute or concrete pump as per the accessibility. Chutes shall be made using MS sheets/CGI sheets supported by structural steel members. Chutes shall be placed with an appropriate slope so that concrete free flows. In the case of concrete using a chute, the same shall be made wet before pouring concrete over it for concrete to free flow.
- Concrete shall be laid in 300-450mm thick layers and vibrated with diesel or electrically operated 60mm/40mm needle vibrators. The layer thickness shall be selected such that the next layer is laid before the previous layer initially sets.
- The exposed top surface of the concrete shall be a smooth finish using a mason’s trowel.
- The wall portion shall be made with Shear keys (Construction Joint), as shown in the drawing.
- Cut piece Reinforcement rods of diameter higher than 25mm shall be embedded (depth of embedment not less than 50mm) along the centre line of the base raft to support inclined props to be used for 2nd stage formwork of wall before final setting of concrete.
- After the initial set, protect the concrete surface with a moist hessian cloth. After the final setting, mortar bunds shall be made for ponding water, and the sand layer is laid in bunds to retain water for proper curing.
- Within 24 hours, concrete will gain sufficient strength, and de-shuttering shall be done carefully.

Also, Read: Soil Reinforcement Methods – Advantages and limitations
Box Culvert Raft Formwork Removal:
- The concrete shall be allowed to gain strength over 12 to 24 hours, and then forms shall be removed without damage to the concrete.
- The forms, side supports and shoring, shall be safely removed, cleaned and stacked correctly for future use.
- The exposed concrete side surfaces shall be inspected for blemishes. Blemishes, if any, shall be mended immediately.
- The pit shall be immediately backfilled with excavated material up to the raft’s top level. This filling will help in curing the foundation if kept moist. The top of the raft shall be provided with cement sand mortar bund and kept inundated with water for curing till the curing period is over.
Box Culvert Wall Construction ( STAGE -2):
The construction joint between wall and deck shall be provided as per the following guidelines:
- For Box Culvert without Cushion: Construction Joint shall be 300mm below the end of corbel level.
- For Box Culvert with Cushion: Construction Joint shall be 300mm below the deck slab bottom level.
- Maximum wall lift height in a single pour shall be as per the availability of formwork material. If the wall lift height exceeds the above height, the intermediate lift shall be planned accordingly.
Box Culvert Wall Reinforcement:
- Balance reinforcement shall be tied against the dowels left through the raft for the predetermined lift to be concreted.
- Vertical rods shall be provided with required overlaps as per construction drawings.
- Efforts shall be made to minimize overlaps, and horizontal reinforcement shall be tied in position.
- Concrete cover shall be provided by Concrete cover blocks tied with reinforcement as required.
Box Culvert Wall Formwork:
- After completion of reinforcement work, forms in panels shall be erected, aligned and fixed in position as required against the already tied reinforcement.
- The forms shall be placed over the seating channel fixed by tie bolts through left-out holes in an already concreted straight portion over the box culvert bottom haunch.
- The forms shall be side supported with the help of struts taking reaction from the channel placed against the embedded reinforcement in the already concreted raft.
- There shall be retrievable tie rods passing through HDPE conduit pipes holding forms from both faces of walls.
- The line and level shall be achieved as per approved drawings and then cleared the wall for concreting.
- The schematic wall formwork arrangement shown above is only to support the methodology, whereas the actual execution shall be done as per the final formwork/staging drawing issued by the engineering department.
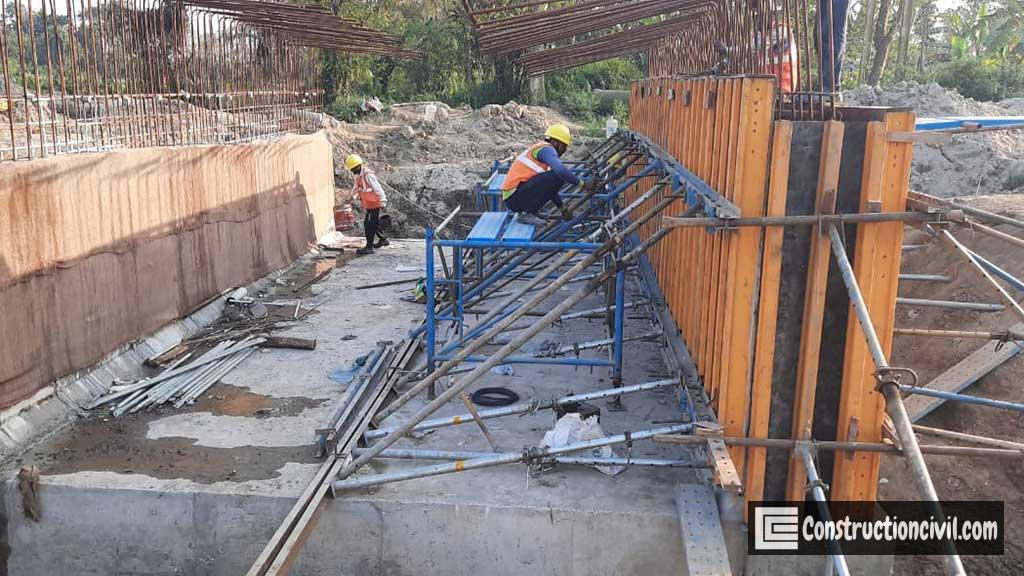
Also, Read: Plate Load Test for Soil – Procedure and Limitation
Box Culvert Wall Concreting:
- The concrete mixed from the centralized batching plant/s shall be delivered through transit mixers.
- It shall be placed manually or through crane bucket/concrete pumps as per site condition.
- Concrete shall be laid in 350-400mm layer and vibrated with needle (electrical/petrol/diesel) vibrators.
- It shall be ensured that concreting is continuous and completed in a single pour to minimize the number of cold joints.
- The exposed area of the walls shall be green cut to receive the next lift concrete, and shear keys (Construction Joint) shall be formed as per the construction drawing.
Formwork removal, inspection & curing:
- After gaining strength over about one day, the side form panels shall be safely removed, cleaned and stacked for future use.
- The demoulded concrete surfaces shall be inspected for blemishes and, if noticed, shall be mended immediately as per the approved methodology.
- The exposed concrete surfaces shall be covered with moist Hessian cloth and shall be maintained moist over the curing period.
Box Culvert Deck with Wall 2nd lift & Corbel Construction(STAGE -3):
The general construction methodology shall be comprised of the following.
- Fabrication of shutter and reinforcement
- Staging
- Formwork and Reinforcement
- Concrete
Fabrication of Shutter & Reinforcement:
- Standard shutters shall be used, or requirement shutters shall be fabricated at a centralized fabrication yard as per drawing for GA of Formwork and Staging.
- The shutters shall be transported to the site by truck/trailer.
- Reinforcement shall be fabricated at the centralized yard as per BBS made following the latest “Good for Construction” Drawing and approved by the Engineer, and it shall be transported to the site by truck/trailer.
- Store the fabricated reinforcements on wooden/concrete sleepers to avoid any contamination from soil/groundwater.
Box Culvert Deck Slab Staging:
- After completion of the wall up to the required height, staging for the deck will start.
- An erect, vertical member in the form of props/H-Frame /MS Pipe/Cup-lock pipe above the base slab of RCC Box in between the walls as per staging drawing.
- Brace the vertical members in both directions and diagonally.
- Erect the longitudinal girder and cross girders as per the staging drawing.
Deck Slab Formwork & Reinforcement:
- Parallel with girder erection, fix the balance wall inner side shutter and align by taking support from the staging erected as per staging and formwork drawing of box culvert.ย
- Apply shuttering oil to the formwork before fixing it in position.
- Fix soffit shuttering over cross girder, check the soffit shuttering level and introduce necessary wooden packing below the shuttering joints for having provision for deshuttering and levelling.
- Apply shuttering oil over the soffit shuttering and start reinforcement work as per the Box culvert GFC drawings.
- Fix the prefabricated reinforcement bars for the deck and balance wall portion of the wall as per GFC drawings.ย
- Reinforcement cover shall be maintained as per GFC drawing by means of cover blocks placed at suitable intervals. The cover Block shall be of the same grade of concrete as used in the deck.
- Fix the reinforcement bars for the crash barrier reinforcement as per the box culvert GFC drawing.
- Fix the side/end shutter of the wall and deck after applying shuttering releasing agent.
- Foams or masking tape shall be used in joints to keep the formwork joints leak-proof.
- Support the side/end shutters by inclined support members, as shown in the formwork/staging drawing.
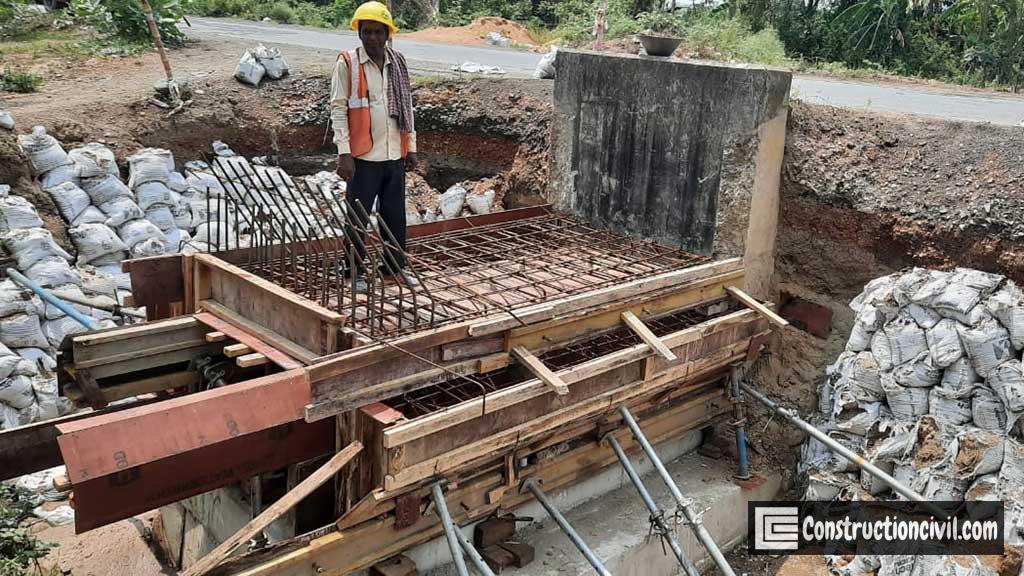
Also, Read: Types of Deep Foundation in Civil Engineering
Box Culvert Deck Slab Concreting:
- After checking of staging, formwork and reinforcement, cast the wall and deck. Concrete shall be placed in a single continuous pour in such a sequence, avoiding the formation of cold joints.
- Concrete shall be produced in the controlled batching plant as per approved Mix Design and shall be transported to the site by Transit Mixer.
- The slump and concrete temperature shall be checked at the site before pouring, and it should be as per the requirement.
- Concrete shall be poured into the formwork by a Static Concrete Pump/placer boom without disrupting to avoid cold joints.
- Separate arrangements for concreting shall be kept ready for any significant mechanical fault of concreting equipment.
- The needle vibrator must be operated vertically with or without the shutter vibrator. No vibrator should run for more than 2 minutes in one place to prevent segregation.
- Do not allow any pocket formation or honeycomb in the concrete, and feel the concrete flow by hammering the shutters with a wooden mallet.
- Deck concrete top-level shall be finished smoothly.
- Remove the end and side shutter after 24 hrs of concreting.
- Start curing of deck and wall by using a wet hessian cloth or continuous water sprinkling arrangement to keep the girder wet for up to 14 days.
- The soffit and staging shall be removed depending on the span length as per guidelines of IS 456:2000.

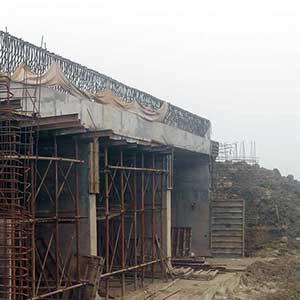
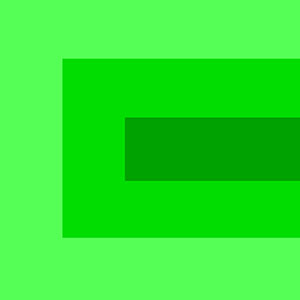
Dear Krishna, I am very glad that you started a helping chain for Civil Engineers. I am requesting you to post about estimating and costing as I am poor in this.
Thanks in advance.๐