What is Corrosion?
The process of creation of rust over the surface of reinforcement is known as corrosion which converts a pure metal to a more chemically stable form. Rusting of iron rebar is a natural process and which results in the depassivation of the reinforcing steel. Corrosion of steel reinforcement in concrete is one of the most inherent and common mechanisms of deterioration for concrete structures.
What is Corrosion Process?
- Chloride ions slowly penetrate the concrete when a concrete structure is exposed to the atmosphere.
- Finally, the chloride ions reach the reinforcement bar and accumulate beyond a certain concentration level, at which the protective film is destroyed. After that, the steel begins to rust in the presence of oxygen and moisture.
- In the case of reinforced concrete structures, due to the rusting of iron rebar, its section decreases gradually.
- Iron oxide (Rust) resulting in reinforced concrete structures increase internal stresses in the concrete, which may lead to deterioration of concrete. Rusting of iron rebar is a very common problem in RCC construction work.
Also, Read: Nondestructive Testing of Concrete – Methods & Guidelines
Reduction of the structural capacity Due to Rusting of Iron Rebar:
Reduction of the structural capacity of reinforced concrete elements affected by rebar corrosion is mainly due to the following three main phenomena, which are the direct consequence of corrosion:
- Reduction of the cross section section due to rusting of iron rebar.
- Reduction of bond strength of concrete because of the rusting of iron rebar.
- Loss of concrete integrity because of cover cracking and spalling after rusting of iron.
However, rusting of iron rebar can occur in two significant situations, which are as follows.
- Carbonation of Concrete
- Chloride Contamination in Concrete
Also, Read: Nondestructive Testing of Concrete – Methods & Guidelines
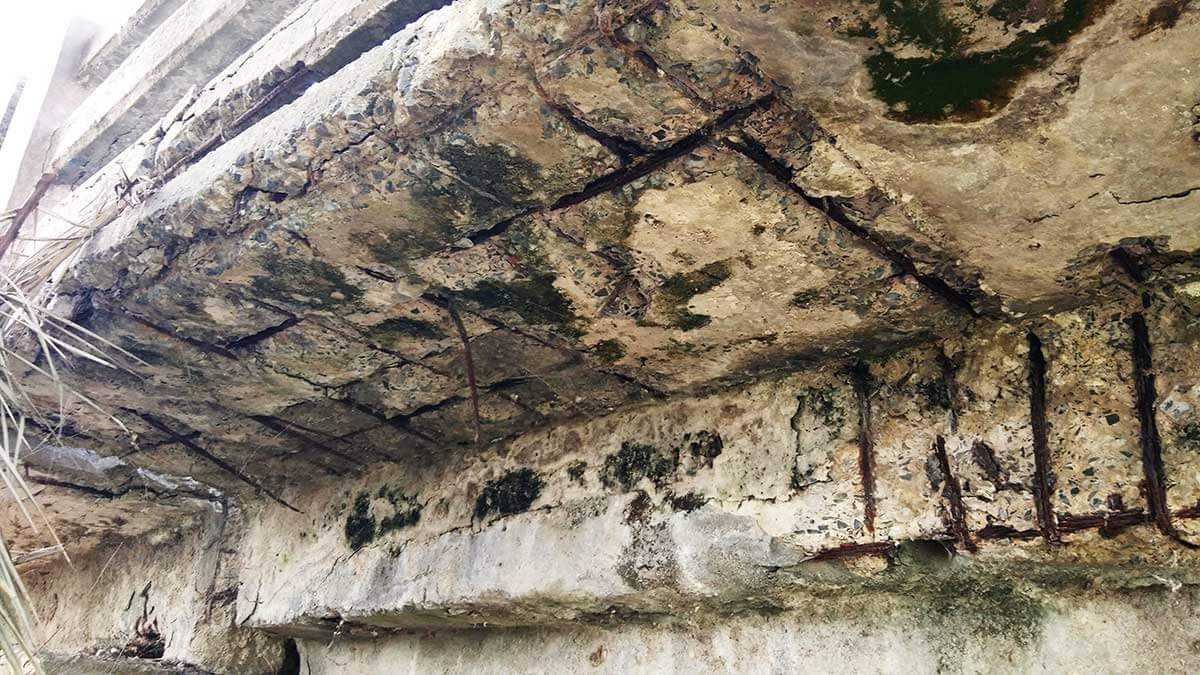
Also, Read: Blowholes/Surface voids/Bugholes in Concrete Surface
Basic Causes of Corrosion:
Carbonation of Concrete:
The carbonation of concrete is a natural chemical process where atmospheric carbon dioxide penetrates the concrete through its pore and neutralizes the alkalinity of concrete. Carbonation of concrete reduces the PH value of concrete to around 8.0-9.0, which lead to destroying the oxide film of the reinforcement bar. The overall process of carbon dioxide penetration is known as the carbonation of concrete.
- After oxide film damage, the rusting of the iron rebar process will start, with an adequate supply of oxygen and moisture.
- The penetration of carbon dioxide by carbonation is a prolonged process and determined by the rate at which carbon dioxide penetrates the concrete.
- The rate of penetration fundamentally depends on the porosity and permeability of the concrete.
- It is rarely a problem on structures which are constructed with good quality concrete maintaining the adequate depth of cover as specified in the design.
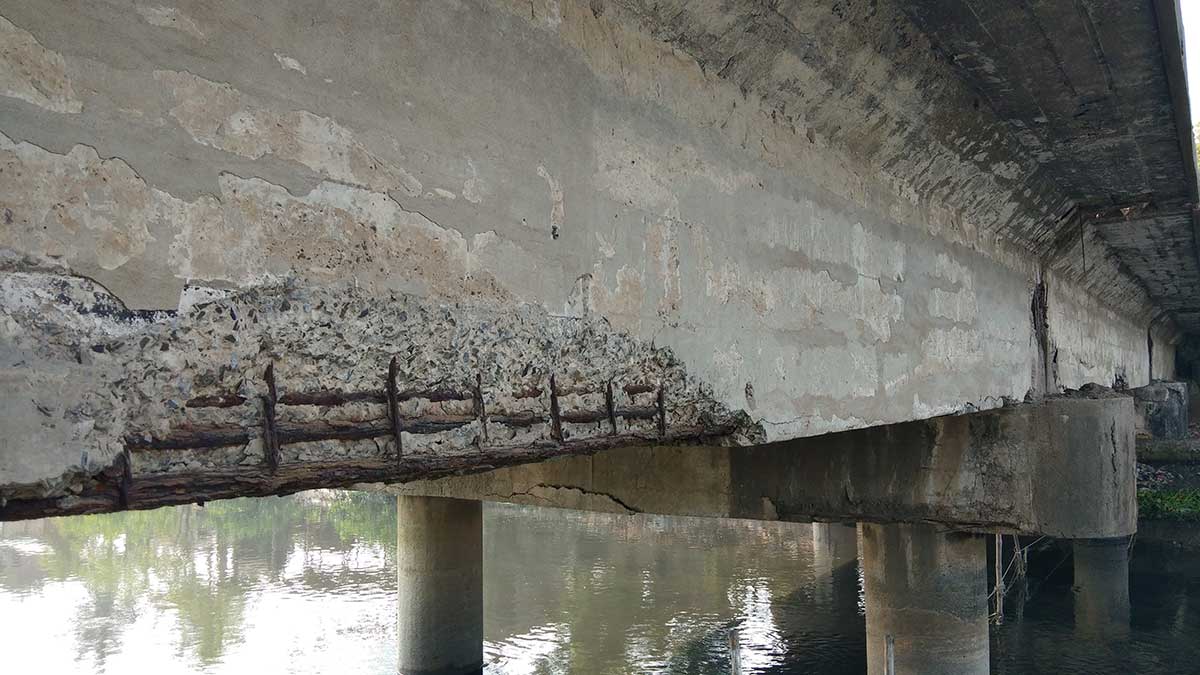
Also, Read: What is Prestressing of Concrete? – Method with Calculation
Chloride Attack on Concrete:
Chloride attack on concrete is another natural chemical process where chloride ions enter into the concrete from the atmosphere or from the chloride-containing admixtures that are used to accelerate curing. If the chloride ion concentration is high, they disrupt the passive film of reinforcing steel and subjected to corrosion. The above process is known as chloride attack on concrete.
- The levels of chloride required to initiate corrosion process are extremely low. Study shows that a threshold concentration of about 0.026% is sufficient to break down the passive film of reinforcement.
- The corrosion process/Rusting of iron is the same after break down of passive film of reinforcement as the carbonation of concrete.
- The rate of carbonation directly dependent on the water-cement ratio, i.e., the higher the ratio, the greater is the depth of carbonation.
Repair of Corrosion affected Concrete:
Material for Repair and Maintenance: The materials used for concert repair are generally cement-based or Epoxy-based. The following materials are used for repairing of the severely corrosion damaged concrete member.
- Cement/Sand mortars
- Polymer Latex
- Epoxy Resins
- Polyester Resins
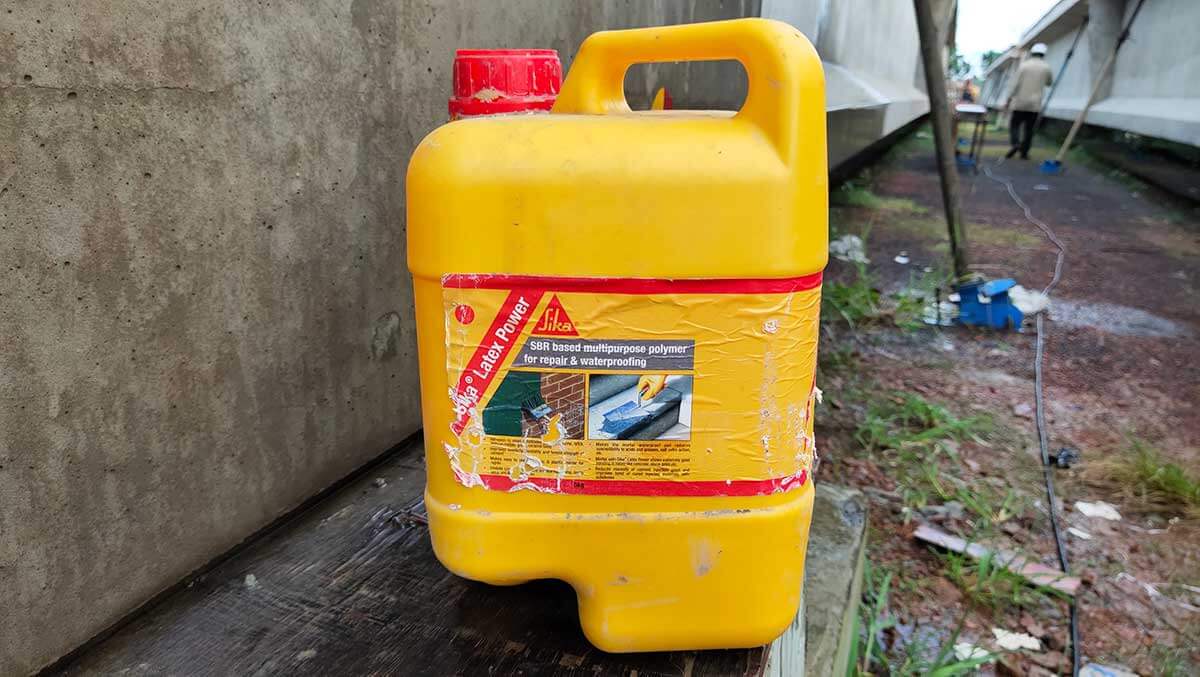
Also, Read: Causes, Prevention and Repair of Concrete Surface Defects
Special Repair Method of Corrosion Affected Concrete:
Surface Preparation:
- Staging with the necessary platform to facilitate work adjacent to the distressed portion shall be done.
- The Damaged / loose concrete should be removed carefully by chisel and hammer or by the breaker. It is to remember that direct hammering should not be allowed.
- Clean the surfaces by use of high-pressure water blower and removal of loose adhering materials.
- The existing dust / loose particle / spalled concrete from the existing surface may be cleaned by gentle hammering if flakes are observed and by wire brushing only.
Application of Polymer Modified Mortar:
- After cleaning off corrosion affected Concrete surface apply one coat of polymer bonding agent in the proportion of 1:0.5 (i.e. Polymer: Cement by wt.) over the cleaned concrete surface.
- Repairing work involves providing and applying single component, fibre reinforced high-performance polymer modified mortar on cleaned concrete surfaces of wall, bottom slab and other surfaces of the existing structure. The mortar should develop compressive strength up to 20MPa in 3 days.
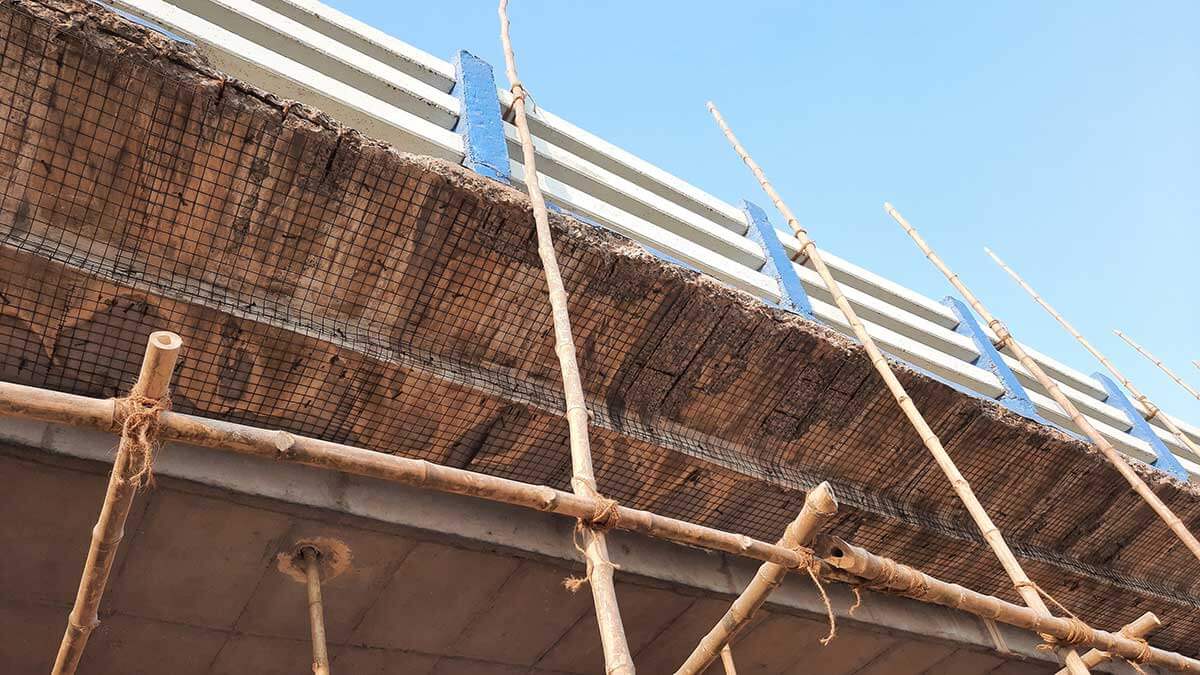
Also, Read: Formula for Development Length, Anchorage and Lapping Length
Removing Rusting from Reinforcement:
- The existing exposed corrosion affected reinforcements should be cleaned by gentle hammering if flakes are observed and by wire brushing only.
- Exposed reinforcements are to be cleaned and rust to be removed by use of Corrosion Removing Gel.
- Corroded reinforcement/Rusting of iron is to be repaired with Anti-corrosive paint.
- Moderate repair and preventive paintings are to be done to enhance the service life of the structure.
Large Volume Repair:
- After completion of cleaning, formwork will be fixed in position as per the site requirement.
- By application of acrylic polymer based bonding agents, it is to ensure that proper bonding between old and new concrete.
- A dual shrinkage-compensating, high flow, high strength ready to use micro concrete should be poured in the formwork to patch the damaged concrete surface.
- The same should be finished maintaining line and level with the existing finish of the RCC member.
- Curing of concrete should be done at least for three days with water.
Stitching and Sealing of Concrete Cracks:
- After groove cutting, clean the same by use of high-pressure water blower and removal of loose adhering materials from the concrete surface.
- Proper groove cutting should be done all along the stitch line so that the stainless steel stitching bar can be embedded from all sides.
- Providing and stitching the cracks of the RCC/Brick wall with 6 mm dia stainless steel bar as per the direction of Engineer in charge. Epoxy-based mortar is to be used to fix the bar into the hole of RCC or brick wall.
Also, Read: Environment Health and Safety(EHS)

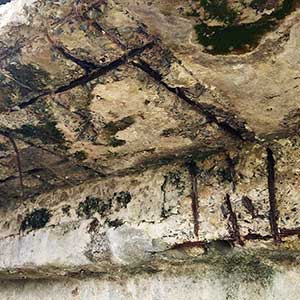
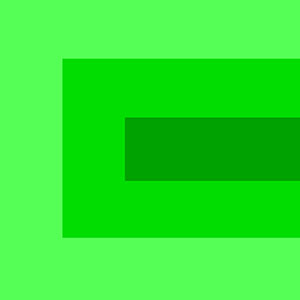