The method of choosing suitable ingredients and determining their relative amounts to produce concrete of the desired objective is known as the design mix of concrete.
Concrete Mix design objectives:
- Meet the minimum compressive strength required from structural consideration.
- Fulfil all requirements like durability to resist the environment in which the structure is exposed during service.
- Adequate workability necessary for easy compaction with the available equipment.
- Fulfil site requirements, especially the methods of concrete production, transport, placement, compaction and finishing.
- To produce concrete as economical as possible with a suitable design Mix of concrete.
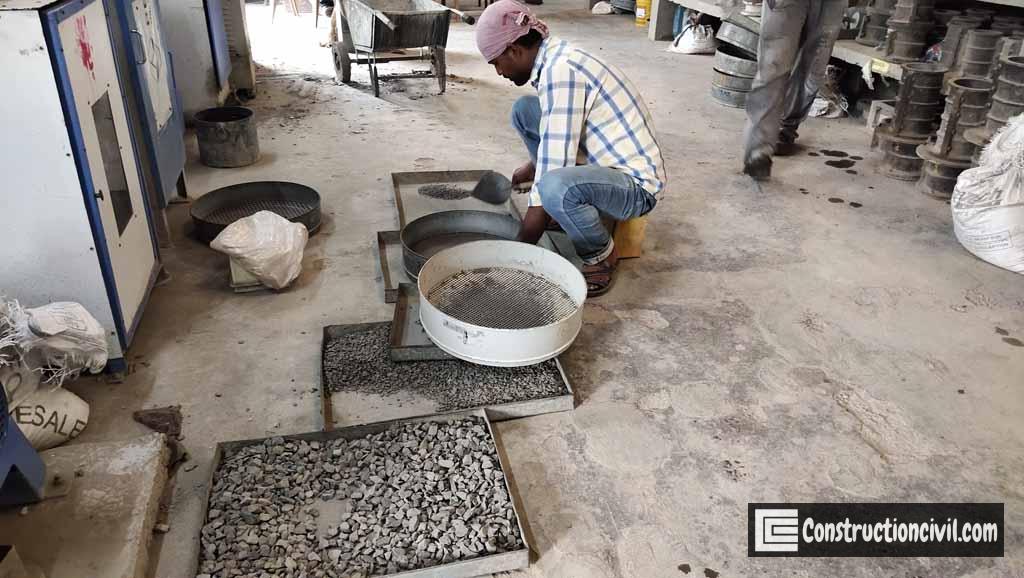
Also, Read: Concrete Ingredients – Important Properties and Tests
Factors influencing the choice of Design Mix of Concrete:
- Minimum w/c ratio for strength and durability can be achieved by increasing cement content and lowering the water content. Water demand can be lowered by controlling aggregate grading and using water-reducing admixture.
- Workability increases with maximum aggregate size. However, the smaller size of aggregate provides a larger surface area for bonding with mortar matrix giving higher strength.
- Grading of concrete aggregate: Relative proportions of coarse and fine aggregates play an essential role, and for dense concrete mix, the aggregates must be well graded.
- Minimum cement content in concrete: As per MORTH, Section 1700, Table 1700-2 For Bridges With Prestressed Concrete or those with Individual Span Lengths More than 60.0 M or those that are Built with Innovative Design/Construction:
Structural Member | Min. cement content for all exposure conditions (kg/cu.m) | Max. water cement ratio for all exposure conditions | Strength of Concrete Moderate exposure conditions | Strength of Concrete Severe exposure conditions |
PCC members | 360 | 0.45 | M25 | M30 |
RCC members | 380 | 0.45 | M35 | M35 |
PSC members | 400 | 0.40 | M35 | M40 |
Also, Read: Blowholes/Surface voids/Bugholes in Concrete Surface
- As per MORTH, Section 1700, Table 1700-3 For Bridges other than those mentioned in Table 1700-2 and for Culverts and other Incidental Construction.
Structural Member | Min. cement content Moderate Exposure Conditions | Min. cement content Severe Exposure Conditions | Max. water cement ratio Moderate Exposure Conditions | Max. water cement ratio Severe Exposure Conditions | Strength of Concrete Moderate exposure conditions | Strength of Concrete Severe exposure conditions |
PCC members | 250 | 310 | 0.50 | 0.45 | M15 | M20 |
RCC members | 310 | 360 | 0.45 | 0.40 | M20 | M25 |
Also, Read: Factors Affecting Strength of Concrete – Construction Civil
- Maximum cement content in concrete: The maximum cement content for any standard concrete (not special concretes) is generally restricted to about 450 kg/m3 as per MoRTH specification. This restriction is from durability consideration as higher cement produce high heat of hydration and more shrinkage cracks. But in the case of modern special concrete viz. SCC or HPC, the content of cementitious material is much more (up to 700 kg/m3). Probably the cement in code means OPC. In SCC or HPC, the pozzolanic reaction between fly ash and lime generates less heat, resulting in reduced thermal cracking when fly ash replaces a percentage of Portland Cement.
Also, Read: Concreting in Construction – Planning and Execution Summary
Factors Influencing Concrete Consistency (Slump):
From the design mix of concrete, the consistency of freshly mixed concrete depends on several factors, which are as follows:
- Water Content
- Water cement ratio
- Fineness Modulus of aggregate
- Use of Water reducing admixture(Plasticizers or Superplasticizers)
- Type and shape of aggregates
- Entrained air content
- Some secondary factors include concrete mix temperature, aggregate’s dust, type of cement, additions (silica fume, fly-ash, slag, fibres), etc.
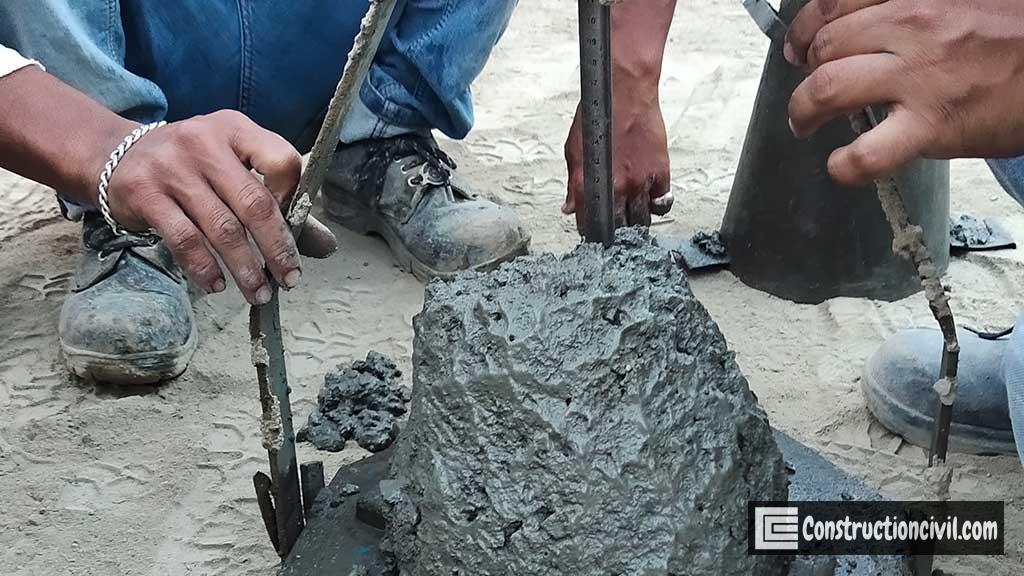
Also, Read: Properties of Concrete – Introduction to Good Concrete Practice
Factors Affecting Strength of Concrete:
Hardened concrete strength from a design mix of concrete depends on several factors, which are as follows:
- Water cement ratio
- Strength of cement used
- Type and shape of the aggregate
- Entrained air Content
- There are some secondary factors too, such as Mix temperature, etc.
Concrete Mix Design Methods:
- IS Method
- ACI Method
- Road Note Method(UK Method)
- IRC44 Method
- Arbitrary Method
- Maximum density Method
- Fineness modulus Method
- Surface Area Method
- Mix Design for high strength concrete
- Mix Design for pumpable concrete
- DOE (British) Mix design method
Also, Read: Sieve Analysis of Coarse Aggregate Test – Construction Civil
Design Mix of Concrete – Detailed Procedure for M30 Structure as per IS: 10262:
A Stipulations for Proportioning:
- Grade designation : 30 N/mm2
- Type of cement: OPC 43 grade conforming to IS 8112
- Maximum size of aggregate: 20 mm
- Cement Content( Min): 310Kg as per Table No-1700-3 of MoRT&H
- Water-Cement Ratio(Max): 0.45 as per Table No-1700-3 of MoRT&H
- Degree of workability: 100mm Slump
- Type of exposure: Moderate
- Methode of concrete placing: Manually
- Degree of supervision: Good
- Aggregate: Crushed angular aggregate
- Chemical admixture type: Superplsticizer as per IS 9103
Test Data for Materials:
- Cement Used: OPC 43 grade conforming to IS 8112, Specific Gravity: 3.15
- Chemical admixture: Conforming to IS 9103, Specific Gravity: 1.225, Dosage: 1.1
- 20mm coarse aggregate: Specific Gravity 2.88, Water absorption 0.59
- 10mm coarse aggregate: Specific Gravity 2.88, Water absorption 0.72
- Fine aggregate(River sand): Specific Gravity 2.66, Water absorption 1.78
- Water: Specific Gravity 1.00
- Combined proportion of coarse aggregates: 20mm aggregate(m) 60 %, 10mm aggregate(n) 40%
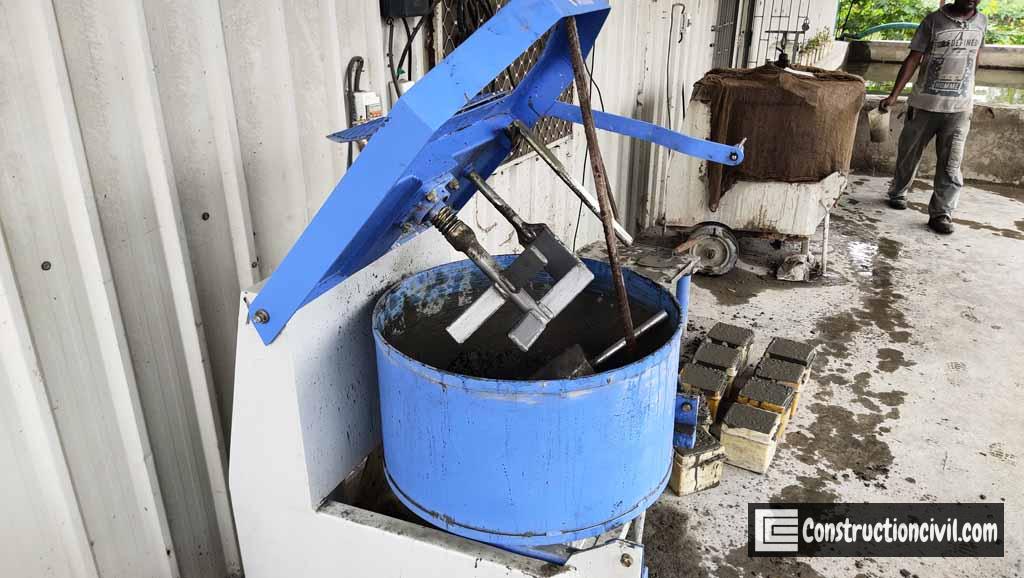
Also, Read: Causes, Prevention and Repair of Concrete Surface Defects
Determine Target mean strength of concrete:
Target Mean Strength: 42 N/mm2 for M30 grade concrete as per section 1700, Table No.1700-5 of MoRT&H.
or, As per IS:456-2000, Target mean strength of concrete(ft)
ft = fck + k. s
where ft = target mean compressive strength at 28 days,
fck = Characteristic compressive strength at 28 days,
k = usually 1.65 as per is 456-2000,
s = standard deviation.
Grade of concrete | Assumed Standard Deviation(N/ mm2) |
M10 | 3.50 |
M15 | 3.50 |
M20 | 4.0 |
M25 | 4.0 |
M30 | 5.0 |
M35 | 5.0 |
M40 | 5.0 |
M45 | 5.0 |
M50 | 5.0 |
Also, Read: Defects in Concrete Structure – Types – Causes and Condition Survey
Selection of Water Cement Ratio:
Consider the W/C = 0.43 <0.45hence OK as per Table No.1700-3 of MoRT&H.
or, As per IS:456-2000, Choose w.c.ratio against max w.c.ratio for the requirement of durability criteria as per IS 456- 2000 ,table 5.
Make a more accurate estimate of the preliminary water-cement ratio corresponding to the average target strength.
- As per the modern study, capillary porous start to be connected when the water-cement ratio is higher than 0.40
- Higher is the aggressiveness of the environment, and lower should be the water-cement ratio.
- For structure concrete exposed to a very hostile environment, the water-cement ratio should be lower than 0.40.
Selection of Water Content:
- As per IS 10262: 2009, Table 2 for nominal maximum Size of 20mm Aggregates, water content per cubic meter of concrete is equal to 186 Kgs(20-50mm slump range).
- Add 3% for every additional 25mm slump that is 6.0%
- Estimate water content for 100mm slump is equal to (186+((6.0/100)x186) = 197.16 kg
- As per manufacture specifications, when extra water reducing superplasticizer is used, the water content can be reduced up to 30%.
- We are considering 23.5% of water reduction here by dosing admixture of 1.10% by weight of cement, based on the trial.
- Hence the arrived Water content rounded off = 197.16-((197.16ร235)/100๏ผ=150.83, hence 151kg

Also, Read: Determination of Sieve Analysis For Fine Aggregate
For Other Conditions if Any:
Condition | Correction |
Sub-Angular Aggregates | -10 Kg |
Gravel + Crushed Particles | -20 Kg |
Rounded Gravel | -25 Kg |
Determination of Cement Content:
Calculate the cement content from the water-cement ratio and final water content arrived after adjustment. After Checking the cement content so calculated against the minimum cement content from the requirement of
durability or as per MORTH specification, and Select greater of the two values.
- Free Water Cement Ratio 0.43
- Cementitious material 350 kg/cum
The Proportion by Volume of Coarse and Fine Aggregate Content:
- As per IS 10262: 2009, Table 3 volume of coarse aggregate corresponding to 20mm size and fine aggregate (Zone II) for the water-cement ratio of 0.50 is equal to 0.62.
- In our case, the water-cement ratio is 0.43; therefore, the volume of coarser side aggregate is required to be increased to decrease the fine aggregate content.
- As the W/C ratio is lowered by 0. 07, the proportion of the volume of coarse aggregate is increased by 0.014 (because the rate of +/- 0.01 for every +/. 0.05 changes in WC ratio).
- Therefor,corrected proportion of volume of coarse aggregate for water cement ratio of 0.43 is equal to (0.62+0.014) = 0.634.
- For more workable concrete mixes required for the pump, we can reduce the estimated coarse aggregate content up to10% per IS 10262: 2009, clause 4.4.1.
- Here we consider 5% coarse aggregate reduction so now the coarse aggregate content (Vca) = 0.634 x0.95 = 0.602 say 0.60
- Volume of fine aggregate (Vfa) =1-Vca =0.40
Design Mix of Concrete – Calculationlation:
- Concrete volume: 1.000 cum
- Cement volume: (Mass of cement)/(Specific gravity of cementx1000) = 0.111cum
- Water volume: (Mass of water)/(Specific gravity of waterx1000) = 0.151cum
- Volume of chemical admixture: (Mass of chemical admixture)/(Specific gravity of chemical admixturex1000) = 0.0031 cum
- Volume of all in aggregate: [a – (b + c+ d)] = 0.735
- Mass of coarse aggregate Wca: (f x Vol of coarse Agg x Sp.Gravity of Coarse Agg x1000) = 1270 kg
- Mass of fine aggregate Wfa: (f ร Vol of Fine Aggx Sp.Gravity of Fine Agg x1000) = 782 kg
- Hence mass of 20mm agg (at 60%)= (0.60 x Wca) = 762 kg
- Hence mass of 10mm agg (at 40%)= (0.40 x Wca) = 508 kg
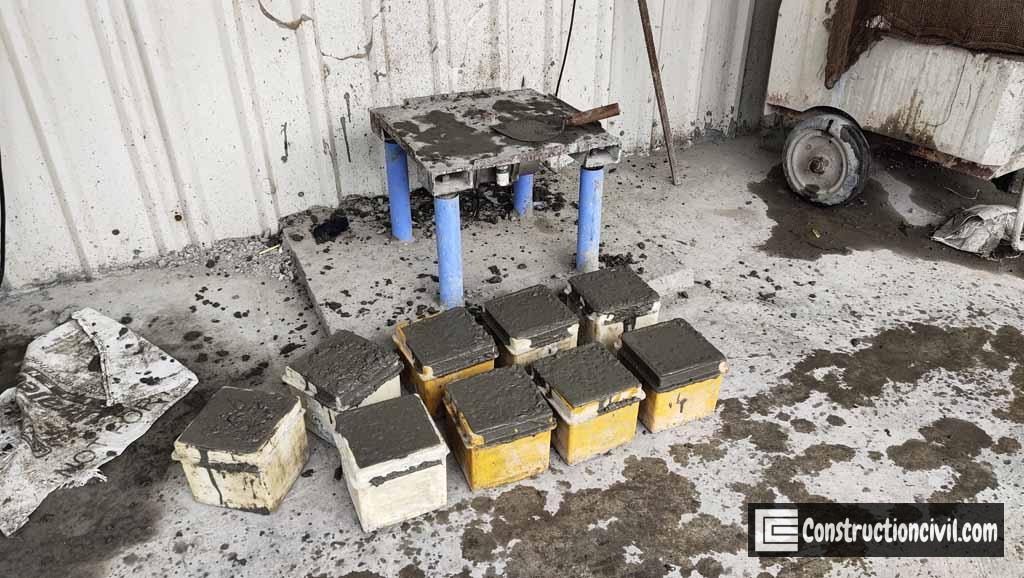
Design Mix Proportion:
From Design Mix of Concrete Mix mix proportions are
Cement (OPC 43 Grade) = 350 kg
20mm Aggregate = 762 kg
10mm Aggregate = 508 kg
Fine Aggregate = 782 kg
Free Water = 151 kg
Admixture = (1.1%) 3.85 kg

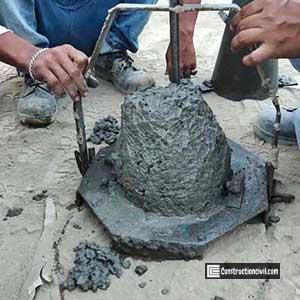
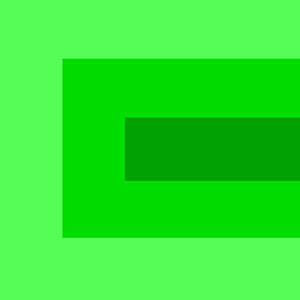