The primary purpose of lap length and development length, anchorage length, is to provide sufficient bond strength between reinforcement and concrete but in different situations. Development length depends upon the grade of concrete mix, reinforcement grade and diameter.
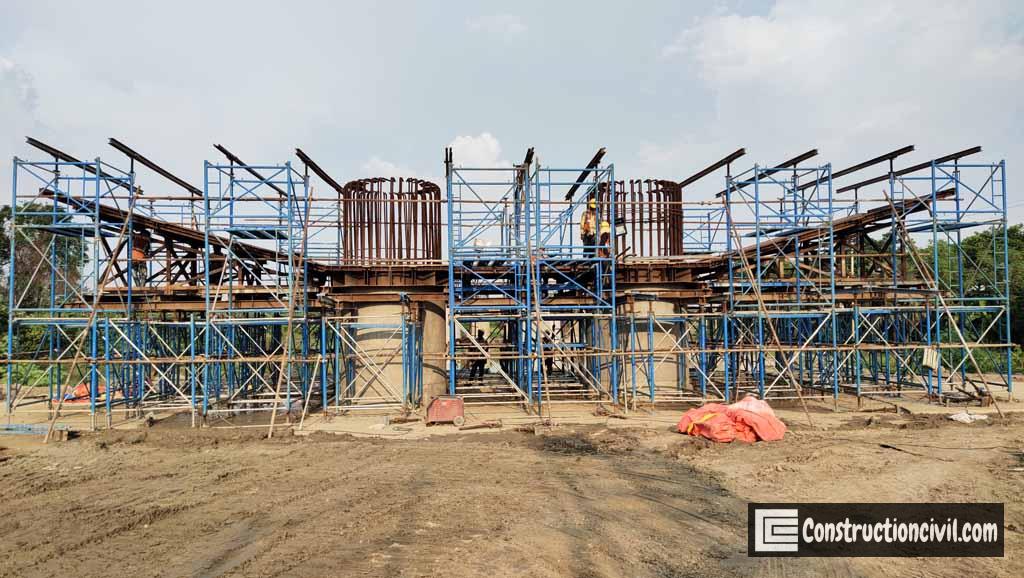
Also, Read: Concrete Ingredients – Important Properties and Tests
Development Length:
It is required to provide an additional length of reinforcement on either side of the point of the maximum stress zone so that the reinforcement bar doesn’t slip as it approaches the ultimate stress known as Development length. Under tension, it is called Development length in tension, and Similarly, we have to provide an extra length known as development length in compression for compression members. Furthermore, it is worth mentioning that due to the presence of ribs, deformed bars are superior compare to the smooth, mild steel bars.
Importance and Purpose of Development Length:
- It is necessary and essential to provide a sufficient bond between reinforcement steel and concrete to act together without any slip.
- Help to complete stress transfer to maintain the structure’s integrity and enable it to carry the loads.
- The plane section of a structural beam remains plane even after bending by giving a perfect bond between them. The required length of the reinforcement bar to develop the entire bond is known as anchorage length.
- Development length becomes highly essential when such design involves the curtailment of reinforcement steel.
- It is crucial to check lap length and development length for structural stability, including tension reinforcement for continuous beams and cantilever supports.
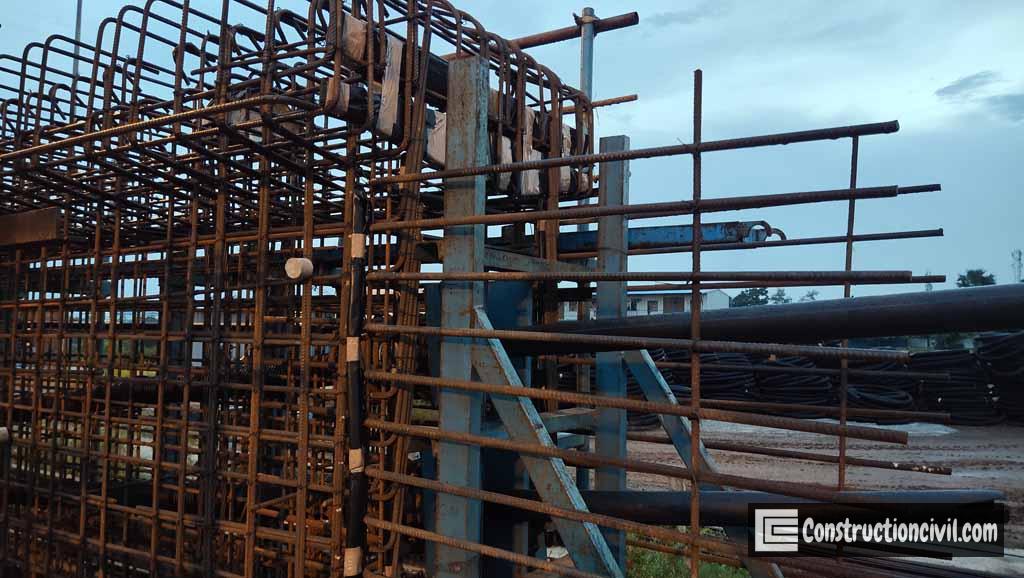
Also, Read: Design Mix of Concrete – Detailed Procedure With Calculation
Development Length Calculation:
- The plane section of a structural beam remains plane even after bending by giving a perfect bond between them. Here bond is estimated by bond stress, and depending on the bending moment, local bond stress varies along with the member. The average bond stress value is calculated throughout its anchorage length for further calculations.
- The bond stress is designated as the shear force per unit nominal surface area of the reinforcing steel. Shear force is acting on the interface between reinforcement and surrounding concrete and parallel to the reinforcement bars.
- An additional length of reinforcement of specified diameter to be provided beyond a given critical section after considering the design bond stress. Though this provision of additional development length may avoid the overall bond failure, slippage of a bar may not always result in the widespread failure of the beam.
Formula for Development Length:
Development length (Ld) = d x σs/4τbd
In the Formula for Development Length, d is for the diameter of the reinforcement bar, σs stress in the bar at the section considered as design load, and τbd is for design bond stress.
- The formula for Development Length includes anchorage values for hooks in tension reinforcement.
- For bars of sections other than circular, the development length should be sufficient to develop the stress in the rebar by bond.
- Design bond stress(τbd) in Limit State Method: As per IS 456:2000, Design bond stress(τbd) in Limit State Method for plain bars and deformed bars under tension shall be as follows:
Grade of concrete | M20 | M25 | M30 | M35 | M40 & Above |
Design bond stress for plain bars, Tbd N/mm2 | 1.2 | 1.4 | 1.5 | 1.7 | 1.9 |
Design bond stress for deformed bars, Tbd N/mm2 | 1.92 | 2.24 | 2.40 | 2.72 | 3.04 |
- Design bond stress(τbd) in Working Stress Method: As per IS 456:2000, Design bond stress(τbd) in Working Stress Method for plain bars and deformed bars under tension shall be as follows:
Grade of concrete | M20 | M25 | M30 | M35 | M40 | M45 | M50 |
Design bond stress for plain bars, Tbd N/mm2 | 0.8 | 0.9 | 1.0 | 1.1 | 1.2 | 1.3 | 1.4 |
Design bond stress for deformed bars, Tbd N/mm2 | 1.28 | 1.44 | 1.6 | 1.76 | 1.92 | 2.08 | 2.24 |
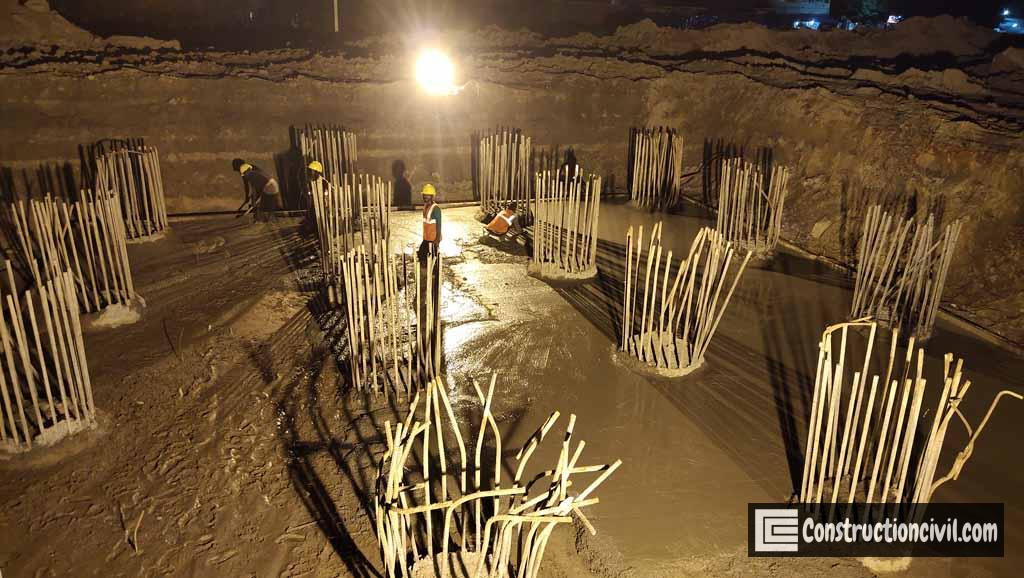
Also, Read: Concreting in Construction – Planning and Execution
- For deformed bars conforming to IS 1786, the values of bond stress should be increased by 60% compared to plain bars which are calculated as above.
- For reinforcement in compression, the values of bond stress for bars in tension should be increased by 25%.
Development Length for Bundle Bars:
In the case of bundle bars, the respective development lengths of each of the rebars for two, three or four rebars in contact are as follows.
- The development length(Ld) of each bar of bundled bars shall be that for the individual bar
- Increased by 10% for two bars in contact
- Raised by 20% for three bars in contact
- Increased by 33% for four bars in contact.
Anchorage Length:
The length of a reinforcement required to develop the entire bond is known as anchorage length, and the bond is measured by bond stress. End anchorage is the length of reinforcement that needs to be embedded into the support for complete stress transfer to maintain the structure’s integrity and thereby enable it to carry the loads.
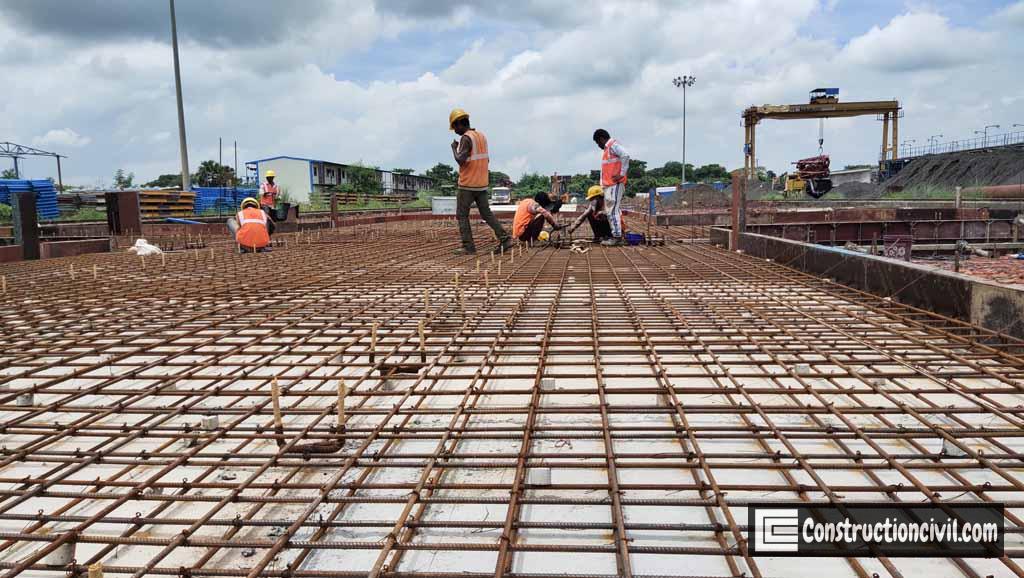
Also, Read: Rusting of Iron Rebar in Concrete – Special Repairing
Anchoring Bars:
Reinforcement bars may be anchored in a combination of providing development length to maintain the structure’s integrity. Such anchoring is explained below under tension and compression, respectively.
Anchoring Bars in Tension:
- if the development length requirement is satisfied, then Deformed bars may not need end anchorages.
- Typically, Hooks are provided for plain bars in tension.
- Standard hooks and bends length should be as per IS 2502 or as given in Table 67 of SP-16.
- For each 45° bend, the anchorage value shall be considered 4 times the rebar’s diameter, subject to a maximum of 16 times the rebar’s diameter for the standard bend.
- For a standard U-type hook, the anchorage length should be 16 times the diameter of the bar.
Anchoring Bars in compression:
- The anchorage value of straight compression bars shall be equal to its development length(Ld).
- The development length shall include the projected length of hooks, bends and straight lengths beyond bends if provided.
Anchorage Length Calculation:
Basic Anchorage Length = (K x Ø) mm
Where, Ø = Reinforcement bar diameter(mm)
As per IRC 112-2011, K values for Favorable Bond type:
Concrete Grade→ Re-Bar Grade↓ | M20 | M25 | M30 | M35 | M40 | M45 | M50 | M55 | ≥ M60 (mm) |
Plain Bars(Fe250) | 52 | 47 | 43 | 40 | 37 | 36 | 35 | 33 | 31 |
HYSD Bars(Fe415 & Fe415D) | 45 | 39 | 33 | 30 | 28 | 27 | 24 | 23 | 21 |
HYSD Bars(Fe500 & Fe500D) | 54 | 47 | 40 | 36 | 34 | 32 | 29 | 27 | 25 |
HYSD Bars(Fe550 & Fe550D) | 60 | 52 | 44 | 40 | 37 | 35 | 32 | 30 | 28 |
HYSD Bars(Fe600) | 65 | 57 | 48 | 43 | 41 | 38 | 35 | 33 | 30 |
- For unfavourable bond condition, the above values should be multiplied by a factor of 1.43
- For ƒ Ø>32mm, these lengths should be increased by multiplying factor 100/(132- Ø)
Reinforcement Lapping:
As per construction requirements, reinforcement needs to join to make it longer by overlapping sufficient length or welding to develop its entire design bond stress. Lapping should not be allowed in the maximum stress zone and should be staggered. As per IS 456, cl. 26.2.5, splices in flexural members should not be at sections where the bending moment is more than 50% of the moment of resistance, and not more than 50% of reinforcements shall be spliced at the same plane.
Reinforcement Lapping Length Calculation:
- Lap Splices can be used for reinforcement diameters up to 36 mm.
- The lapping of reinforcement should be staggered, and the centre to centre distance of the splices is a minimum of 1.3 times the lap length.
- The lap length, including anchorage of hooks under flexural tension, shall be equal to development length(Ld) or 30d, whichever is higher. The same under direct tension shall be 2x(Ld) or 30d, whichever is higher.
- The lap length under compression shall be equal to development length(Ld) but not less than 24d.
- The reinforcement lap length shall be determined on the basis of the smaller diameter reinforcement when bars of two separate diameters are to be spliced.
- The lapping of bundled reinforcement shall be made by splicing one rebar at a time, and all such individual splices in the bundle bar shall be staggered.
Reinforcement Lapping Length Formula:
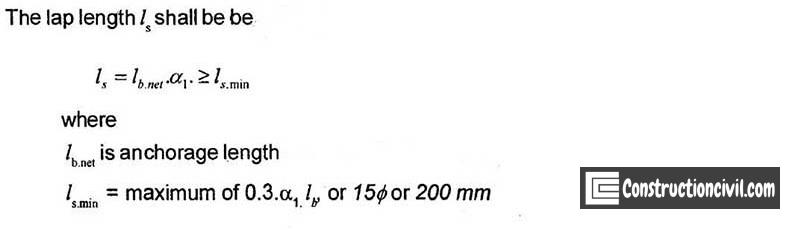
For Reinforcement Lapping Length coefficient α1 takes the following values
Percentage of lapped bars relative to the total cross-sectional area | <25% | 33% | 50% | >50% |
α1 | 1 | 1.15 | 1.4 | 1.5 |
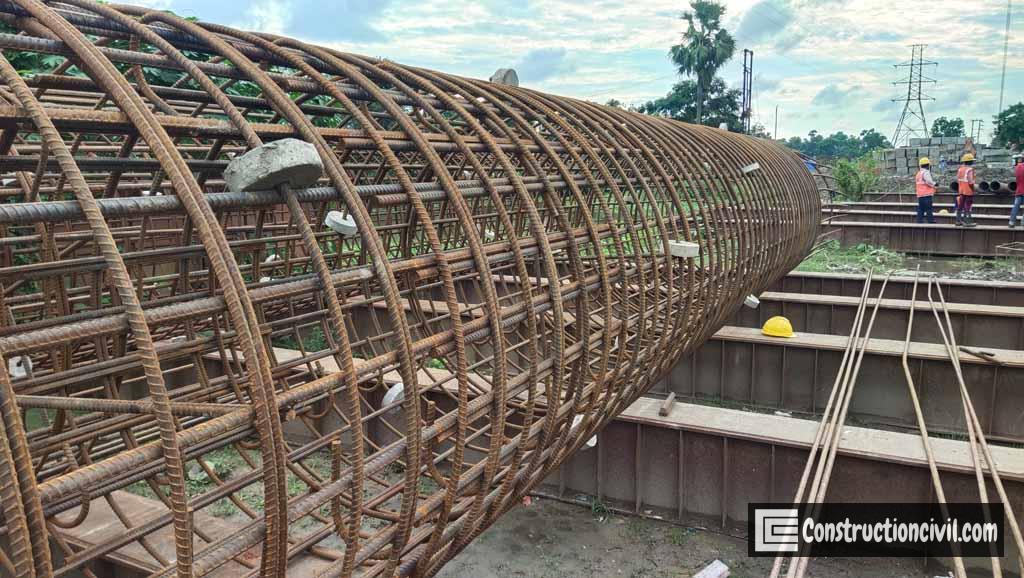
Reinforcement Lapping Length for <25% Lapping and Grade of Steel Fe500:
Sl. No. | Dia of bar (mm) | M35 (mm) | M40 (mm) | M45 (mm) | M50 (mm) | M55 (mm) | ≥ M60 (mm) |
1 | 10 | 360 | 340 | 320 | 290 | 270 | 250 |
2 | 12 | 432 | 408 | 384 | 348 | 324 | 300 |
3 | 16 | 576 | 544 | 512 | 464 | 432 | 400 |
4 | 20 | 720 | 680 | 640 | 580 | 540 | 500 |
5 | 25 | 900 | 850 | 800 | 725 | 675 | 625 |
6 | 32 | 1152 | 1088 | 1024 | 928 | 864 | 800 |
7 | 36 | 1350 | 1275 | 1200 | 1088 | 1013 | 938 |
8 | 40 | 1565 | 1478 | 1391 | 1261 | 1174 | 1087 |
Sl. No. | Dia of bar | M35 | M40 | M45 | M50 | M55 | ≥ M60 (mm) |
1 | 10 | 515 | 486 | 458 | 415 | 386 | 358 |
2 | 12 | 618 | 583 | 549 | 498 | 463 | 429 |
3 | 16 | 824 | 778 | 732 | 664 | 618 | 572 |
4 | 20 | 1030 | 972 | 915 | 829 | 772 | 715 |
5 | 25 | 1287 | 1216 | 1144 | 1037 | 965 | 894 |
6 | 32 | 1647 | 1556 | 1464 | 1327 | 1236 | 1144 |
7 | 36 | 1931 | 1823 | 1716 | 1555 | 1448 | 1341 |
8 | 40 | 2238 | 2114 | 1990 | 1803 | 1679 | 1554 |
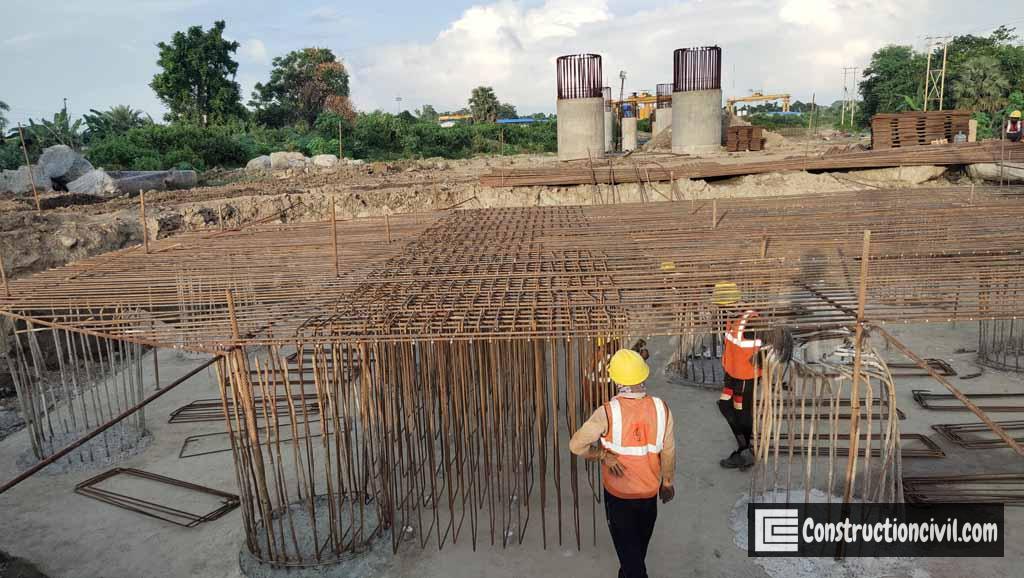
Reinforcement Lapping Length for 33% Lapping and Grade of Steel Fe500:
Sl. No. | Dia of bar (mm) | M35 (mm) | M40 (mm) | M45 (mm) | M50 (mm) | M55 (mm) | ≥ M60 (mm) |
1 | 10 | 414 | 391 | 368 | 334 | 311 | 288 |
2 | 12 | 497 | 469 | 442 | 400 | 373 | 345 |
3 | 16 | 662 | 626 | 589 | 534 | 497 | 460 |
4 | 20 | 828 | 782 | 736 | 667 | 621 | 575 |
5 | 25 | 1035 | 978 | 920 | 834 | 776 | 719 |
6 | 32 | 1325 | 1251 | 1178 | 1067 | 994 | 920 |
7 | 36 | 1553 | 1466 | 1380 | 1251 | 1164 | 1078 |
8 | 40 | 1800 | 1700 | 1600 | 1450 | 1350 | 1250 |
Sl. No. | Dia of bar (mm) | M35 (mm) | M40 (mm) | M45 (mm) | M50 (mm) | M55 (mm) | ≥ M60 (mm) |
1 | 10 | 592 | 559 | 526 | 477 | 444 | 411 |
2 | 12 | 710 | 671 | 631 | 572 | 533 | 493 |
3 | 16 | 947 | 895 | 842 | 763 | 710 | 658 |
4 | 20 | 1184 | 1118 | 1052 | 954 | 888 | 822 |
5 | 25 | 1480 | 1398 | 1316 | 1192 | 1110 | 1028 |
6 | 32 | 1894 | 1789 | 1684 | 1526 | 1421 | 1316 |
7 | 36 | 2220 | 2097 | 1973 | 1788 | 1665 | 1542 |
8 | 40 | 2574 | 2431 | 2288 | 2074 | 1931 | 1788 |

Reinforcement Lapping Length for 50% Lapping and Grade of Steel Fe500
Sl. No. | Dia of bar (mm) | M35 (mm) | M40 (mm) | M45 (mm) | M50 (mm) | M55 (mm) | ≥ M60 (mm) |
1 | 10 | 504 | 476 | 448 | 406 | 378 | 350 |
2 | 12 | 605 | 571 | 538 | 487 | 454 | 420 |
3 | 16 | 806 | 762 | 717 | 650 | 605 | 560 |
4 | 20 | 1008 | 952 | 896 | 812 | 756 | 700 |
5 | 25 | 1260 | 1190 | 1120 | 1015 | 945 | 875 |
6 | 32 | 1613 | 1523 | 1434 | 1299 | 1210 | 1120 |
7 | 36 | 1890 | 1785 | 1680 | 1523 | 1418 | 1313 |
8 | 40 | 2191 | 2070 | 1948 | 1765 | 1643 | 1522 |
Sl. No. | Dia of bar (mm) | M35 (mm) | M40 (mm) | M45 (mm) | M50 (mm) | M55 (mm) | ≥ M60 (mm) |
1 | 10 | 721 | 681 | 641 | 581 | 541 | 501 |
2 | 12 | 865 | 817 | 769 | 697 | 649 | 601 |
3 | 16 | 1153 | 1089 | 1025 | 929 | 865 | 801 |
4 | 20 | 1441 | 1361 | 1281 | 1161 | 1081 | 1001 |
5 | 25 | 1802 | 1702 | 1602 | 1451 | 1351 | 1251 |
6 | 32 | 2306 | 2178 | 2050 | 1858 | 1730 | 1602 |
7 | 36 | 2703 | 2553 | 2402 | 2177 | 2027 | 1877 |
8 | 40 | 3134 | 2959 | 2785 | 2524 | 2350 | 2176 |
Reference:
- IRC 112-2011
- IS 456: 2000

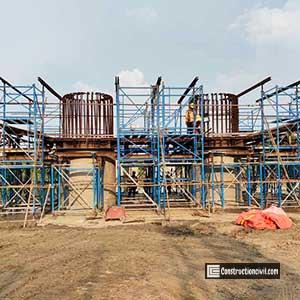
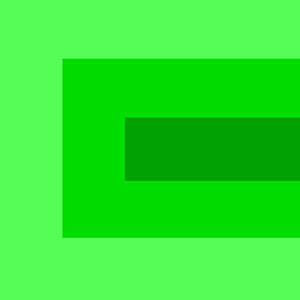