Here we will know more about the Defects in concrete, their Prevention and Repair. Repair of Concrete Surface Defectsย is the process of fixing a hardened concrete surface that has not fulfill the acceptance criteria and standard.
What is Defective Concrete?
Defective concrete does not meet the specified strength requirements, and generally, acceptance criteria are laid down based on the percentage of defectives. i.e. specimens are falling below the stipulated strength. A concrete that shows defects on the surface during construction or within a short time after completion of concrete showing cracks before or after hardening is also called defective concrete.
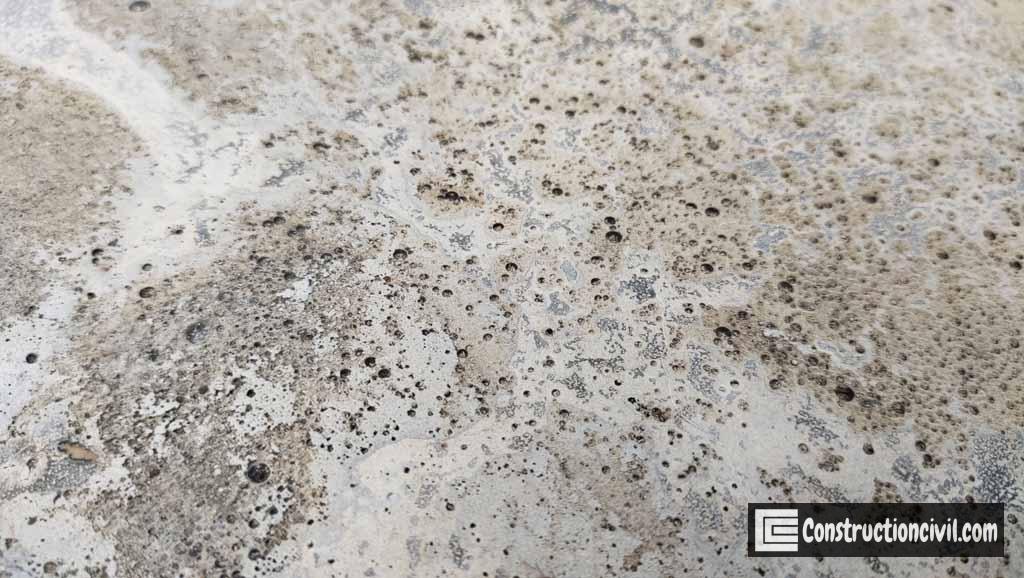
Also, Read: Blowholes/Surface voids/Bugholes in Concrete Surface
How do we know?
The concrete does not meet the strength requirements indicated by the low compressive strength, but which is apparently good will not often get detected until it cracks or fails under service conditions. After detection, investigations are undertaken, and costly repairs are planned.
Concrete surface defects:
The defects mentioned below are usually seen over concrete surfaces
- Honeycombing
- Air pockets land bolt holes
- rock pockets and grovels streaks
- sand streaking
- laitance
- rust stains
- dusting
- surface scaling.
The above defects are usually caused by poor quality materials, improper mix design, and lack of proper placing, compacting and curing procedures. Theย repair of concrete surface defectsย are both problematic and costly, and even the best repair work will not be as good as an original, properly finished surface.
Causes, Prevention and Repair of Concrete Surface Defects:
Honeycombing in Concrete:
- This is caused by a harsh dry mix or a non-cohesive mix of a watery consistency, improperly placed and not properly consolidated.ย
- To avoidย repair of concrete surface defects need attention to mix design, good aggregate grading, proper placing and systematic vibration or rodding will avoid the occurrence of honeycombed patches.ย
- Repair of concrete surface defects involves removing the defective concrete and replacing it with good concrete, which is the only effective method of repair.
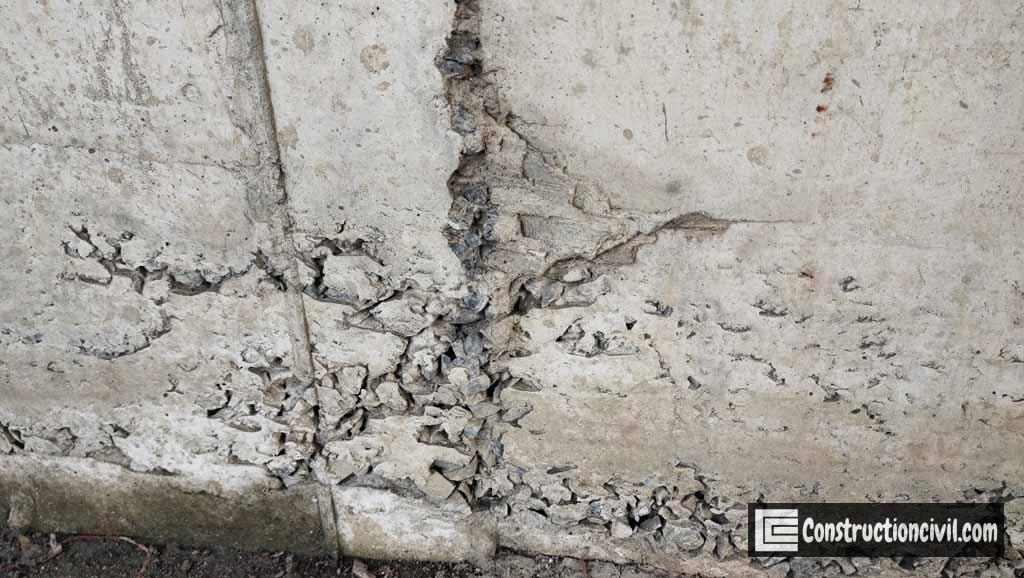
Air pockets and Bolt holes in concrete:
- Air pockets on the formed surface occur due to the excessive amount of form oils or the use of over-sanded mixes. Excess oil on the form causes the air bubbles to stick to the surface, and the over-sanded mix makes it more difficult for the bubbles to escape upward through mortar.
- Using a well-designed mix and proper concrete pour plan considering the height of fall, layer thickness and consolidation of each layer by vibration with precaution to packing along the forms should remove the air pockets.
- Air pockets and bolt holes can be filled by dry pack mortar. This should be carefully packed in place in small amounts.
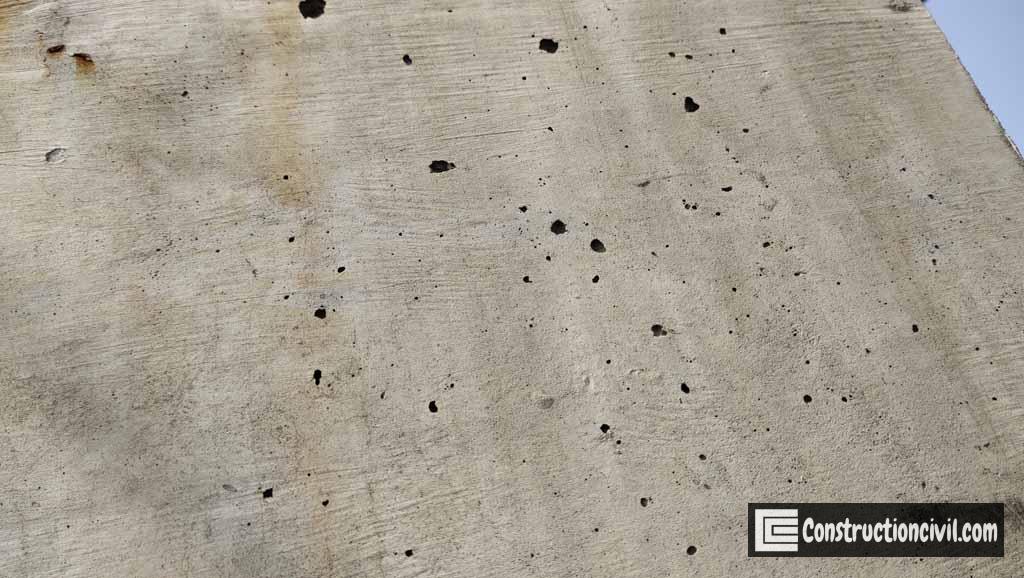
Also, Read: Concrete Ingredients – Important Properties and Tests
Rock pockets and gravel streaks in concrete:
- The loss of cement or mortar through cracks present in the formwork causes rock pockets, and this is more likely to occur when the concrete is consolidated by vibration.ย
- Such repair of concrete surface defectsย is very complicated and need special care.
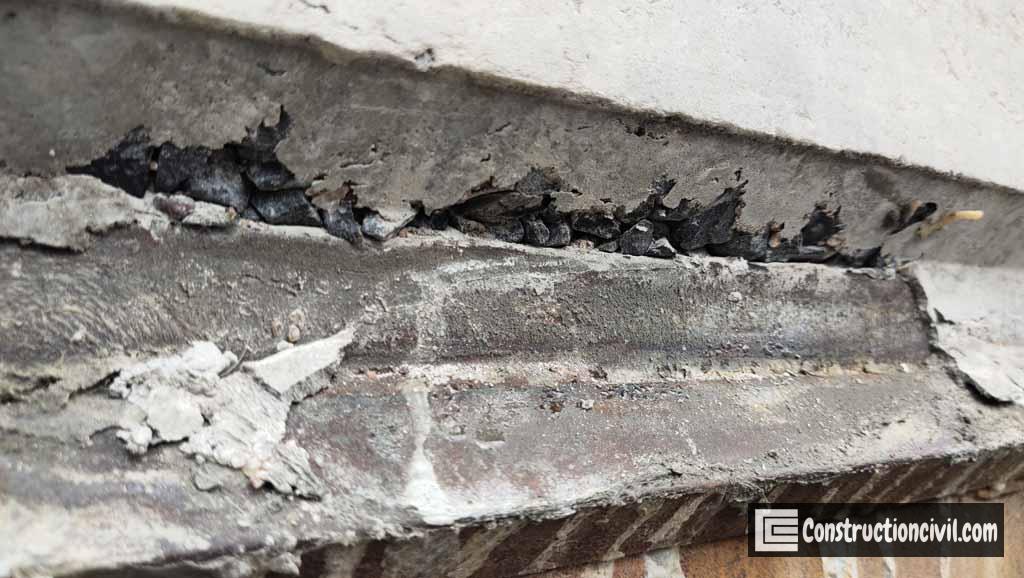
Sand streaking in concrete:
- The use of wet, over-sanded mix that bleeds excessively is the primary cause of sand streaking on the formed surface of the concrete.ย
- We can avoid suchย repair of concrete surface defects by using proper vibration in case of stiffer mixes or air-entrained concrete and using more cohesive and bleeds less concrete mix.
- Such repair of concrete surface defectsย is very complicated and need special care.
Laitance in Concrete:
- It is a mixture of cement, fine sand and water that accumulates on the top of the finished concrete surface. These types of surface defects appear when wet concrete mix bleeds excessively.
- Laitance leaves a light coloured streak of poor concrete between successive lifts; it has high permeability and is vulnerable to freezing and thawing.ย
- We can avoid suchย repair of concrete surface defects by usingย a well-designed concrete mix.
- Laitance on the top of the concrete layer should be removed entirely by wet sandblasting before placing the next lift.
Rust stains in Concrete:
- These are caused by reinforcing steel or some iron-bearing mineral substances in aggregates or outer surfaces of concrete.ย
- During tying or welding of reinforcement, pieces of binding wires or molten weld metal are likely to drop in the formwork, which on rusting may cause rust stains in concrete.ย
- Reinforcing rods with little or no cover would start staining on oxidation causing rust stains in concrete.ย
- We can avoid suchย repair of concrete surface defects by proper care during reinforcement fixing and providing adequate cover, which is mentioned in the design drawing.
- We can remove rust stains by washing the surface with oxalic acid.
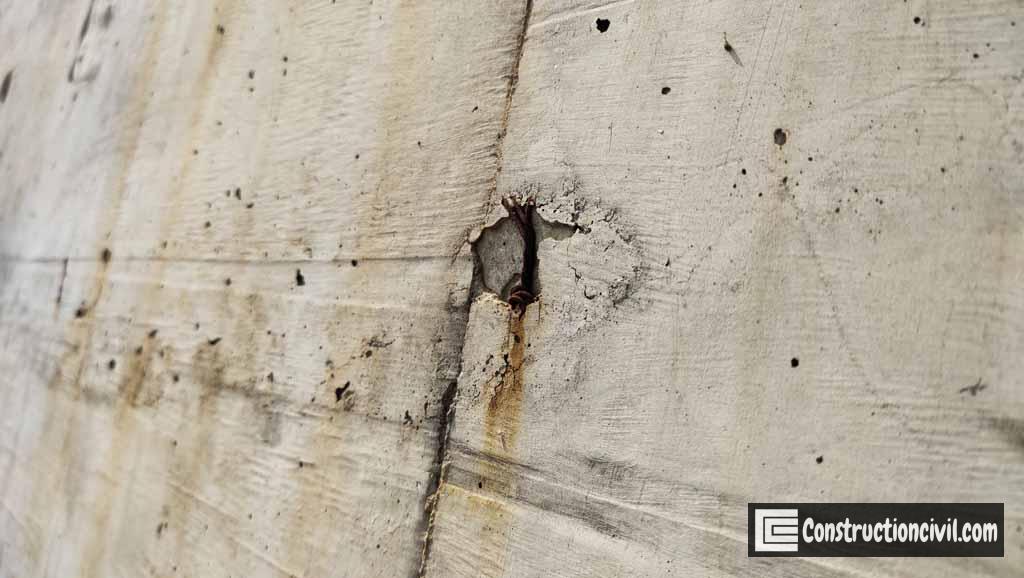
Also, Read: Rusting of Iron Rebar in Concrete – Special Repairing
Dusting in concrete:
- The presence of excess clay or silt in the concrete mix will cause dusting.
- Premature floating and trowelling will bring an excess of fine materials with water to the surface to produce a soft cement paste that will cause dusting.
- Spreading dry cement on the concrete surface for early finishing will cause dusting.
- Inadequate curing also causes dusting.
- Surface treatment with a magnesium or zinc fluosilicates or sodium silicate solution will harden the surface and reduce dusting.
Surface scaling in concrete:
- Surface scaling in concrete is caused by improper finishing and inadequate curing or by applying salts for snow and ice removal in the case of non-air entrained concrete. Sometimes dusting also causes thin scaling.
- We can avoid surface scaling in concrete by selecting suitable construction materials and taking proper care during finishing and curing as per design requirements and technical specifications.ย
- Clear loose concrete by gentle hammering and clean the concrete surface free from dirt and debris. After cleaning, dampen the cleaned surface andย apply a bonding agentย before the next concrete layer for resurfacing. Place particular concrete type to resurface the damaged surfaces.
- Such repair of concrete surface defectsย is very complicated and need special care.

Also, Read: Design Mix of Concrete – Detailed Procedure
Cracks in Concrete:
- Another type of surface defect in concrete is cracking, and cracks may be surface cracks, shallow cracks, deep and thorough cracks etc. On the other hand, there are two types of cracks map cracks and single continuous cracks considering crack patterns.
- Map cracks are uniformly distributed short cracks running roughly in a hexagonal pattern, whereas continuous cracks run indefinitely, often parallel at the definite interval.
- Besides the above types, there are internal cracks around larger stone pieces, or unsoundness cracks form chemical reactions or cracks along reinforcing bars due to corrosion.ย
- To avoid such repair of concrete surface defects due to cracks involves proper understanding of the various reasons is essential while designing, selecting materials and construction methods to prevent cracking or at least keeping it down to an acceptable level.
- Cracks once appeared cannot be repaired until they assume a severe form resulting in the spoiling of concrete or widespread damage.ย
- Cracking should, therefore, be prevented by careful attention to various details of design and construction, ensuring good quality of concrete and by proper technique.
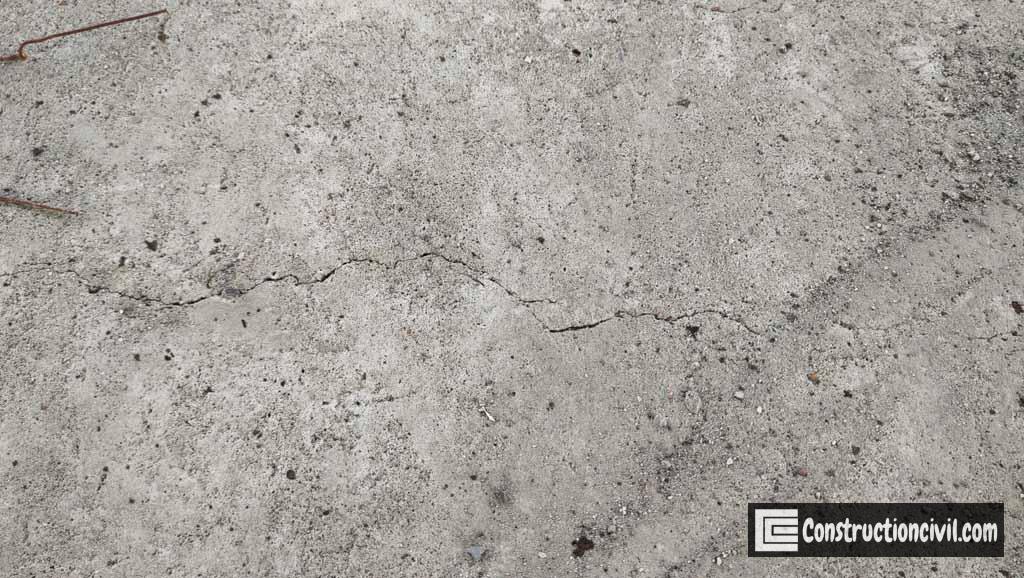
Also, Read: Environment Health and Safety(EHS)


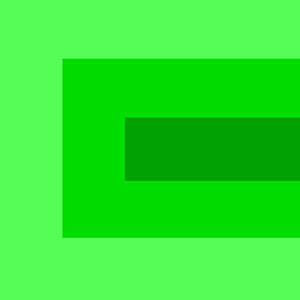
Your posts are so amazing and informative. Plzz keep it up and brings more informative knowledge on your post, so that everyone could get it.
Thanks
Very good sir . Very useful website for civil engineering professionals and students.