Filter media in road construction consist of coarse sand, gravel or stone conforming to Filter Media’s requirement spelt out in MoRTH technical specifications. One or more layer of graded materials act as a filter media shall be provided underneath the pitching, behind abutment, retaining wall, wing wall, RE wall including various types of earth retaining structure to prevent loss of embankment material and build-up of hydrostatic pressure or water pressure on the walls.
- The finer filter shall be considered as a base material for the selection of a coarser filter.
- The filter shall be compacted to a firmed condition.
- The layer thickness of the filter media in Road Construction not exceeding more than 250mm.
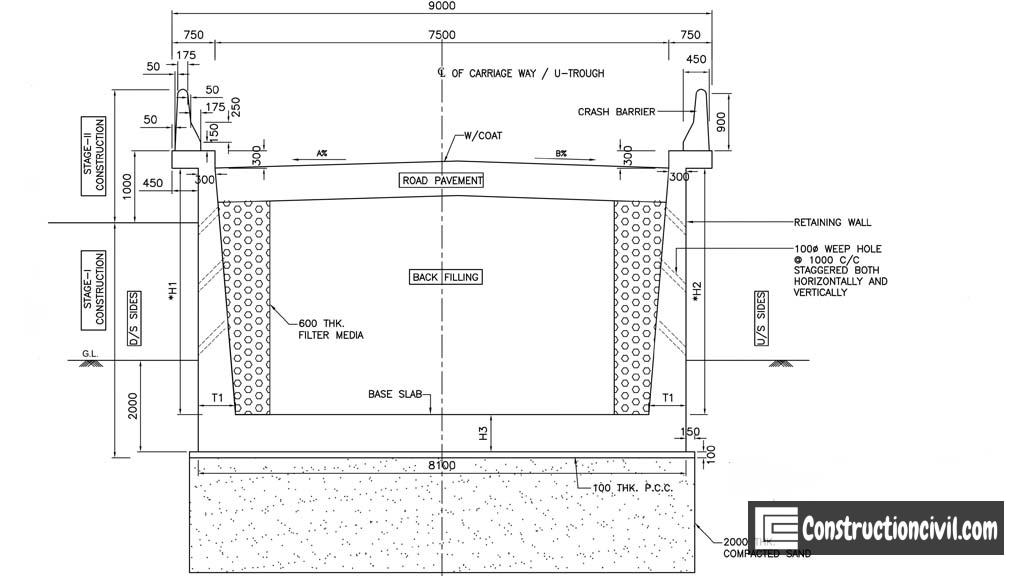
Grading Requirements For Filter Media in Road Construction:
As per MORTH, Table 300-4: Grading Requirements for Filter Material – Percent Passing by Weight
Sieve Designation | Class-I | Class-II | Class-III |
53 mm | – | – | 100 |
45 mm | – | – | 97-100 |
26.50 mm | – | 100 | – |
22.40 mm | – | 95-100 | 58-100 |
11.20 mm | 100 | 48-100 | 20-60 |
5.60 mm | 92-100 | 28-54 | 4-32 |
2.80 mm | 83-100 | 20-35 | 0-10 |
1.40 mm | 59-96 | – | 0-5 |
710 micron | 35-80 | 6-18 | – |
355 micron | 14-40 | 2-9 | – |
180 micron | 3-15 | – | – |
90 micron | 0-5 | 0-4 | 0-3 |
Selection of Grading:
- For the fined grained type of soil like clay/silt backfill material shall confirm to class-I.
- For coarse silt to medium sand or sandy type soil backfill material shall corresponds to class-II
- For the gravelly type of sand, backfill material shall correspond to class-III
Additional Specification:
In order to fulfil the requirement, as per MORTH section 2500, the filter may be provided in one or more layers meeting the following criteria :
- D 15 (Filter)/D 85 (Base) <5
- D 15 (Filter)/D 15 (Base) >4 & <20
- D 50 (Filter)/D 50 (Base) <25
Where, D15 means the size of that sieve which allows 15% (by weight) of the filter material passing through it and similar is the meaning of D50 and D85.
Gradation of Filter media for RE wall:
The desirable gradation of the aggregate used as filter media for RE wall backfilling is indicated in Table 2, IRC SP 102
Sieve Opening | Percentage Finer |
37.50 mm | 90-100 |
20.00 mm | 80-100 |
12.50 mm | 0-20 |
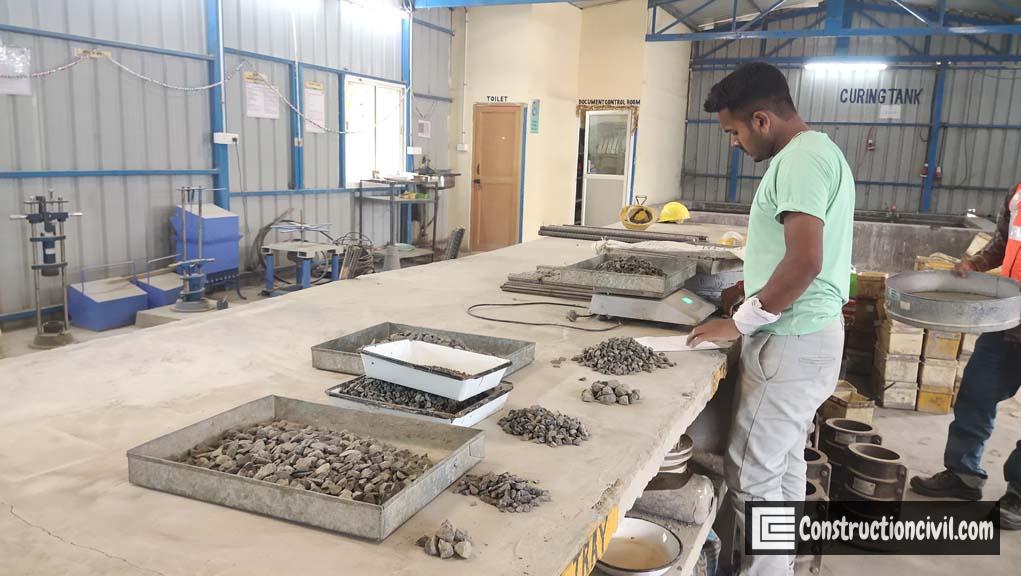
Filter Media Construction:
Equipment and Machinery:
The following, Equipment and Machinery shall be deployed for execution of Filter Media.
- JCB/Excavator
- Tippers/Dumpers (6 โ 8m3)
- Rollers – (2 Ton Capacity)
- Rammers/Plate Vibrators
- Water tanker (10.000Lit Capacity)
Filter Media Laying Procedure:
For Earth Retaining Structure:
- The filter material shall be well packed to a total thickness of 600 mm width or as specified in design and drawing.
- With smaller size towards the soil as a base and bigger size towards the wall as filter @ 300mm width each and provided over the entire surface behind abutment, wings or return walls, Retaining Walls to the height as shown in the drawing.
- A template of required size and shape shall be used to ensure regular and orderly deposition of the full indented quantity of filter and base material along the entire length and width of the Filter Media.
- The Filter Media shall be placed manually inside the 250mm thick template simultaneously with the fill material’s laying.
- The template shall then be removed after spreading and levelling.
- Sometimes weep holes/pipes need to be provided with filter media for earth retaining structures like abutment wall, retaining wall, wing wall and other below-ground drainage structures to remove seepage water from embankment/backfill material.
- In the RE wall case, after covering the gaps between the facia joints with geosynthetics, a filter media layer of a minimum of 600 mm width at the back of the fascia panel is commonly used, preventing loss of backfill material and reduces hydrostatic pressure.
Also, Read: RE Wall Construction – Important Guidelines
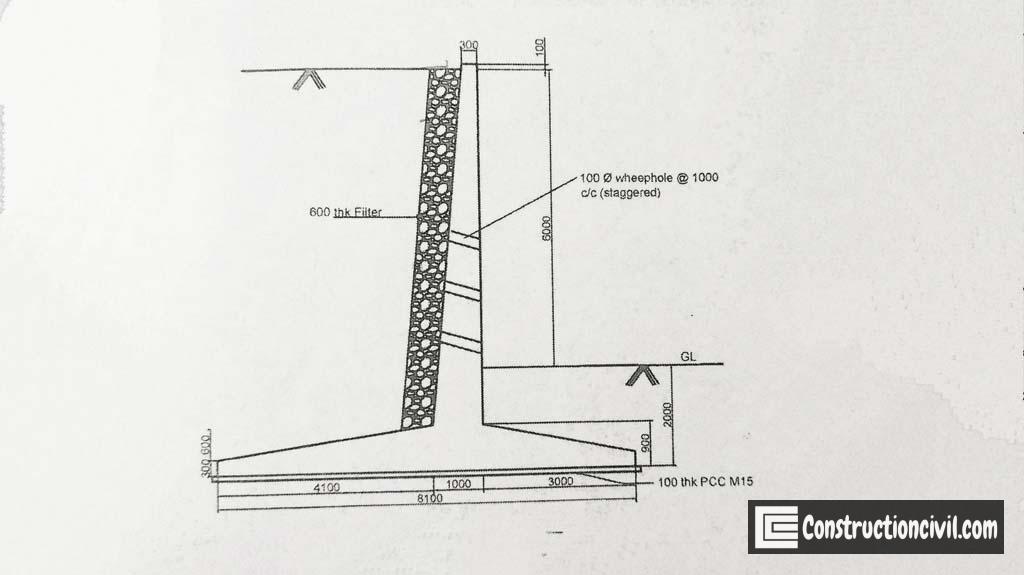
For Pipe Laying Work:
- Suitably graded backfill material shall be placed in full width of the trench bed before placing pipe and compacted as required to a minimum thickness of 150 mm or as per design and drawings. After that, the pipe shall then be embedded firmly on the bed.
- Perforated pipes shall be provided with their perforations on the downside to minimize clogging if required. The pipes shall be appropriately joined with the help of a coupler.
- In the case of non-perforated pipes, suitable geosynthetics or some other type material of not less than 150 mm width shall be used to permit entry of water but prevent fines from entering the pipes.
For Stone Pitching Work:
- Filter media shall be laid over the well compacted bade to a thickness specified on the drawings before starting stone pitching work.
- Pitching shall be started from the toe wall/curtain wall and built up in courses upwards.
- One or more filter media layers shall be provided underneath the stone pitching to prevent uplift head on the pitching.
Also, Read: What are Gabions?- Advantages and Construction Method
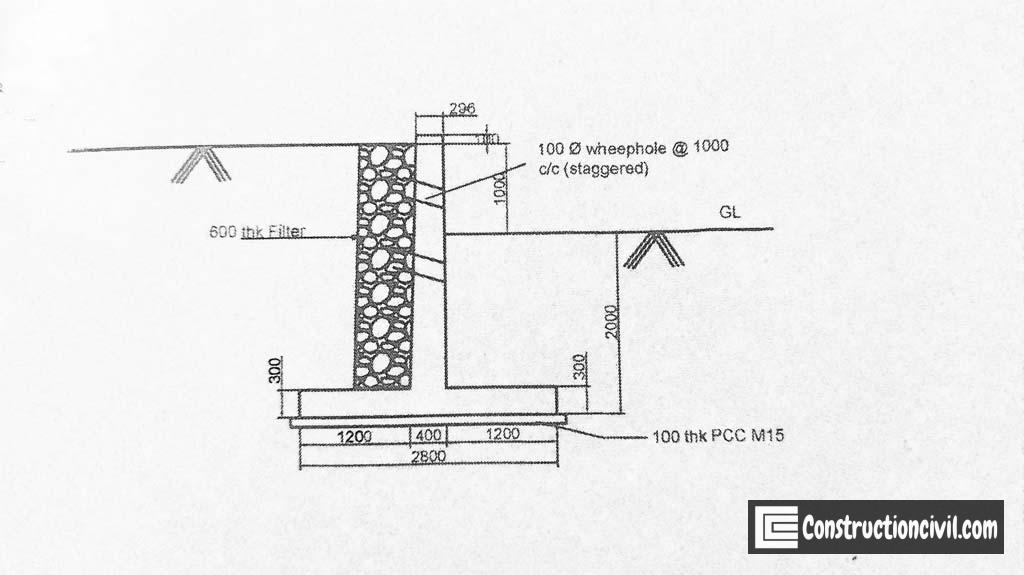
Compaction of Filter Media in Road Construction:
- The filter media and the fill material shall be compacted to the desired density using 2 Ton vibratory rollers.
- Where it is impracticable to use vibratory rollers, the compaction shall be carried out by appropriate mechanical means such as plate compactor or power rammer.
- Adequate care shall be taken to see that the compaction equipment does not hit or come to close to any structural member so as to cause any damage to them or excessive pressure against the structures.
Filter Media Construction Safety:
- All the vehicles engaged in filter media construction should have proper indicator arrangement.
- Reverse light, rearview mirror and reverse horn must be fitted with all the vehicles engaged.
- Break, steering condition, and tire pressure should be checked before the start of the activity.
- The proper speed limit should be maintained.
- Driver shall not drive a vehicle when he is not fit mentally and physically.
- Fences shall be provided wherever required, and also reflectors shall be placed for night vision.
- Proper caution boards, flag boys shall be placed to caution the vehicle movement at unloading points.
- Trained Supervisors shall be deployed at all the dumping sites.
- Unauthorized persons shall not be allowed within the critical work area.
- Periodical training shall be provided to drivers, helpers, bankmens, and flag boys.
- Proper supervision and planning of the activity shall be done.
Also, Read: Environment Health and Safety(EHS) Management – Important Guidelines


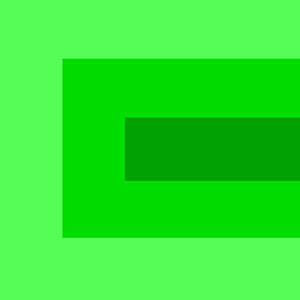