As per the MORTH technical specification, following Test Frequency and Acceptance Criteria of Road Construction Materials are adapted for Flexible Pavements.
Road Construction materials – Tests on soil:
Following test frequency and acceptance criteria of road construction materials are selected for embankment and subgrade construction.
S.NO. | Type of Test | Frequency | Location | Acceptance Criteria |
1.1 |
Borrow Material for Embankment and Subgrade: |
|||
(i) | Sand Content (IS: 2720 Part 4) | Two tests per 3000 cu.m of soil. | Grid the borrow area at 25 m c/c | ย |
(ii) | Plasticity Test (IS: 2720 Part 5) e.g. LL, PL & PI | Two tests per 3000 cu.mย of soil. | Grid the borrow area at 25 m c/c | LL<70%
ย PI<45% |
(iii) | Density Test (IS:2720 Partย 8) | Two tests per 3000 cu.m of soil | Grid the borrow area at 25 m c/c | Max laboratory dry Unit weight
ย Embankments up to 3m height, not subjected to extensive flooding: Not less than 15.2 KN/cu.m. Embankments exceeding 3 m height or any height subject to long periods of inundation: Not less than16.0 KN/cu.m. Sub-grade/earthen shoulder/ verge/backfill : Not less than 17.5 KN/cu.m. |
(iv) | Deleterious content Testย (IS:2720 Part 27); | As and when required by the Engineer. | Grid the borrow area at 25 m c/c | ย |
(v) | Moisture content Testย ย ย ย ย ย ย ย ย ย ย (IS: 2720 Part 2) | One test for every 250 cum of soil. | Inย situ | -2% to+1% of OMC |
(vi) | CBR test on the material to be compacted in the sub-grade on soaked ย samples (IS:2720 Part 16) | One CBR test for every 3000 cum or closer as and when required by the Engineer. | Grid the borrow area at 25 m c/c | Not less than the designed CBR value 8% and 10 % at 97% of MDD (4 days soaked value) |
1.2 | Compaction control (IS:2720 Part 28) on each layer
ย (MORTH Spec. 903.2.2 |
One Density test for each 1000 sq.m of compacted area for the body of the embankment, to be increased to one ย test per 500 sq.m of compacted area for sub-grade i.e. top 500 mm portion of embankment [1.65- {1.65/(no of the sample)^0.5}] times the standard deviation | In situ | Relative compaction asย %ย of max. laboratory dry density
ย Embankment not less than 95% Sub-grade/earthen shoulder not less thanย 97% |
1.3 | Surfaceย Levels
ย (MORTH Spec. 902.3) |
Every 10 m interval | In situ | Sub-Grade
ย + 20mm to (-) 25mm |
2.0
GSB and WMM Road Construction Materials:
Granular Sub Base(GSB) is road construction materials. It is known asย subbase, which is the layer of aggregate material placed on the subgrade, on which the WMM layer as a base course is found.
S.NO. | Type of Test | Frequency | Location | Acceptance Criteria |
2.1 |
GSB Material: |
|||
(i) | Gradation (IS: 2720 Part 4 as per job mix formula | One test per 200 cu.m | Stock Yard/In situ | As per Table 400- 1 of MORTH Specs for R & B Works. |
(ii) | Atterberg Limit (IS:2720 Part 5) | One test per 200 cu.m | Stock Yard/In situ | LL & P.I. not more than 25 and 6% respectively. |
(iii) | Moisture content prior to compaction (IS:2720 Part 28) | One test per 250 sq.m. | In situ | OMC โ2% to OMC + 1% |
(iv) | The density of the compacted layer (IS:2720 Part 28) | One test per 500 sq.m | In situ | Mean density not less than the specified density + [1.65- {1.65/(no of the sample)^0.5}] times the standard deviation |
(v) | Deleterious (IS:2720 Part 27) | As required | Stock Yard/In situ |
– |
(vi) | C.B.R. (IS:2720 Part 16) | As required | Stock Yard/ In situ | Not less thanย 30% |
(vii) | Water absorption (IS: 2386 Part III) | As required | Stock Yard/In situ | 2% maximum.
ย If this value is more than 2%, the soundness test to be carried out. |
(viii) | Soundness (IS:2386 Part 5) | As required | Stock Yard/ In situ | 12%ย maximum with Na2 So4,
ย 18% with Magnesium Sulphateย |
(ix) | 10% Fines Value of Coarse aggregate BS 812 (Part-111) | As required | Stock Yard/In situ | 50 KN or more in soaked condition |
(xi) | Surface Level MORTH, Spec. 902.3 | Every 10 m interval | In situ | + 10mm to โ20 mm |
2.2 |
WMM Material: |
|||
(i) | Aggregate Impact Value (IS:2386 Part 4) | One test per 200 cum of aggregate | In situ | Max. 30%. |
(ii) | Grading (IS: 2720 Part 4) | One test per 100 cum of aggregate | In situ | As per Table 400-11 of MOSRT&H Specs |
(iii) | Flakiness and Elongation Index (IS:2386 Part 1) | One test per 200 cum of aggregate | In situ | Max. 30% |
(iv) | Atterberg limits of the portion of aggregate passing 425-micron sieve (IS:2720 Part 5) | One test per 100 cum of aggregate | In situ | Not Exceeding (PI) 6% |
(v) | The density of the compacted layer (IS:2720 Part 8) | One test per 500 sqm. |
– |
At least 98% of the max. dry density. |
(vi) | Abrasion value
ย (IS:2386 Part 4) |
As required | In situ | Max.ย 40% |
(vii) | Fractured Faces | As required | In situ | 90% of material > 4.75 mm size shall have at least 2 fractured faces. |
(viii) | Water absorption | As required | In situ | Max.ย 2%.
ย Soundness test to be conducted in case water absorption is more than 2%. |
(ix) | Surface Level (MORTH Spec. 902.3) | Every 10 m interval | In situ | + 10mm |
Also, Read: Concrete Subbase Course – DLC Construction
3.0
Road Constructionย – Tests on Bitumen Materials:
Bitumen is a black, sticky, viscous liquid or semi-solid material derived from crude oil. It is generally found in natural organic deposits or may be a refined petroleum product. Bitumen is the essential road construction materials for flexible pavement.
S.
ย NO. |
Type of Construction | Test | Location | Acceptance Criteria |
3.1 |
Prime Coat and Tack Coat: |
|||
(i) | Quality of binder (IS:73,217 & 8887) | Number of samples per lot and tests as per IS:73, IS:217 and IS:8887 as applicable | HM Plant | Bitumen Emulsion complying with IS:8887 of a type and grade as specified in the contract or as directed by Engineer. |
(ii) | Temp. of the binder for application | At the regular close interval |
Insitu |
– |
(iii) | Rate of spread of binder | Not less than 2 tests per day; One test per ย 500 sq.m. | Insitu | 6-9 kg/10 sq.m of liquid bituminous material for a prime coat over the surface of low porosity.
ย 2.5-3.0 Kg/10 sq.m. of liquid bituminous material for tack coat. |
(iv) | Quality of Application | As required | Insitu | No pools
ย No dry spots Evenly applied |
3.2 |
Dense Bituminous Macadam (DBM) and Bituminous Concrete (BC): |
|||
(i) | Quality of binder (IS:73,217 & 8887) | Number of samples per lot and tests as per IS: 73, IS:217 and IS: 8887 as applicable | HM Plant | Bitumen Emulsion complying with IS:73 of a type and grade as specified in the contract or as directed by Engineer |
(ii) | Aggregate Impact Value / Los Angles Abrasion Value (IS:2386 Part 4) | One test per 50 cum. of aggregate | HM Plant | Aggregate Impact Value
ย DBM 27% max. BC 24% max Los Angeles Abrasion Value DBM 35% max BC 30% max |
(iii) | Flakiness Indexย & Elongation Index (IS:2386 Part 1) | One test per 50 cum. of aggregate | HM Plant/stockyard | Max. 30% |
(iv) | Stripping value (IS:6241) | Initially one test of 3 representative specimens for each source of supply. Subsequently when warranted by changes in the quality of aggregates. | HM Plant/stockyard | Minimum retained coating ofย Bitumen Aggregate Mixtures 95% |
(v) | Water absorption of aggregate (IS:2386 Part 3) | Initially one test of 3 representative specimens for each source of supply. Subsequently when warranted by changes in the quality of aggregates. | HM Plant | Max. 2% for DBM
ย Max. 1% for BC |
(vi) | Soundness (Magnesium and sodium sulphate) (IS:2386 Part 5) | Initially, one determination by each method for each source of supply, then as warranted by a change in the quality of the aggregates. | HM Plant/stockyard | SodiumSulphate
ย 12% max. Magnesium Sulphateย ย ย ย ย ย ย ย ย 18% max. |
(vii) | Sand equivalent test for fine aggregate
ย (IS:2720 Part 37) |
As required | HM Plant | Not less than 50 |
(viii) | Plasticity Index (IS:2720 Part 5) | As required | HM Plant | Not more than 4% for fraction passing 0.425mm sieve |
(ix) | Stone Polish Test (BS 812ย Part โ 114) | As required, for Bituminous Concrete. | HM Plant | 55 minimum (for BC) |
(x) | Percentage of fractured facesย ย ย ย ย (IS:2386 part-I) | When gravel is used, one test per 50 cum of aggregate. | HM Plant | When crushed gravel is proposed for use, not less than 90% by weight of the crushed material retained on the 4.75mm sieve shall have at least two fractured faces |
(xi) | Mix grading | One set of tests on individual constituents and mixed aggregate from the drier for every 400 tonnes of mix subject to a minimum of two tests per plant per day. | HM Plant | The combined grading for the particular mixture shall be within the limits given in Table 500.10 of MORTH, Specs. for R & B. Works when tested in accordance with IS:2386 Part I for DBM & Table 500 โ 18 for BC. |
(xii) | Stability of mix | For every 400 tonnes of mix produced, a set of 3 Marshall specimens to be prepared and tested for stability, flow value, density and void content subject to a minimum of two sets being tested per plant per day. | HM Plant | As per Table 500.11 for DBM and Table 500.19 for BC of MORTH Specs for R & B Works. |
(xiii) | Water sensitivity of mix (Retained tensile strength) โ AASHTOย T 283 | Initially one test of 3 representative specimens for each source of supply. Subsequently when warranted by changes in the quality of aggregates (if required) | HM Plant | 80% minย DBM & BC |
(xiv) | Swell test on the mix | As required for the Bituminous Concrete | HM Plant | Refer Section 6.18 of MS2. Applicableย only to Hveem Method of Mix Design |
(xv) | Control of the temperature of binder in the boiler, aggregate in the dryer and mix at the time of laying and rolling.
ย MORTH Spec. Clause 501.3 and Table 500-5 |
At a regular close interval | HM Plant | Bitumen mixing temp 150-165ยฐC
ย Aggregate mixing temp 150-170ยฐC Mixed Material 165ยฐC max. Laying: 125oC min. temp. on Rolling 90ยฐC min. |
(xvi) | Control of binder content and grading of the mix. | One test for every 400 tonnes of mix subject to a minimum of two tests per day per plant. | ย | As shown in Table 500-10 for DBM and Table 500-18 for BC of MORTH, Specs for R&B Works. |
(xvii) | Rate of spread of mixed material | Regular control through checks on the weight of mixed material and layer thickness | ย | Hot-mix pant of adequate capacity and capable of yielding a mix of proper and uniform quality with thoroughly coated aggregates. |
(xviii) | The density of the compacted layer | One test per 700 sq.m area [1.65- {1.65/(no of the sample)^0.5}] times the standard deviation | In situ | 92% of the theoretical maximum specific gravity of the loose mix (Gmm) |
(xix) | Coating and stripping of bitumen aggregate mixtures IS:6241. | As required | HM Plant | Min 95% coating retained. |
(xx) | Surface levels
ย (MORTH Spec. 902.3) |
As required | Insitu | + ย 6 mm |
3.3 |
Modified Binder: |
|||
(i) | Softening point (IS:1205) | Initially on submission, thereafter daily if site blended, weekly if preblended. | HM Plant | As specified in Table 500-44, 500-45 and 500-46 of MOSRT&H Specs. |
(ii) | Penetration at 25ยฐC and 4ยฐC
ย (IS: 1203 and IS: 1205 respectively) |
Initially on submission, thereafter daily if site blended, weekly if preblended. | HM Plant | As specified in Table 500-44, 500-45 and 500-46 of MOSRT&H Specs. |
(iii) | Elastic Recovery (ASTM D 5976) | Initially on submission, thereafter daily if site blended, weekly if preblended. | HM Plant | As specified in Table 500-44, 500-45 and 500-46 of MOSRT&H Specs |
(iv) | Ductility (IS:1208) | Initially on submission, thereafter daily if site blended, weekly if preblended. | HM Plant | As specified in Table 500-44, 500-45 and 500-46 of MOSRT&H Specs |
(v) | Flashpoint (IS:1209) | Initially on submission, thereafter daily if site blended, weekly if preblended. | HM Plant | As specified in Table 500-44, 500-45 and 500-46 of MOSRT&H Specs |
(vi) | Fraass Breaking Point (IS:9381) | Initially on submission | HM Plant | As specified in Table 500-44, 500-45 and 500-46 of MOSRT&H Specs of modifier used. |
(vii) | Viscosity at 150ยฐC (IS:1206) | Initially on submission, | HM Plant | As specified in Table 500-44, 500-45 and 500-46 of MOSRT&H Specs |
(viii) | Thin-film oven test, penetration, softening point, elastic recovery of residue, loss on heating.ย ย ย ย (IS: 9382). | Initially on submission, | HM Plant | As specified in Table 500-44, 500-45 and 500-46 of MOSRT&H Specs |

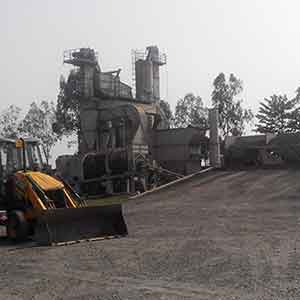
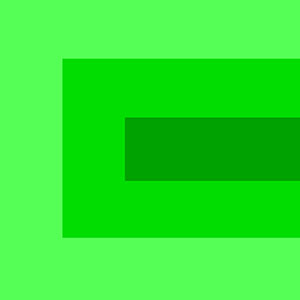